L’impression 3D ou fabrication additive est un processus de fabrication d’objets solides tridimensionnels à partir d’un fichier numérique.
La création d’un objet imprimé en 3D est réalisée à l’aide de procédés additifs. Dans un processus additif, un objet est créé en déposant des couches successives de matériau jusqu’à ce que l’objet soit créé. Chacune de ces couches peut être vue comme une section transversale finement découpée de l’objet.
L’impression 3D est l’opposé de la fabrication soustractive qui consiste à découper/évider un morceau de métal ou de plastique avec par exemple une fraiseuse.
L’impression 3D vous permet de produire des formes complexes en utilisant moins de matière que les méthodes de fabrication traditionnelles.
Notre newsletter est gratuite & vous pouvez vous désinscrire à tout moment.
Comment Fonctionne L’Impression 3D?
Tout commence par un modèle 3D. Vous pouvez choisir d’en créer un à partir de zéro ou de le télécharger à partir d’une bibliothèque 3D.
Logiciel 3D
De nombreux outils logiciels sont disponibles. Du niveau industriel à l’open source. Nous avons créé un aperçu sur notre page de logiciels 3D.
Nous recommandons souvent aux débutants de commencer par Tinkercad. Tinkercad est gratuit et fonctionne dans votre navigateur, vous n’avez pas besoin de l’installer sur votre ordinateur. Tinkercad propose des cours pour débutants et dispose d’une fonctionnalité intégrée pour exporter votre modèle sous forme de fichier imprimable, par exemple.STL ou.OBJ.
Maintenant que vous avez un fichier imprimable, l’étape suivante consiste à le préparer pour votre imprimante 3D. C’est ce qu’on appelle le tranchage.
Tranchage: Du fichier imprimable à l’imprimante 3D
Le découpage en tranches signifie essentiellement découper un modèle 3D en centaines ou milliers de couches et se fait avec un logiciel de découpage en tranches.
Lorsque votre fichier est découpé, il est prêt pour votre imprimante 3D. L’alimentation du fichier sur votre imprimante peut se faire via USB, SD ou Wi-Fi. Votre fichier découpé est maintenant prêt à être imprimé couche par couche en 3D.
Industrie de l’impression 3D
L’adoption de l’impression 3D a atteint une masse critique car ceux qui n’ont pas encore intégré la fabrication additive quelque part dans leur chaîne d’approvisionnement font maintenant partie d’une minorité en constante diminution. Là où l’impression 3D ne convenait qu’au prototypage et à la fabrication ponctuelle à ses débuts, elle se transforme rapidement en une technologie de production.
La majeure partie de la demande actuelle d’impression 3D est de nature industrielle. Acumen Research and Consulting prévoit que le marché mondial de l’impression 3D atteindra 41 milliards de dollars d’ici 2026.
À mesure qu’elle évolue, la technologie d’impression 3D est destinée à transformer presque toutes les grandes industries et à changer notre façon de vivre, de travailler et de jouer à l’avenir.
Exemples d’impression 3D
L’impression 3D englobe de nombreuses formes de technologies et de matériaux, car l’impression 3D est utilisée dans presque toutes les industries auxquelles vous pourriez penser. Il est important de le voir comme un groupe d’industries diverses avec une myriade d’applications différentes.
Quelques exemples:
- – produits de consommation (lunettes, chaussures, design, meubles)
- – produits industriels (outils de fabrication, prototypes, pièces d’utilisation finale fonctionnelles)
- – produits dentaires
- – prothèses
- – maquettes architecturales & maquettes
- – reconstitution de fossiles
- – reproduction de fossiles anciens artefacts
- – reconstitution de preuves en pathologie médico–légale
- – accessoires de films
Prototypage rapide & Fabrication rapide
Les entreprises ont utilisé des imprimantes 3D dans leur processus de conception créer des prototypes depuis la fin des années soixante-dix. L’utilisation d’imprimantes 3D à ces fins est appelée prototypage rapide.
Pourquoi utiliser des imprimantes 3D pour le prototypage rapide ?
En bref : c’est rapide et relativement bon marché. De l’idée au modèle 3D en passant par la tenue d’un prototype entre vos mains, c’est une question de jours au lieu de semaines. Les itérations sont plus faciles et moins chères à réaliser et vous n’avez pas besoin de moules ou d’outils coûteux.
Outre le prototypage rapide, l’impression 3D est également utilisée pour la fabrication rapide. La fabrication rapide est une nouvelle méthode de fabrication dans laquelle les entreprises utilisent des imprimantes 3D pour la fabrication sur mesure de petites séries / petites séries.
