3D-udskrivning eller additivfremstilling er en proces til fremstilling af tredimensionelle faste genstande fra en digital fil.
oprettelsen af et 3D-trykt objekt opnås ved hjælp af additive processer. I en additivproces oprettes et objekt ved at lægge successive lag af materiale, indtil objektet oprettes. Hvert af disse lag kan ses som et tyndt skåret tværsnit af objektet.
3D-udskrivning er det modsatte af subtraktiv fremstilling, der skærer / udhuler et stykke metal eller plast med for eksempel en fræsemaskine.
3D-udskrivning giver dig mulighed for at fremstille komplekse former ved hjælp af mindre materiale end traditionelle fremstillingsmetoder.
vores nyhedsbrev er gratis & du kan afmelde dig når som helst.
Hvordan fungerer 3D-udskrivning?
det hele starter med en 3D-model. Du kan vælge at oprette en fra bunden eller hente den fra et 3D-bibliotek.
3D-programmer
der er mange forskellige værktøjer til rådighed. Fra industriel kvalitet til open source. Vi har lavet en oversigt på vores 3D-programside.
vi anbefaler ofte begyndere at starte med Tinkercad. Tinkercad er gratis og fungerer i din bro.ser, du behøver ikke at installere det på din computer. Tinkercad tilbyder begynderundervisning og har en indbygget funktion til at eksportere din model som en udskrivbar fil f.eks .STL eller .OBJ.
nu hvor du har en udskrivbar fil, er det næste trin at forberede den til din 3d-printer. Dette kaldes skæring.
udskæring: Fra udskrivbar fil til 3d-Printer
skæring betyder grundlæggende at skære en 3d-model i hundreder eller tusinder af lag og udføres med skæreprogrammer.
når din fil er skåret, er den klar til din 3d-printer. Tilførsel af filen til din printer kan ske via USB, SD eller trådløs internetadgang. Din skivede fil er nu klar til at blive 3D-trykt lag for lag.
3D-trykkeri
vedtagelse af 3D-udskrivning har nået kritisk masse, da de, der endnu ikke har integreret additivfremstilling et eller andet sted i deres forsyningskæde, nu er en del af et stadigt faldende mindretal. Hvor 3D-udskrivning kun var egnet til prototyping og engangsproduktion i de tidlige stadier, omdannes den nu hurtigt til en produktionsteknologi.
det meste af den nuværende efterspørgsel efter 3D-udskrivning er industriel. Acumen Research and Consulting forudsiger, at det globale 3D-udskrivningsmarked når 41 milliarder dollars inden 2026.
efterhånden som den udvikler sig, er 3D-udskrivningsteknologi bestemt til at transformere næsten enhver større industri og ændre den måde, vi lever, arbejder og spiller på i fremtiden.
eksempler på 3D-udskrivning
3D-udskrivning omfatter mange former for teknologier og materialer, da 3D-udskrivning bruges i næsten alle brancher, du kunne tænke på. Det er vigtigt at se det som en klynge af forskellige industrier med et utal af forskellige applikationer.
et par eksempler:
- – forbrugerprodukter (briller, fodtøj, design, møbler)
- – industriprodukter (fremstillingsværktøjer, prototyper, funktionelle slutdele)
- -tandprodukter
- – proteser
- – arkitektoniske skalamodeller & maketter
- – rekonstruktion af fossiler
- – replikering af gamle artefakter
- – rekonstruktion af beviser i retsmedicinsk patologi
- – filmrekvisitter
rapid prototyping & rapid manufacturing
virksomheder har brugt 3D– printere i deres designproces at skabe prototyper siden slutningen af halvfjerdserne. Brug af 3D-printere til disse formål kaldes rapid prototyping.
Hvorfor bruge 3D-printere til Rapid Prototyping?
kort sagt: det er hurtigt og relativt billigt. Fra ide til 3D-model til at holde en prototype i dine hænder er et spørgsmål om dage i stedet for uger. Iterationer er lettere og billigere at lave, og du har ikke brug for dyre forme eller værktøjer.
udover hurtig prototyping bruges 3D-udskrivning også til hurtig fremstilling. Rapid manufacturing er en ny fremstillingsmetode, hvor virksomheder bruger 3D-printere til kort sigt / lille batch brugerdefineret fremstilling.
