3D tisk nebo aditivní výroba je proces vytváření trojrozměrných pevných objektů z digitálního souboru.
vytvoření 3D tištěného objektu je dosaženo pomocí aditivních procesů. V aditivním procesu je objekt vytvořen položením po sobě jdoucích vrstev materiálu, dokud není objekt vytvořen. Každá z těchto vrstev může být viděna jako tenký řez průřezu objektu.
3D tisk je opakem subtraktivní výroby, která vyřezává / vydlabává kus kovu nebo plastu například frézkou.
3D tisk umožňuje vytvářet složité tvary s použitím méně materiálu než tradiční výrobní metody.
náš newsletter je zdarma & můžete se kdykoli odhlásit.
jak funguje 3D tisk?
vše začíná 3D modelem. Můžete se rozhodnout vytvořit jeden od základu nebo si jej stáhnout z 3D knihovny.
3D Software
k dispozici je mnoho různých softwarových nástrojů. Od průmyslového stupně po open source. Vytvořili jsme přehled na naší 3D softwarové stránce.
často doporučujeme začátečníkům začít s Tinkercadem. Tinkercad je zdarma a funguje ve Vašem prohlížeči, nemusíte jej instalovat do počítače. Tinkercad nabízí lekce pro začátečníky a má vestavěnou funkci pro export vašeho modelu jako Soubor pro tisk, např.STL nebo .OBJEKT.
Nyní, když máte tisknutelný soubor, je dalším krokem jeho příprava pro 3D tiskárnu. Tomu se říká krájení.
krájení: Z tisknutelného souboru na 3D tiskárnu
krájení v podstatě znamená krájení 3D modelu na stovky nebo tisíce vrstev a provádí se krájecím softwarem.
když je váš soubor nakrájen na plátky, je připraven pro vaši 3D tiskárnu. Podávání souboru do tiskárny lze provést přes USB, SD nebo Wi-Fi. Váš nakrájený soubor je nyní připraven k 3D tisku vrstvu po vrstvě.
3D tiskový průmysl
přijetí 3D tisku dosáhlo kritického množství, protože ti, kteří ještě neintegrovali aditivní výrobu někde ve svém dodavatelském řetězci, jsou nyní součástí stále se zmenšující menšiny. Tam, kde byl 3D tisk vhodný pouze pro prototypování a jednorázovou výrobu v raných fázích, se nyní rychle mění na výrobní technologii.
většina současné poptávky po 3D tisku je průmyslového charakteru. Acumen Research and Consulting předpovídá, že globální trh 3D tisku dosáhne do roku 2026 41 miliard dolarů.
jak se vyvíjí, technologie 3D tisku je určena k transformaci téměř každého významného odvětví a ke změně způsobu, jakým žijeme, pracujeme a hrajeme v budoucnu.
příklady 3D tisku
3D tisk zahrnuje mnoho forem technologií a materiálů, protože 3D tisk se používá téměř ve všech průmyslových odvětvích, na která si vzpomenete. Je důležité vidět to jako shluk různých průmyslových odvětví s nesčetnými různými aplikacemi.
několik příkladů:
- – spotřební zboží (brýle, obuv, design, nábytek)
- – průmyslové výrobky (výrobní nástroje, prototypy, funkční části pro konečné použití)
- -zubní výrobky
- – protetika
- – architektonické modely v měřítku & makety
- – rekonstrukce fosilií
- – replikace starověkých artefaktů
- – rekonstrukce důkazů ve forenzní patologii
- – filmové rekvizity
rapid prototyping & Rapid manufacturing
společnosti používaly 3d tiskárny ve svém procesu návrhu vytvářet prototypy od konce sedmdesátých let. Použití 3D tiskáren pro tyto účely se nazývá rychlé prototypování.
Proč používat 3D tiskárny pro rychlé prototypování?
stručně řečeno: je to rychlé a relativně levné. Od nápadu, přes 3D model až po držení prototypu ve vašich rukou je otázkou dnů místo týdnů. Iterace jsou jednodušší a levnější a nepotřebujete drahé formy nebo nástroje.
kromě rychlého prototypování se 3D tisk používá také pro rychlou výrobu. Rapid manufacturing je nový způsob výroby, kde podniky používají 3D tiskárny pro krátkodobou / malosériovou zakázkovou výrobu.