Automobile
Les constructeurs automobiles utilisent l’impression 3D depuis longtemps. Les entreprises automobiles impriment des pièces de rechange, des outils, des gabarits et des accessoires, mais aussi des pièces d’utilisation finale. L’impression 3D a permis la fabrication à la demande, ce qui a entraîné une baisse des niveaux de stock et a raccourci les cycles de conception et de production.
Les passionnés de l’automobile du monde entier utilisent des pièces imprimées en 3D pour restaurer de vieilles voitures. Un tel exemple est lorsque des ingénieurs australiens ont imprimé des pièces pour redonner vie à un Delage Type-C. Ce faisant, ils ont dû imprimer des pièces hors production pendant des décennies.
Aviation
L’industrie aéronautique utilise l’impression 3D de différentes manières. L’exemple suivant marque une étape importante dans la fabrication de l’impression 3D: GE Aviation a imprimé en 3D 30 000 buses de carburant cobalt-chrome pour ses moteurs d’avion LEAP. Ils ont franchi cette étape en octobre 2018, et étant donné qu’ils en produisent 600 par semaine sur quarante imprimantes 3D, c’est probablement beaucoup plus élevé que cela maintenant.
Une vingtaine de pièces individuelles qui devaient auparavant être soudées ensemble ont été consolidées en un composant imprimé en 3D qui pèse 25% de moins et est cinq fois plus résistant. Le moteur LEAP est le moteur le plus vendu dans l’industrie aérospatiale en raison de son haut niveau d’efficacité et GE économise 3 millions de dollars par avion en imprimant en 3D les buses de carburant, de sorte que cette seule pièce imprimée en 3D génère des centaines de millions de dollars d’avantages financiers.
Les buses de carburant de GE ont également fait leur chemin dans le Boeing 787 Dreamliner, mais ce n’est pas la seule pièce imprimée en 3D du 787. Les raccords structurels de 33 centimètres de long qui maintiennent la cuisine arrière à la cellule sont imprimés en 3D par une société appelée Norsk Titanium. Norsk a choisi de se spécialiser dans le titane car il a un rapport résistance / poids très élevé et est plutôt coûteux, ce qui signifie que la réduction des déchets permise par l’impression 3D a un impact financier plus important que par rapport aux métaux moins chers où les coûts des déchets matériels sont plus faciles à absorber. Plutôt que de fritter de la poudre métallique avec un laser comme la plupart des imprimantes 3D métalliques, la Norsk Merke 4 utilise un arc plasma pour faire fondre un fil métallique dans un processus appelé Dépôt Plasma Rapide (une forme de Dépôt d’Énergie Dirigée) qui peut déposer jusqu’à 10 kg de titane par heure. Une pièce en titane de 2 kg nécessiterait généralement un bloc de titane de 30 kg pour l’usiner, générant 28 kg de déchets, mais l’impression 3D de la même pièce ne nécessite que 6 kg de fil de titane.
Construction
Est-il possible d’imprimer un bâtiment? – oui, ça l’est. Les maisons imprimées en 3D sont déjà disponibles dans le commerce. Certaines entreprises impriment des pièces préfabriquées et d’autres le font sur place.
La plupart des histoires d’impression de béton que nous examinons sur ce site Web se concentrent sur des systèmes d’impression de béton à grande échelle avec des buses assez grandes pour un débit important. Il est idéal pour poser des couches de béton de manière assez rapide et reproductible. Mais pour un travail concret vraiment complexe qui utilise pleinement les capacités de l’impression 3D, il faut quelque chose d’un peu plus agile et d’une touche plus fine.
Produits de consommation
Lorsque nous avons commencé à bloguer sur l’impression 3D en 2011, l’impression 3D n’était pas prête à être utilisée comme méthode de production pour de gros volumes. De nos jours, il existe de nombreux exemples de produits de consommation imprimés en 3D pour utilisation finale.
Chaussures
La gamme 4D d’Adidas a une semelle intermédiaire entièrement imprimée en 3D et est imprimée en gros volumes. Nous avons fait un article à l’époque, expliquant comment Adidas ne publiait initialement que 5 000 paires de chaussures au public, et avait pour objectif de vendre 100 000 paires de modèles infusés d’AM d’ici 2018.
Avec leurs dernières itérations de la chaussure, il semble qu’ils ont dépassé cet objectif, ou sont sur le point de le dépasser. Les chaussures sont disponibles partout dans le monde dans les magasins Adidas locaux et également dans divers points de vente en ligne tiers.