Automotive
bilproducenter har brugt 3D-udskrivning i lang tid. Automotive virksomheder udskriver reservedele, værktøj, jigs og inventar, men også slutbrug dele. 3D-udskrivning har muliggjort on-demand-produktion, hvilket har ført til lavere lagerniveauer og har forkortet design-og produktionscyklusser.
bilentusiaster over hele verden bruger 3D-trykte dele til at gendanne gamle biler. Et sådant eksempel er, når Australske ingeniører trykte dele for at bringe en Delage Type-C tilbage til livet. Dermed måtte de udskrive dele, der var ude af produktion i årtier.
luftfart
luftfartsindustrien bruger 3D-udskrivning på mange forskellige måder. Følgende eksempel markerer en betydelig milepæl for fremstilling af 3D-udskrivning: GE Aviation har 3D-trykt 30.000 kobolt-krom brændstofdyser til sine LEAP-flymotorer. De opnåede denne milepæl i Oktober 2018, og i betragtning af at de producerer 600 om ugen på fyrre 3D-printere, er det sandsynligvis meget højere end det nu.
omkring tyve individuelle dele, der tidligere skulle svejses sammen, blev konsolideret til en 3D-trykt komponent, der vejer 25% mindre og er fem gange stærkere. LEAP-motoren er den bedst sælgende motor i luftfartsindustrien på grund af dens høje effektivitetsniveau, og GE sparer $3 millioner pr.fly ved 3D-udskrivning af brændstofdyserne, så denne enkelt 3D-trykte del genererer hundreder af millioner af dollars økonomisk fordel.
GE ‘ s brændstofdyser kom også ind i Boeing 787 Dreamliner, men det er ikke den eneste 3D-trykte del i 787. De 33 centimeter lange strukturelle fittings, der holder den bageste køkkenkabinet til flyrammen, er 3D-trykt af et firma kaldet Norsk Titanium. Norsk valgte at specialisere sig i titanium, fordi det har et meget højt styrke-til-vægt-forhold og er ret dyrt, hvilket betyder, at reduktionen i affald muliggjort af 3D-udskrivning har en større økonomisk indvirkning end sammenlignet med billigere metaller, hvor omkostningerne ved materialeaffald er lettere at absorbere. I stedet for at sintre metalpulver med en laser som de fleste metal 3D-printere bruger Norsk Merke 4 en plasmabue til at smelte en metaltråd i en proces kaldet hurtig Plasmaaflejring (en form for Rettet Energiaflejring), der kan deponere op til 10 kg titanium i timen. En 2 kg titandel kræver generelt en 30 kg titaniumblok for at bearbejde den fra, hvilket genererer 28 kg affald, men 3D-udskrivning af den samme del kræver kun 6 kg titantråd.
byggeri
er det muligt at udskrive en bygning? – jo, det er. 3D-trykte huse er allerede kommercielt tilgængelige. Nogle virksomheder udskriver dele prefab og andre gør det på stedet.
de fleste af de konkrete trykhistorier, vi ser på på denne hjemmeside, er fokuseret på store betontryksystemer med ret store dyser til en stor strømningshastighed. Det er fantastisk til at lægge betonlag på en ret hurtig og gentagelig måde. Men for virkelig indviklet betonarbejde, der gør fuld brug af mulighederne i 3D-udskrivning, kræver noget lidt mere smidigt og med et finere touch.
forbrugerprodukter
da vi først begyndte at blogge om 3D-udskrivning tilbage i 2011, var 3D-udskrivning ikke klar til at blive brugt som produktionsmetode til store mængder. I dag er der adskillige eksempler på slutbrug 3D-trykte forbrugerprodukter.