Automotive
výrobci automobilů již dlouhou dobu využívají 3D tisk. Automobilové společnosti tisknou náhradní díly, nástroje, přípravky a přípravky, ale také díly pro konečné použití. 3D tisk umožnil výrobu na vyžádání, což vedlo k nižším zásobám a zkrátilo konstrukční a výrobní cykly.
automobiloví nadšenci po celém světě používají 3D tištěné díly k obnově starých automobilů. Jedním z takových příkladů je, když Australští inženýři vytiskli díly, aby oživili Delage Type-C. Přitom museli tisknout díly, které byly desítky let mimo výrobu.
letectví
letecký průmysl používá 3D tisk mnoha různými způsoby. Následující příklad představuje významný milník ve výrobě 3D tisku: GE Aviation má 3D vytištěno 30 000 palivových trysek kobaltu a chromu pro své letecké motory LEAP. Dosáhli tohoto milníku v říjnu 2018 a vzhledem k tomu, že vyrábějí 600 týdně na čtyřiceti 3D tiskárnách, je to pravděpodobně mnohem vyšší než nyní.
asi dvacet jednotlivých dílů, které dříve musely být svařeny dohromady, bylo sloučeno do jedné 3D tištěné součásti, která váží o 25% méně a je pětkrát silnější. LEAP engine je díky své vysoké účinnosti nejprodávanějším motorem v leteckém průmyslu a GE ušetří 3 miliony dolarů na letadlo 3D tiskem palivových trysek, takže tato jediná 3D tištěná část generuje stovky milionů dolarů finančního přínosu.
palivové trysky GE se také dostaly do Boeingu 787 Dreamliner, ale není to jediná 3D tištěná část v 787. 33 centimetrů dlouhé konstrukční kování, které drží zadní kuchyňskou kuchyň k draku letadla, je 3D vytištěno společností s názvem Norsk Titanium. Norsk se rozhodl specializovat na Titan, protože má velmi vysoký poměr pevnosti k hmotnosti a je poměrně drahý, což znamená, že snížení odpadu umožněné 3D tiskem má významnější finanční dopad než ve srovnání s levnějšími kovy, kde se náklady na materiální odpad snáze absorbují. Spíše než slinování kovového prášku laserem jako většina kovových 3D tiskáren používá Norsk Merke 4 plazmový oblouk k roztavení kovového drátu v procesu zvaném Rychlé ukládání plazmy (forma nasměrovaného ukládání energie), který může uložit až 10 kg titanu za hodinu. 2kg Titanová část by obecně vyžadovala 30kg blok titanu, který by ji obrobil, generování 28kg odpadu, ale 3D tisk stejné části vyžaduje pouze 6kg titanového drátu.
stavba
je možné budovu vytisknout? – Ano, je. 3D tištěné domy jsou již komerčně dostupné. Některé společnosti tisknou díly montované a jiné to dělají na místě.
většina konkrétních tiskových příběhů, na které se podíváme na této webové stránce, je zaměřena na rozsáhlé betonové tiskové systémy s poměrně velkými tryskami pro velký průtok. Je to skvělé pro pokládku betonových vrstev poměrně rychlým a opakovatelným způsobem. Ale pro skutečně složité konkrétní práci, která umožňuje plné využití možností 3D tisku vyžaduje něco trochu hbitější, a jemnější dotek.
spotřební zboží
když jsme poprvé začali blogovat o 3D tisku v roce 2011, 3D tisk nebyl připraven k použití jako výrobní metoda pro velké objemy. V současné době existuje mnoho příkladů konečného použití 3D tištěných spotřebních výrobků.
obuv
řada 4D Adidas má plně 3d tištěnou mezipodešev a je vytištěna ve velkých objemech. Udělali jsme článek tehdy, vysvětlující, jak Adidas zpočátku uvolňoval jen 5,000 párů bot pro veřejnost, a měl za cíl prodat 100,000 párů am-infused designs do 2018.