Lunettes
Le marché des lunettes imprimées en 3D devrait atteindre 3,4 milliards de dollars d’ici 2028. Une section qui augmente rapidement est celle des cadres d’utilisation finale. L’impression 3D est une méthode de production particulièrement adaptée aux montures de lunettes car les mesures d’un individu sont faciles à traiter dans le produit final.
Mais saviez-vous qu’il est également possible d’imprimer des lentilles en 3D ? Les lentilles en verre traditionnelles ne sont pas fines et légères au départ; elles sont découpées dans un bloc de matériau beaucoup plus grand appelé ébauche, dont environ 80% sont gaspillées. Si l’on considère combien de personnes portent des lunettes et à quelle fréquence elles ont besoin d’une nouvelle paire, 80% de ces chiffres représentent beaucoup de gaspillage. En plus de cela, les laboratoires doivent conserver d’énormes stocks d’ébauches pour répondre aux besoins de vision personnalisés de leurs clients. Enfin, cependant, la technologie d’impression 3D a suffisamment avancé pour fournir des lentilles ophtalmiques personnalisées de haute qualité, éliminant ainsi les déchets et les coûts d’inventaire du passé. L’imprimante 3D Luxexcel VisionEngine utilise un monomère acrylate durcissable aux UV pour imprimer deux paires de lentilles par heure qui ne nécessitent aucun polissage ou post-traitement d’aucune sorte. Les zones focales peuvent également être entièrement personnalisées afin qu’une certaine zone de l’objectif puisse fournir une meilleure clarté à distance tandis qu’une zone différente de l’objectif offre une meilleure vision de près.
Bijoux
Il existe deux façons de produire des bijoux avec une imprimante 3D. Vous pouvez utiliser un processus de production direct ou indirect. Direct fait référence à la création d’un objet directement à partir de la conception 3D, tandis que la fabrication indirecte signifie que l’objet (motif) imprimé en 3D est finalement utilisé pour créer un moule pour le moulage de précision.
Soins de santé
Il n’est pas rare de nos jours de voir les gros titres sur les implants imprimés en 3D. Souvent, ces cas sont expérimentaux, ce qui peut donner l’impression que l’impression 3D est encore une technologie marginale dans les secteurs médical et de la santé, mais ce n’est plus le cas. Au cours de la dernière décennie, plus de 100 000 remplacements de hanche ont été imprimés en 3D par GE Additive.
La coupe Delta-TT conçue par le Dr. Guido Grappiolo et LimaCorporate est fabriqué en titane trabéculaire, caractérisé par une structure cellulaire hexagonale tridimensionnelle régulière qui imite la morphologie osseuse trabéculaire. La structure trabéculaire augmente la biocompatibilité du titane en favorisant la croissance osseuse dans l’implant. Certains des premiers implants Delta-TT fonctionnent toujours bien plus d’une décennie plus tard.
Un autre composant de soins de santé imprimé en 3D qui permet d’être indétectable est l’aide auditive. Presque toutes les aides auditives des 17 dernières années ont été imprimées en 3D grâce à une collaboration entre Materialise et Phonak. Phonak a développé Rapid Shell Modeling (RSM) en 2001. Avant RSM, la fabrication d’une aide auditive nécessitait neuf étapes laborieuses impliquant la sculpture à la main et la fabrication de moules, et les résultats étaient souvent mal adaptés. Avec RSM, un technicien utilise du silicone pour prendre une impression du conduit auditif, cette impression est numérisée en 3D, et après quelques ajustements mineurs, le modèle est imprimé en 3D avec une imprimante 3D en résine. L’électronique est ajoutée et ensuite elle est expédiée à l’utilisateur. Grâce à ce procédé, des centaines de milliers d’appareils auditifs sont imprimés en 3D chaque année.
Dentaire
Dans l’industrie dentaire, les moules pour aligneurs transparents sont peut-être les objets les plus imprimés en 3D au monde. Actuellement, les moules sont imprimés en 3D avec des procédés d’impression 3D à base de résine et de poudre, mais également via un jet de matériau. Les couronnes et les prothèses dentaires sont déjà directement imprimées en 3D, ainsi que des guides chirurgicaux.
Bio-impression
Au début des deux milliers de technologies d’impression 3D ont été étudiées par des entreprises de biotechnologie et des universités pour une utilisation possible dans des applications d’ingénierie tissulaire où des organes et des parties du corps sont construits à l’aide de techniques à jet d’encre. Des couches de cellules vivantes sont déposées sur un milieu de gel et lentement construites pour former des structures tridimensionnelles. Nous nous référons à ce domaine de recherche par le terme: bio-impression.