Fodtøj
Adidas’ 4D-serie har en fuldt 3D-trykt mellemsål og bliver trykt i store mængder. Vi lavede en artikel dengang og forklarede, hvordan Adidas oprindeligt frigav kun 5.000 par af skoene til offentligheden og havde til formål at sælge 100.000 par af AM-infused designs inden 2018.
med deres seneste iterationer af skoen ser det ud til, at de har overgået dette mål eller er på vej til at overgå det. Skoene er tilgængelige over hele verden fra lokale Adidas butikker og også fra forskellige 3.parts online forretninger.
briller
markedet for 3D-trykte briller forventes at nå 3,4 milliarder dollars i 2028. Et hurtigt voksende afsnit er slutanvendelsesrammer. 3D-udskrivning er en særlig velegnet produktionsmetode til brillestel, fordi målingerne af en person er lette at behandle i slutproduktet.
men vidste du, at det også er muligt at 3D-printe linser? Traditionelle glaslinser starter ikke tynde og lette; de er skåret fra en meget større blok af materiale kaldet et tomt, hvoraf 80% går til spilde. Når vi overvejer, hvor mange mennesker der bærer briller, og hvor ofte de har brug for at få et nyt par, er 80% af disse tal meget spild. Oven i købet, laboratorier er nødt til at holde enorme varebeholdninger af emner for at imødekomme deres kunders brugerdefinerede visionsbehov. Endelig er 3D-udskrivningsteknologi imidlertid avanceret nok til at levere brugerdefinerede oftalmiske linser af høj kvalitet og fjerne fortidens affald og lageromkostninger. Den luksuriøse VisionEngine 3D-printer bruger en UV-hærdelig acrylatmonomer til at udskrive to par linser i timen, der ikke kræver polering eller efterbehandling af nogen art. Fokusområderne kan også tilpasses fuldstændigt, så et bestemt område af linsen kan give bedre klarhed på afstand, mens et andet område af linsen giver bedre syn tæt på.
smykker
der er to måder at producere smykker med en 3d-printer. Du kan enten bruge en direkte eller indirekte produktionsproces. Direkte henviser til oprettelsen af et objekt lige fra 3D-designet, mens indirekte fremstilling betyder, at objektet (mønsteret), der er 3D-trykt, til sidst bruges til at skabe en form til investeringsstøbning.
Healthcare
det er ikke ualmindeligt i disse dage at se overskrifter om 3D-trykte implantater. Ofte er disse tilfælde eksperimentelle, hvilket kan få det til at virke som om 3D-udskrivning stadig er en frynseteknologi inden for medicinsk og sundhedssektoren, men det er ikke tilfældet længere. I løbet af det sidste årti er mere end 100.000 hofteudskiftninger blevet 3D-trykt af GE Additive.
Delta-TT Cup designet af Dr. Guido Grappiolo og LimaCorporate er lavet af trabekulært Titanium, som er kendetegnet ved en regelmæssig, tredimensionel, sekskantet cellestruktur, der efterligner trabekulær knoglemorfologi. Den trabekulære struktur øger titaniumets biokompatibilitet ved at tilskynde til knoglevækst i implantatet. Nogle af de første Delta-TT-implantater kører stadig stærkt over et årti senere.
en anden 3D-trykt sundhedskomponent, der gør et godt stykke arbejde med at være uopdagelig, er høreapparatet. Næsten alle høreapparater i de sidste 17 år er blevet 3D-printet takket være et samarbejde mellem Materialise og Phonak. Phonak udviklede Rapid Shell Modeling (RSM) i 2001. Før RSM krævede fremstilling af et høreapparat ni besværlige trin, der involverede håndskulptur og skimmelfremstilling, og resultaterne var ofte dårligt passende. Med RSM bruger en tekniker silikone til at tage et indtryk af øregangen, det indtryk er 3D-scannet, og efter nogle mindre justeringer er modellen 3D-trykt med en harpiks 3d-printer. Elektronikken tilføjes, og derefter sendes den til brugeren. Ved hjælp af denne proces udskrives hundreder af tusinder af høreapparater hvert år 3d.