se svými nejnovějšími iteracemi boty se zdá, že tento cíl překonali nebo jsou na cestě k jeho překonání. Boty jsou k dispozici po celém světě z místních obchodů Adidas a také z různých online prodejen 3. strany.
brýle
předpokládá se, že trh 3D tištěných brýlí dosáhne do roku 2028 3,4 miliardy dolarů. Rychle rostoucí část je část rámců pro konečné použití. 3D tisk je zvláště vhodnou výrobní metodou pro rámy brýlí, protože měření jednotlivce se v konečném produktu snadno zpracovávají.
ale věděli jste, že je také možné 3D tisk objektivů? Tradiční skleněné čočky nezačínají tenké a lehké; jsou vyříznuty z mnohem většího bloku materiálu zvaného blank, z nichž asi 80% jde do odpadu. Když vezmeme v úvahu, kolik lidí nosí brýle a jak často potřebují získat nový pár, 80% těchto čísel je spousta odpadu. Kromě toho musí laboratoře udržovat obrovské zásoby polotovarů, aby vyhověly potřebám vlastních vizí svých klientů. Konečně však technologie 3D tisku pokročila natolik, aby poskytla vysoce kvalitní vlastní oční čočky, čímž se zbavila nákladů na odpad a zásoby minulosti. Tiskárna Luxexcel VisionEngine 3D používá UV-vytvrditelný akrylátový monomer k tisku dvou párů čoček za hodinu, které nevyžadují žádné leštění ani následné zpracování jakéhokoli druhu. Ohniskové oblasti lze také zcela přizpůsobit tak, aby určitá oblast objektivu mohla poskytovat lepší jasnost na dálku, zatímco jiná oblast objektivu poskytuje lepší vidění zblízka.
šperky
existují dva způsoby výroby šperků s 3D tiskárnou. Můžete použít přímý nebo nepřímý výrobní proces. Přímý odkazuje na vytvoření objektu přímo z 3D návrhu, zatímco nepřímá výroba znamená, že objekt (vzor), který je 3D vytištěn, se nakonec použije k vytvoření formy pro investiční lití.
zdravotnictví
v dnešní době není neobvyklé vidět titulky o 3D tištěných implantátech. Často jsou tyto případy experimentální, což může vypadat, že 3D tisk je stále okrajovou technologií v lékařském a zdravotnickém sektoru, ale už tomu tak není. Za posledních deset let bylo více než 100 000 náhrad kyčle 3D vytištěno společností GE Additive.
pohár Delta-TT navržený Dr. Guido Grappiolo a LimaCorporate jsou vyrobeny z trabekulárního titanu, který se vyznačuje pravidelnou trojrozměrnou hexagonální buněčnou strukturou, která napodobuje morfologii trabekulární kosti. Trabekulární struktura zvyšuje biokompatibilitu titanu podporou růstu kostí do implantátu. Některé z prvních implantátů Delta-TT jsou stále silné o deset let později.
další 3D tištěná zdravotnická součást, která dělá dobrou práci, že je nezjistitelná, je sluchadlo. Téměř každé sluchadlo za posledních 17 let bylo 3D vytištěno díky spolupráci mezi Společností Materialise a Phonak. Phonak vyvinul Rapid Shell Modeling (RSM) v roce 2001. Před RSM, výroba jednoho sluchadla vyžadovala devět pracných kroků zahrnujících ruční sochařství a výrobu forem, a výsledky byly často špatně padnoucí. S RSM, technik používá silikon, aby udělal dojem zvukovodu, tento dojem je naskenován 3D, a po nějakém drobném vyladění je model 3D vytištěn pryskyřičnou 3D tiskárnou. Elektronika se přidá a pak je odeslána uživateli. Pomocí tohoto procesu jsou každý rok vytištěny stovky tisíc sluchadel 3D.
zubní
v zubním průmyslu vidíme formy pro jasné zarovnání, které jsou možná nejvíce 3D tištěnými objekty na světě. V současné době se formy tisknou 3D tiskem na bázi pryskyřice i prášku, ale také tryskáním materiálu. Korunky a zubní protézy jsou již přímo 3D vytištěny spolu s chirurgickými průvodci.