Aliments
La fabrication additive a envahi l’industrie alimentaire il y a longtemps. Des restaurants comme Food Ink et Melisse l’utilisent comme un argument de vente unique pour attirer des clients du monde entier.
Éducation
Les enseignants et les étudiants utilisent depuis longtemps des imprimantes 3D en classe. L’impression 3D permet aux étudiants de matérialiser leurs idées de manière rapide et abordable.
Bien que les diplômes spécifiques à la fabrication additive soient assez nouveaux, les universités utilisent depuis longtemps des imprimantes 3D dans d’autres disciplines. Il existe de nombreux cours pédagogiques que l’on peut suivre pour s’engager dans l’impression 3D. Les universités offrent des cours sur des éléments adjacents à l’impression 3D, tels que la CAO et la conception 3D, qui peuvent être appliqués à l’impression 3D à un certain stade.
En termes de prototypage, de nombreux programmes universitaires se tournent vers les imprimantes. Il existe des spécialisations en fabrication additive que l’on peut atteindre grâce à des diplômes en architecture ou en design industriel. Les prototypes imprimés sont également très courants dans les arts, l’animation et les études de mode.
Types de technologies et de procédés d’impression 3D
L’American Society for Testing and Materials (ASTM), a développé un ensemble de normes qui classent les procédés de fabrication additive en 7 catégories. Ce sont:
- Photopolymérisation en cuve
- Stéréolithographie (SLA)
- Traitement Numérique de la Lumière (DLP)
- Production d’Interface Liquide Continue (CLIP)
- Jet de matériau
- Jet de Liant
- Extrusion de matériau
- Modélisation par Dépôt fondu (FDM)
- Fabrication de Filaments fondus (FFF)
- Fusion en Lit de Poudre
- Fusion Multi-Jets (MJF)
- Frittage Laser Sélectif (SLS)
- Frittage Laser Direct des Métaux (DMLS)
- Stratification de feuille
- Dépôt d’Énergie Dirigée
Photopolymérisation en cuve
Une imprimante 3D basée sur le procédé de photopolymérisation en cuve présente un récipient rempli de résine photopolymère. La résine est durcie avec une source de lumière UV.
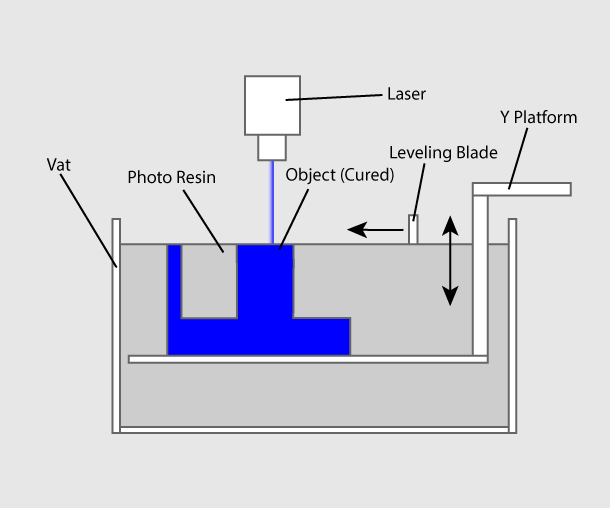
Stéréolithographie (SLA)
Le SLA a été inventé en 1986 par Charles Hull, qui a également fondé la société 3D Systems. La stéréolithographie utilise une cuve de résine photopolymère durcissable liquide et un laser ultraviolet pour construire les couches de l’objet une à la fois. Pour chaque couche, le faisceau laser trace une section transversale du motif de la pièce à la surface de la résine liquide. L’exposition à la lumière laser ultraviolette durcit et solidifie le motif tracé sur la résine et le fusionne à la couche ci-dessous.
Une fois le motif tracé, la plate-forme élévatrice du SLA descend d’une distance égale à l’épaisseur d’une seule couche, typiquement de 0,05 mm à 0,15 mm (0,002″à 0,006″). Ensuite, une lame remplie de résine balaie la section transversale de la pièce, la recouvrant de matériau frais. Sur cette nouvelle surface liquide, le motif de la couche suivante est tracé, rejoignant la couche précédente. Selon l’orientation d’impression de l’objet &, le SLA nécessite souvent l’utilisation de structures de support.
Traitement de la Lumière numérique (DLP)
Le traitement de la lumière numérique ou Traitement de la lumière numérique fait référence à une méthode d’impression utilisant des polymères légers et photosensibles. Bien qu’il soit très similaire au SLA, la principale différence réside dans la source de lumière. DLP utilise d’autres sources lumineuses comme les lampes à arc. La DLP est relativement rapide par rapport aux autres technologies d’impression 3D.