Dental
i tandindustrien ser vi forme til klare aligners muligvis de mest 3D-trykte genstande i verden. I øjeblikket er formene 3D-trykt med både harpiks-og pulverbaserede 3D-udskrivningsprocesser, men også via materialestråling. Kroner og proteser er allerede direkte 3D-trykt sammen med kirurgiske guider.
Bio-udskrivning
fra de tidlige to-tusinder 3D-udskrivningsteknologi er blevet undersøgt af biotekfirmaer og Akademia til mulig anvendelse i vævstekniske applikationer, hvor organer og kropsdele er bygget ved hjælp af inkjet-teknikker. Lag af levende celler deponeres på et gelmedium og opbygges langsomt til dannelse af tredimensionelle strukturer. Vi henviser til dette forskningsområde med udtrykket: bioprint.
mad
additivfremstilling invaderede fødevareindustrien for længe siden. Restauranter som Food Ink og Melisse bruger dette som et unikt salgsargument for at tiltrække kunder fra hele verden.
uddannelse
undervisere og studerende har længe brugt 3D-printere i klasseværelset. 3D-udskrivning gør det muligt for eleverne at realisere deres ideer på en hurtig og overkommelig måde.
mens additive fremstillingsspecifikke grader er ret nye, har universiteter længe brugt 3D-printere i andre discipliner. Der er mange uddannelseskurser, man kan tage for at engagere sig i 3D-udskrivning. Universiteter tilbyder kurser om ting, der støder op til 3D-udskrivning som CAD og 3D-design, som kan anvendes til 3D-udskrivning på et bestemt tidspunkt.
med hensyn til prototyping henvender mange universitetsprogrammer sig til printere. Der er specialiseringer i additiv fremstilling man kan opnå gennem arkitektur eller industrielt design grader. Trykte prototyper er også meget almindelige inden for kunst, animation og modestudier.
typer af 3d-Udskrivningsteknologier og-processer
American Society for Testing and Materials (ASTM) udviklede et sæt standarder, der klassificerer additive fremstillingsprocesser i 7 kategorier. Disse er:
- Vat fotopolymerisering
- stereolitografi (SLA)
- Digital lysbehandling (DLP)
- produktion af kontinuerlig flydende grænseflade (klip)
- materiale Jetting
- bindemiddel Jetting
- materiale ekstrudering
- Fused Deposition Modeling (FDM)
- fusioneret Filamentfremstilling (FFF)
- pulver seng Fusion
- Multi Jet Fusion (MJF)
- selektiv Laser sintring (SLS)
- direkte Metal Laser sintring (DMLS)
- laminering af plader
- Directed Energy Deposition
Momsfotopolymerisering
en 3D-printer baseret på Momsfotopolymeriseringsmetoden har en beholder fyldt med fotopolymerharpiks. Harpiksen er hærdet med en UV-lyskilde.
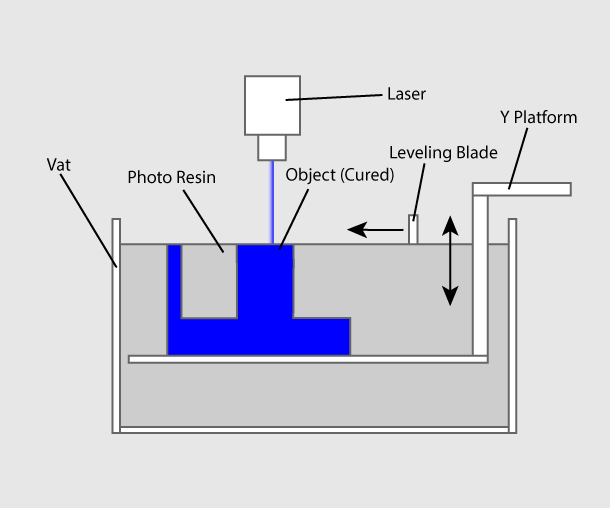
stereolitografi (SLA)
SLA blev opfundet i 1986 af Charles Hull, der også på det tidspunkt grundlagde virksomheden, 3D Systems. Stereolitografi anvender en beholder med flydende hærdelig fotopolymerharpiks og en ultraviolet laser til at bygge objektets lag en ad gangen. For hvert lag sporer laserstrålen et tværsnit af delmønsteret på overfladen af den flydende harpiks. Eksponering for det ultraviolette laserlys hærder og størkner mønsteret, der spores på harpiksen, og smelter det sammen med laget nedenfor.