Biotisk
od prvních dvou tisíc technologií 3D tisku byly studovány biotechnologickými firmami a akademickou obcí pro možné použití v aplikacích tkáňového inženýrství, kde jsou orgány a části těla postaveny pomocí inkoustových technik. Vrstvy živých buněk se ukládají na gelové médium a pomalu se vytvářejí trojrozměrné struktury. Na tuto oblast výzkumu odkazujeme termínem: biotisk.
potraviny
aditivní výroba napadla potravinářský průmysl už dávno. Restaurace jako Food Ink a Melisse to používají jako jedinečné prodejní místo k přilákání zákazníků z celého světa.
vzdělávání
pedagogové a studenti již dlouho používají 3D tiskárny ve třídě. 3D tisk umožňuje studentům zhmotnit své nápady rychlým a cenově dostupným způsobem.
zatímco aditivní výrobní specifické tituly jsou poměrně nové, univerzity již dlouho používají 3D tiskárny v jiných oborech. Existuje mnoho vzdělávacích kurzů, které lze absolvovat s 3D tiskem. Univerzity nabízejí kurzy o věcech, které sousedí s 3D tiskem, jako je CAD a 3D design, které lze v určité fázi aplikovat na 3D tisk.
pokud jde o prototypování, mnoho univerzitních programů se obrací na tiskárny. Existují specializace v aditivní výroby lze dosáhnout prostřednictvím architektury nebo průmyslového designu stupňů. Tištěné prototypy jsou také velmi běžné v umění, animace a módní studie.
typy technologií a procesů 3D tisku
americká společnost pro testování a materiály (ASTM) vyvinula soubor norem, které klasifikují aditivní výrobní procesy do 7 kategorií. Jedná se o:
- DPH Fotopolymerace
- stereolitografie (SLA)
- digitální zpracování světla (DLP)
- kontinuální výroba kapalinového rozhraní (klip)
- tryskání materiálu
- tryskání pojiva
- vytlačování materiálu
- modelování taveného nanášení (FDM)
- výroba taveného vlákna (FFF)
- práškové lože Fusion
- Multi Jet Fusion (MJF)
- selektivní laserové slinování (SLS)
- přímé kovové laserové slinování (DMLS)
- laminace plechu
- řízená energetická depozice
Fotopolymerace DPH
3D tiskárna založená na metodě Fotopolymerace DPH má nádobu naplněnou fotopolymerní pryskyřicí. Pryskyřice je vytvrzena UV světelným zdrojem.
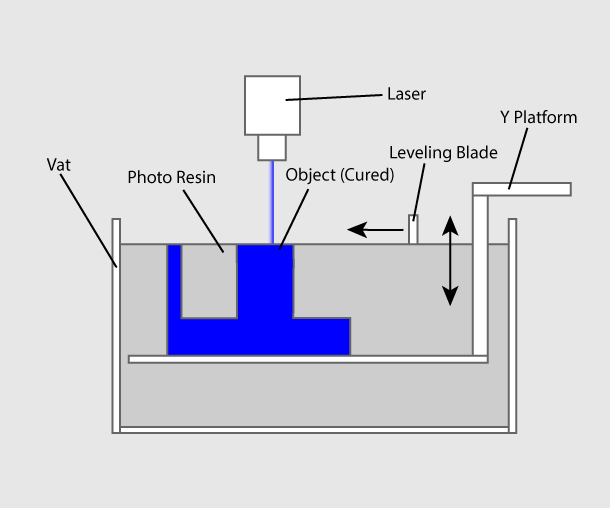
stereolitografie (SLA)
SLA byla vynalezena v roce 1986 Charlesem Hullem, který také v té době založil společnost 3D Systems. Stereolitografie využívá kádě kapalné vytvrditelné fotopolymerní pryskyřice a ultrafialového laseru k vytvoření vrstev objektu po jednom. Pro každou vrstvu laserový paprsek sleduje průřez vzoru dílu na povrchu kapalné pryskyřice. Vystavení ultrafialovému laserovému světlu vytvrzuje a ztuhne vzorek vysledovaný na pryskyřici a spojí ji s níže uvedenou vrstvou.
po vysledování vzoru sestupuje plošina výtahu SLA o vzdálenost rovnající se tloušťce jedné vrstvy, typicky 0,05 mm až 0,15 mm(0,002 „až 0,006“). Poté čepel naplněná pryskyřicí zametá přes průřez dílu a znovu jej potáhne čerstvým materiálem. Na tomto novém povrchu kapaliny je sledován následující vzor vrstvy, který spojuje předchozí vrstvu. V závislosti na orientaci tisku objektu & vyžaduje SLA často použití podpůrných struktur.
digitální zpracování světla (DLP)
DLP nebo digitální zpracování světla označuje způsob tisku, který využívá světlo a fotosenzitivní polymery. I když je velmi podobný SLA, klíčovým rozdílem je světelný zdroj. DLP využívá jiné světelné zdroje, jako jsou obloukové lampy. DLP je relativně rychlý ve srovnání s jinými technologiemi 3D tisku.
Continuous Liquid Interface Production (CLIP)
jeden z nejrychlejších procesů využívajících Fotopolymerizaci DPH se nazývá CLIP, zkratka pro kontinuální výrobu kapalinového rozhraní, vyvinutá společností Carbon.
digitální syntéza světla
srdcem procesu klipu je technologie Digitální syntézy světla. V této technologii světlo z vlastního vysoce výkonného LED světelného motoru promítá sled UV obrazů vystavujících průřez 3D tištěné části, což způsobuje, že UV vytvrditelná pryskyřice částečně vytvrzuje přesně řízeným způsobem. Kyslík prochází okénkem propustným pro kyslík a vytváří tenké kapalné rozhraní nevytvrzené pryskyřice mezi oknem a tištěnou částí známou jako mrtvá zóna. Mrtvá zóna je tenká jako deset mikronů. Uvnitř mrtvé zóny kyslík zakazuje světlo vytvrzovat pryskyřici umístěnou nejblíže k oknu, což umožňuje nepřetržitý tok kapaliny pod tištěnou částí. Těsně nad mrtvou zónou UV promítané světlo nahoru způsobuje kaskádu, jako je vytvrzení součásti.
pouhý tisk samotným hardwarem Carbonu neumožňuje vlastnosti konečného použití s aplikacemi v reálném světě. Jakmile světlo tvaruje součást, druhý programovatelný proces vytvrzování dosahuje požadovaných mechanických vlastností pečením 3D tištěné části v termální lázni nebo peci. Naprogramované tepelné vytvrzování nastavuje mechanické vlastnosti spuštěním sekundární chemické reakce, která způsobí, že materiál posílí dosažení požadovaných konečných vlastností.
komponenty potištěné technologií Carbon jsou na stejné úrovni jako vstřikované díly. Digitální syntéza světla vytváří konzistentní a předvídatelné mechanické vlastnosti a vytváří části, které jsou skutečně izotropní.
tryskání materiálu
v tomto procesu se materiál nanáší v kapkách tryskou s malým průměrem, podobně jako běžná inkoustová tiskárna papíru, ale nanáší se vrstva po vrstvě na stavební platformu a poté se vytvrdí UV světlem.