efter at mønsteret er sporet, falder SLA ‘s elevatorplatform med en afstand svarende til tykkelsen af et enkelt lag, typisk 0,05 mm til 0,15 mm (0,002″ til 0,006″). Derefter fejer et harpiksfyldt blad over delens tværsnit og belægger det igen med frisk materiale. På denne nye flydende overflade spores det efterfølgende lagmønster, der forbinder det foregående lag. Afhængigt af objektet & udskrivningsretning kræver SLA ofte brug af støttestrukturer.
Digital Light Processing (DLP)
DLP eller Digital Light Processing refererer til en metode til udskrivning, der gør brug af lys og lysfølsomme polymerer. Selv om det er meget lig SLA, den vigtigste forskel er lyskilden. DLP udnytter andre lyskilder som arc lamper. DLP er relativt hurtig sammenlignet med andre 3D-udskrivningsteknologier.
kontinuerlig produktion af flydende Interface (CLIP)
en af de hurtigste processer ved hjælp af Momsfotopolymerisering kaldes CLIP, forkortelse for kontinuerlig produktion af flydende Interface, udviklet af Carbon.
Digital Lyssyntese
hjertet i KLIPPROCESSEN er Digital Lyssynteseteknologi. I denne teknologi projicerer lys fra en brugerdefineret højtydende LED-lysmotor en sekvens af UV-billeder, der udsætter et tværsnit af den 3D-trykte del, hvilket får den UV-hærdelige harpiks til delvist at hærde på en nøjagtigt kontrolleret måde. Ilt passerer gennem det iltgennemtrængelige vindue, hvilket skaber en tynd flydende grænseflade af uhærdet harpiks mellem vinduet og den trykte del kendt som dødområdet. Det Døde område er så tyndt som ti mikron. Inde i Det Døde område forbyder ilt lys at hærde harpiksen, der ligger tættest på vinduet, hvilket tillader kontinuerlig strøm af væske under den trykte del. Lige over Det Døde område forårsager UV-projiceret lys opad en kaskade som hærdning af delen.
blot udskrivning med Carbon ‘ s udstyr alene tillader ikke slutanvendelsesegenskaber med virkelige applikationer. Når lyset har formet delen, opnår en anden programmerbar hærdningsproces de ønskede mekaniske egenskaber ved at bage den 3D-trykte del i et termisk bad eller ovn. Programmeret termisk hærdning indstiller de mekaniske egenskaber ved at udløse en sekundær kemisk reaktion, der får materialet til at styrke opnåelsen af de ønskede endelige egenskaber.
komponenter trykt med Carbon ‘ s teknologi er på niveau med sprøjtestøbte dele. Digital Lyssyntese producerer konsistente og forudsigelige mekaniske egenskaber, hvilket skaber dele, der virkelig er isotrope.
materiale Jetting
i denne proces påføres materiale i dråber gennem en dyse med lille diameter, svarende til den måde, en almindelig inkjetpapirprinter fungerer på, men den påføres lag for lag på en byggeplatform og hærdes derefter af UV-lys.
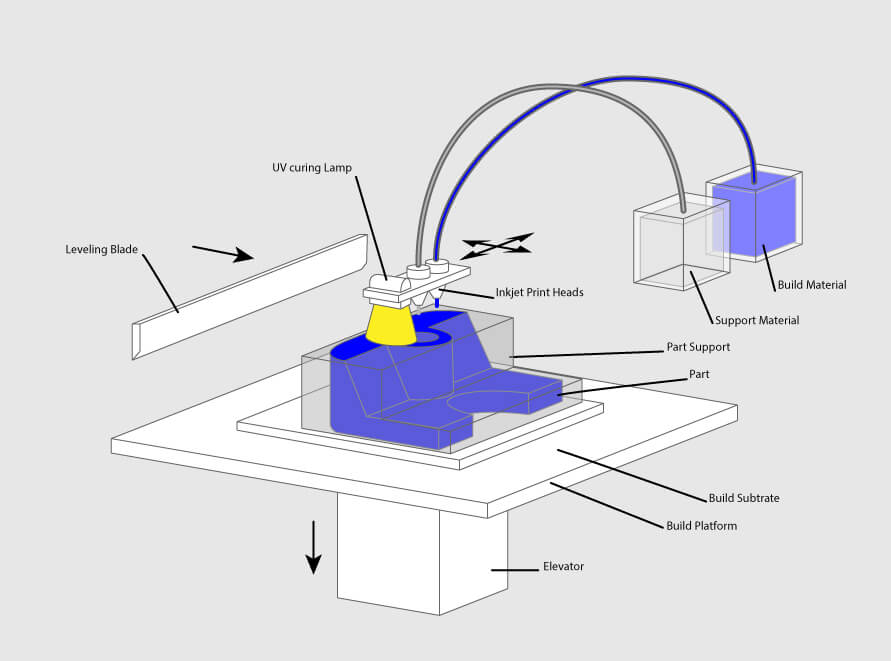
Bindemiddelstråling
med bindemiddelstråling anvendes to materialer: pulverbasemateriale og et flydende bindemiddel. I byggekammeret spredes pulver i lige store lag, og bindemiddel påføres gennem jetdyser, der “limer” pulverpartiklerne i den krævede form. Når udskriften er færdig, renses det resterende pulver, som ofte kan genbruges til at udskrive det næste objekt. Denne teknologi blev først udviklet ved Massachusetts Institute of Technology i 1993.
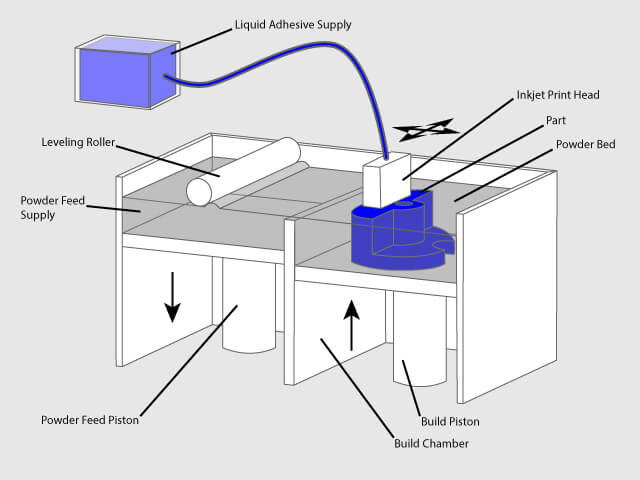
materiale ekstrudering
smeltet Deposition modellering (FDM)
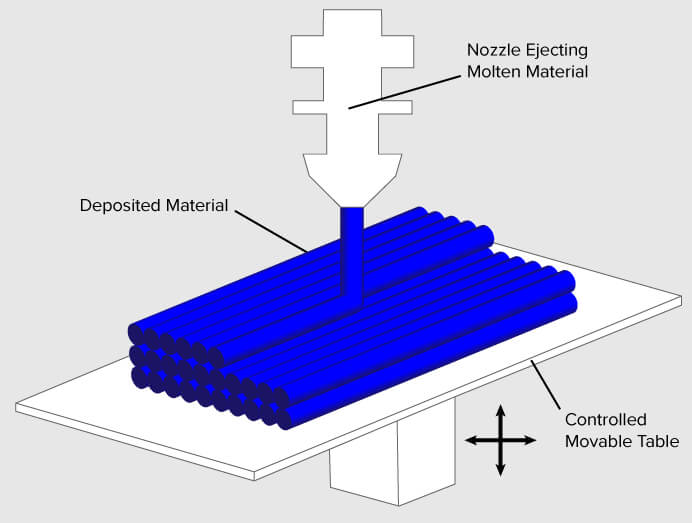
FDM arbejder ved hjælp af et plastfilament, der afvikles fra en spole og leveres til en ekstruderingsdyse, der kan tænde og slukke for strømmen. Dysen opvarmes for at smelte materialet og kan bevæges i både vandret og lodret retning ved hjælp af en numerisk styret mekanisme. Objektet fremstilles ved ekstrudering af smeltet materiale til dannelse af lag, da materialet hærder umiddelbart efter ekstrudering fra dysen.