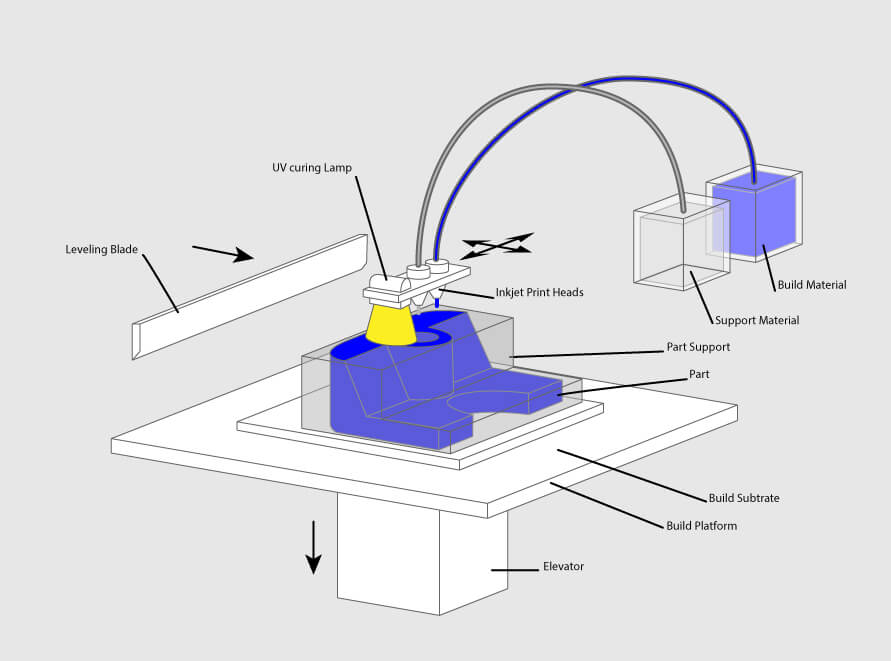
tryskání pojiva
s tryskáním pojiva se používají dva materiály: práškový základní materiál a kapalné pojivo. Ve stavební komoře se prášek rozprostírá ve stejných vrstvách a pojivo se nanáší tryskovými tryskami ,které“ lepí “ částice prášku v požadovaném tvaru. Po dokončení tisku se zbývající prášek vyčistí, což lze často znovu použít k tisku dalšího objektu. Tato technologie byla poprvé vyvinuta na Massachusetts Institute of Technology v roce 1993.
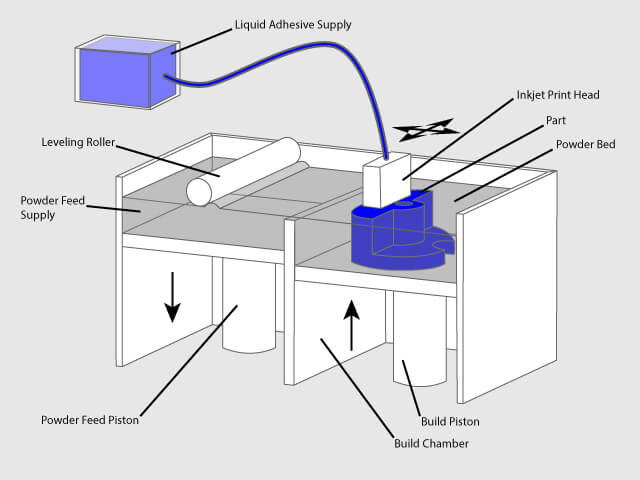
vytlačování materiálu
modelování taveného nanášení (FDM)
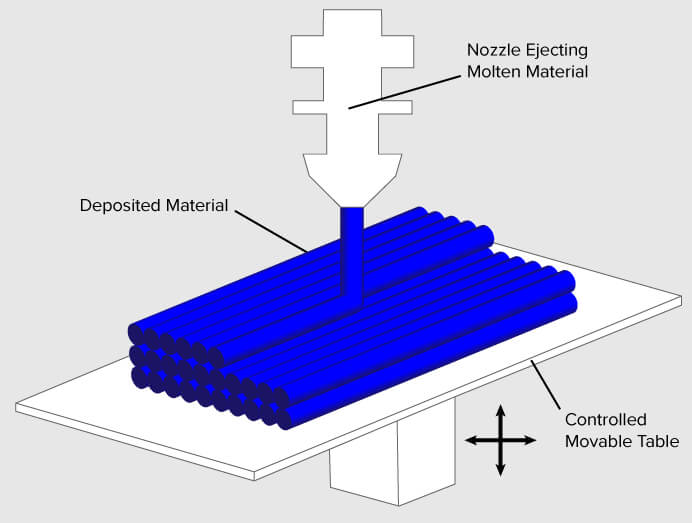
FDM pracuje s použitím plastového vlákna, které se odvíjí od cívky a je dodáváno do vytlačovací trysky, která může zapnout a vypnout tok. Tryska se zahřívá k roztavení materiálu a může se pohybovat v horizontálním i vertikálním směru číslicově řízeným mechanismem. Předmět se vyrábí vytlačováním roztaveného materiálu za vzniku vrstev, jak materiál ztvrdne bezprostředně po vytlačování z trysky.