FDM blev opfundet af Scott Crump i slutningen af 80 ‘ erne. Efter patentering af denne teknologi startede han firmaet Stratasys i 1988. Udtrykket Fused Deposition Modeling og dets forkortelse til FDM er varemærket af Stratasys Inc.
Fused Filament Fabrication (FFF)
det nøjagtigt ækvivalente udtryk, Fused Filament Fabrication (FFF), blev opfundet af medlemmerne af RepRap-projektet for at give en sætning, der ville være juridisk ubegrænset i dens anvendelse.
pulver Bed Fusion
selektiv lasersintring (SLS)
SLS bruger en høj effekt laser til at smelte små partikler af pulver til en masse, der har den ønskede tredimensionelle form. Laseren smelter selektivt pulver ved først at scanne tværsnittene (eller lagene) på overfladen af et pulverleje. Efter hvert tværsnit scannes, sænkes pulverlejet med en lagtykkelse. Derefter påføres et nyt lag af materiale ovenpå, og processen gentages, indtil objektet er afsluttet.
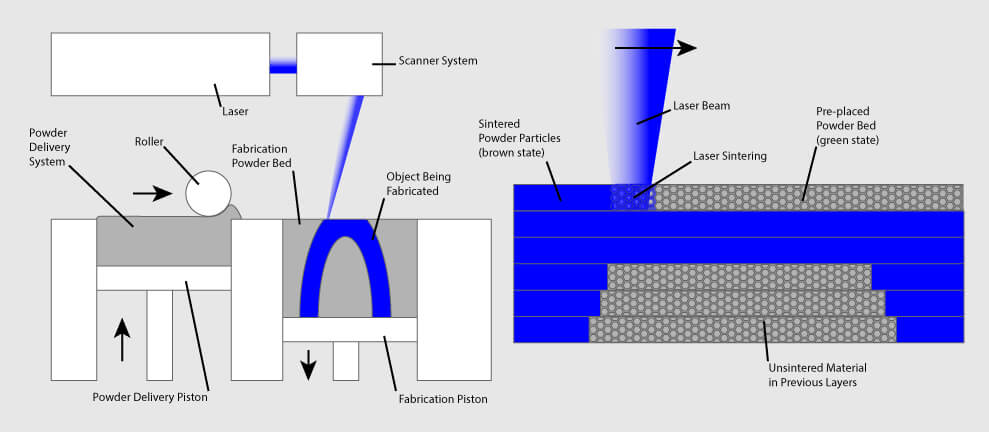
Multi Jet Fusion (MJF)
Multi Jet Fusion technology blev udviklet af Packard og arbejder med en fejende arm, der deponerer et lag pulver og derefter en anden arm udstyret med inkjets, som selektivt anvender et bindemiddel over materialet. Inkjets deponerer også et detaljeringsmiddel omkring bindemidlet for at sikre præcis dimensionalitet og glatte overflader. Endelig udsættes laget for en udbrud af termisk energi, der får agenterne til at reagere.
direkte Metal Laser sintring (DMLS)
DMLS er stort set det samme som SLS, men bruger metalpulver i stedet. Alt ubrugt pulver forbliver som det er og bliver en støttestruktur for objektet. Ubrugt pulver kan genbruges til næste print.
på grund af øget laserkraft har DMLS udviklet sig til en lasersmeltningsproces. Læs mere om det og andre metalteknologier på vores oversigtsside for metalteknologier.