FDM vynalezl Scott Crump na konci 80. let. Po patentování této technologie založil v roce 1988 společnost Stratasys. Termín tavené depozice modelování a jeho zkratka pro FDM jsou ochrannou známkou Stratasys Inc.
výroba taveného vlákna (FFF)
přesně ekvivalentní termín, výroba taveného vlákna (FFF), byl vytvořen členy projektu RepRap, aby poskytl frázi, která by byla právně neomezená v jeho použití.
fúze práškového lože
selektivní laserové slinování (SLS)
SLS používá vysoce výkonný laser k fúzi malých částic prášku do hmoty, která má požadovaný trojrozměrný tvar. Laser selektivně fúzuje prášek nejprve skenováním průřezů (nebo vrstev) na povrchu práškového lože. Po skenování každého průřezu se práškové lože sníží o jednu tloušťku vrstvy. Poté se nahoře nanese nová vrstva materiálu a proces se opakuje, dokud není objekt dokončen.
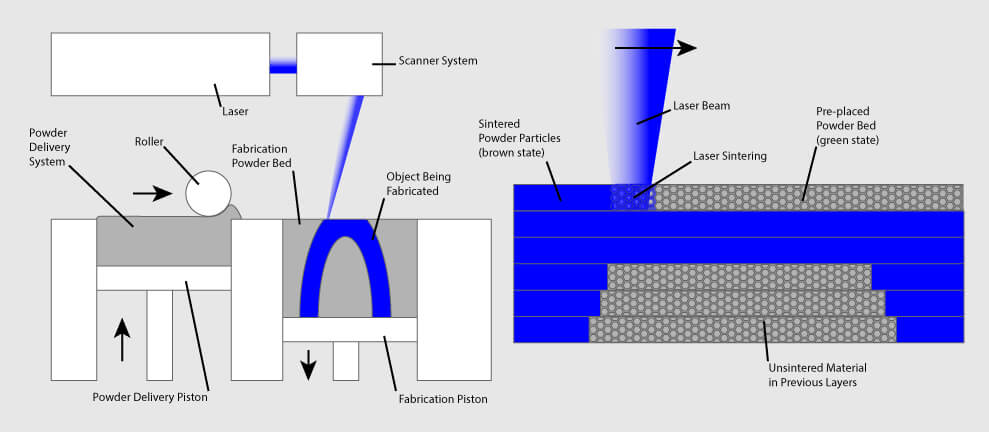
Multi Jet Fusion (MJF)
technologie Multi Jet Fusion byla vyvinuta společností Hewlett Packard a pracuje s zametacím ramenem, které ukládá vrstvu prášku, a poté s dalším ramenem vybaveným inkoustovými tryskami, které selektivně nanáší pojivo na materiál. Inkoustové trysky také ukládají kolem pojiva podrobný prostředek, aby byla zajištěna přesná dimenzionalita a hladké povrchy. Nakonec je vrstva vystavena výbuchu tepelné energie, která způsobuje reakci činidel.
přímé kovové laserové slinování (DMLS)
DMLS je v podstatě stejné jako SLS, ale místo toho používá kovový prášek. Veškerý nepoužitý prášek zůstává tak, jak je, a stává se nosnou strukturou objektu. Nepoužitý prášek lze znovu použít pro další tisk.
díky zvýšenému výkonu laseru se DMLS vyvinul do procesu tavení laserem. Přečtěte si více o tom a dalších kovových technologiích na naší stránce s přehledem kovových technologií.
laminace plechu
laminace plechu zahrnuje materiál v listech, který je vázán spolu s vnější silou. Listy mohou být kovové, papírové nebo polymerní. Plechy jsou svařeny dohromady ultrazvukovým svařováním ve vrstvách a poté CNC frézovány do správného tvaru. Papírové listy mohou být také použity, ale jsou lepeny lepidlem a řezány do tvaru přesnými čepelemi.