Arklaminering
Arklaminering involverer materiale i ark, der er bundet sammen med ekstern kraft. Ark kan være metal, papir eller en form for polymer. Metalplader svejses sammen ved ultralydssvejsning i lag og derefter CNC fræses til en ordentlig form. Papirark kan også bruges, men de limes af klæbende lim og skæres i form af præcise knive.
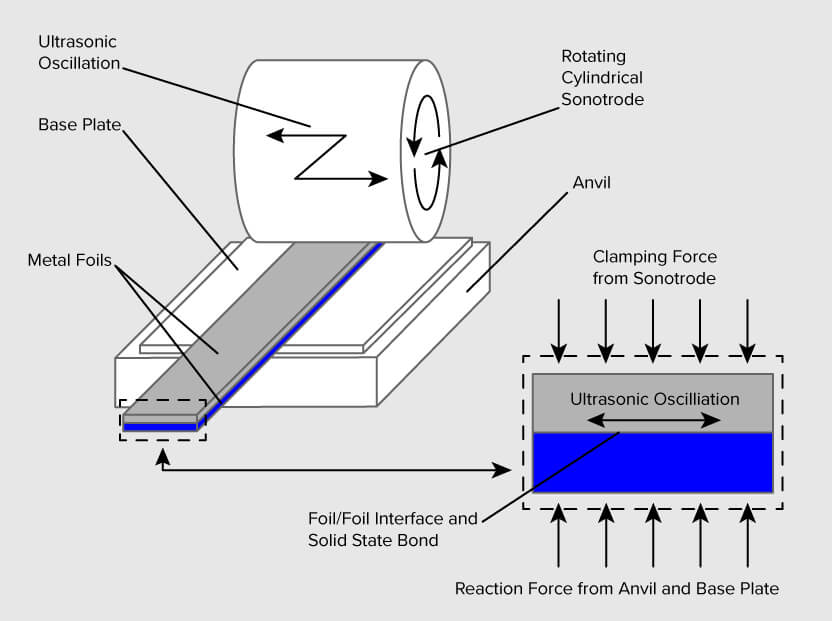
Directed Energy Deposition
denne proces bruges mest i metalindustrien og i hurtige fremstillingsapplikationer. 3D-udskrivningsapparatet er normalt fastgjort til en flerakset robotarm og består af en dyse, der aflejrer metalpulver eller ledning på en overflade og en energikilde (laser, elektronstråle eller plasmabue), der smelter det og danner en fast genstand.
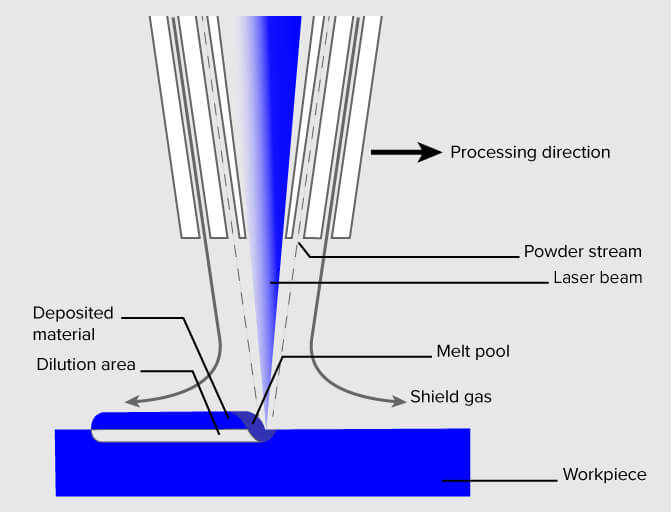
materialer
flere materialer kan anvendes til additivfremstilling: plast, metaller, beton, keramik, papir og visse spiselige stoffer (f.eks. Materialer fremstilles ofte i trådråmateriale, også filament, pulverform eller flydende harpiks. Lær mere om vores fremhævede materialer på vores materialeside.
Services
Ønsker du at implementere 3D-udskrivning i din produktionsproces? Få et tilbud på en brugerdefineret del eller bestil prøver på vores 3D print service side.