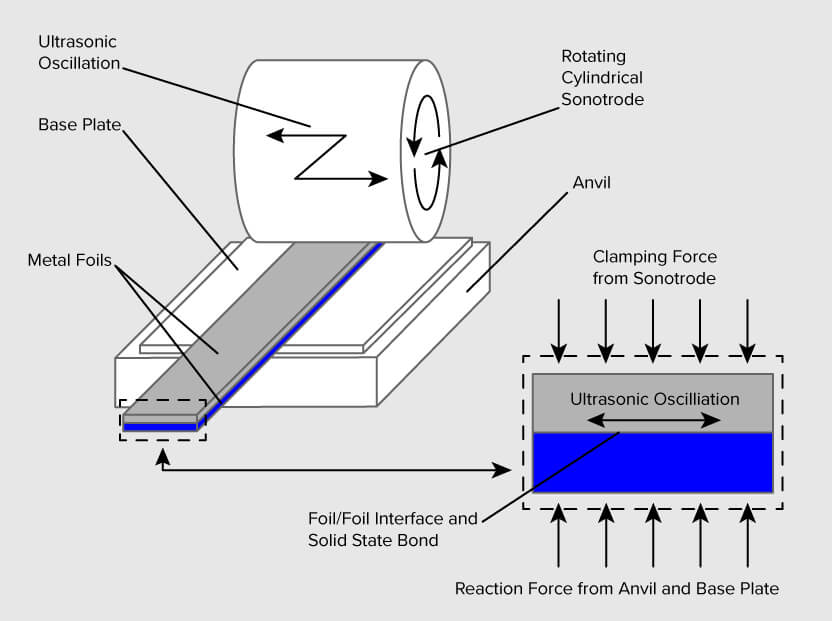
řízená energetická depozice
tento proces se většinou používá v kovoprůmyslu a v rychlých výrobních aplikacích. 3D tiskové zařízení je obvykle připojeno k víceosému robotickému rameni a sestává z trysky, která ukládá kovový prášek nebo drát na povrch a zdroje energie (laser, elektronový paprsek nebo plazmový oblouk), který jej roztaví a vytvoří pevný předmět.
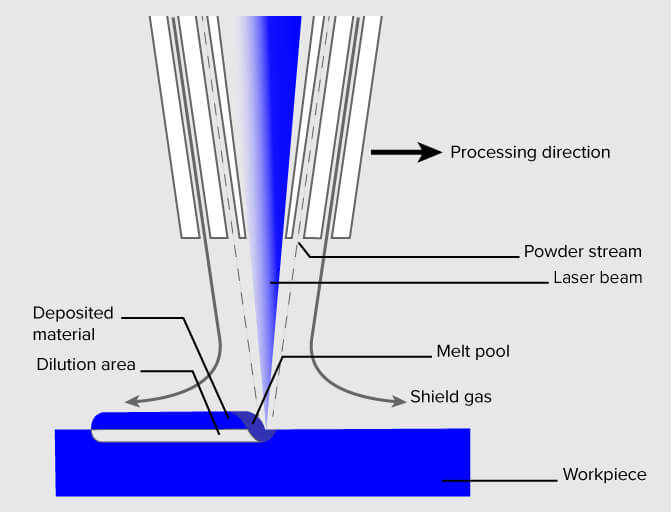
materiály
při výrobě aditiv lze použít více materiálů: plasty, kovy, beton, keramika, papír a některé jedlé látky (např. čokoláda). Materiály se často vyrábějí v drátěných surovinách alias vláknech, práškové formě nebo kapalné pryskyřici. Další informace o našich doporučených materiálech najdete na stránce materiály.
služby
chcete implementovat 3D tisk ve vašem výrobním procesu? Získejte nabídku na vlastní část nebo objednejte vzorky na naší stránce služby 3D tisku.