Production d’Interface Liquide Continue (CLIP)
L’un des processus les plus rapides utilisant la photopolymérisation en Cuve est appelé CLIP, abréviation de Production d’Interface Liquide Continue, développé par Carbon.
Synthèse de lumière numérique
Le cœur du processus CLIP est la technologie de synthèse de lumière numérique. Dans cette technologie, la lumière d’un moteur d’éclairage LED haute performance personnalisé projette une séquence d’images UV exposant une section transversale de la pièce imprimée en 3D, provoquant un durcissement partiel de la résine durcissable aux UV de manière contrôlée avec précision. L’oxygène traverse la fenêtre perméable à l’oxygène créant une interface liquide mince de résine non durcie entre la fenêtre et la partie imprimée connue sous le nom de zone morte. La zone morte est aussi mince que dix microns. A l’intérieur de la zone morte, l’oxygène interdit à la lumière de durcir la résine située au plus près de la fenêtre permettant ainsi l’écoulement continu du liquide sous la partie imprimée. Juste au-dessus de la zone morte, la lumière UV projetée vers le haut provoque une cascade de durcissement de la pièce.
La simple impression avec le matériel Carbon seul ne permet pas des propriétés d’utilisation finale avec des applications réelles. Une fois que la lumière a façonné la pièce, un deuxième processus de durcissement programmable atteint les propriétés mécaniques souhaitées en faisant cuire la pièce imprimée en 3d dans un bain thermique ou un four. Le durcissement thermique programmé définit les propriétés mécaniques en déclenchant une réaction chimique secondaire entraînant le renforcement du matériau pour obtenir les propriétés finales souhaitées.
Les composants imprimés avec la technologie Carbon sont à égalité avec les pièces moulées par injection. La synthèse de lumière numérique produit des propriétés mécaniques cohérentes et prévisibles, créant des pièces vraiment isotropes.
Jet de matériau
Dans ce processus, le matériau est appliqué en gouttelettes à travers une buse de petit diamètre, de la même manière qu’une imprimante à papier jet d’encre courante, mais il est appliqué couche par couche sur une plate-forme de construction, puis durci par la lumière UV.
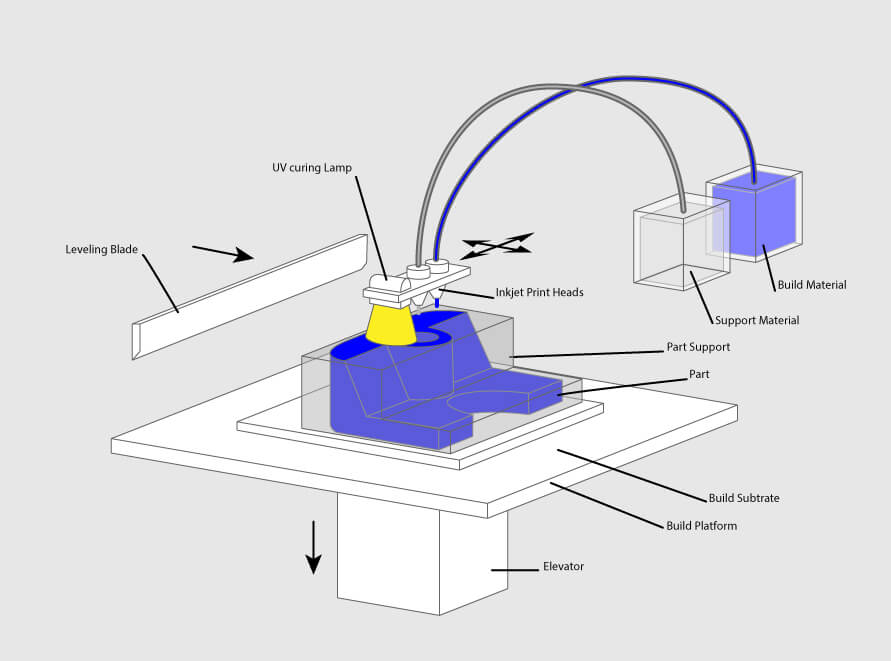
Jet de liant
Avec jet de liant, deux matériaux sont utilisés: un matériau de base en poudre et un liant liquide. Dans la chambre de construction, la poudre est étalée en couches égales et le liant est appliqué à travers des buses à jet qui « collent » les particules de poudre dans la forme requise. Une fois l’impression terminée, la poudre restante est nettoyée et peut souvent être réutilisée pour imprimer l’objet suivant. Cette technologie a été développée pour la première fois au Massachusetts Institute of Technology en 1993.
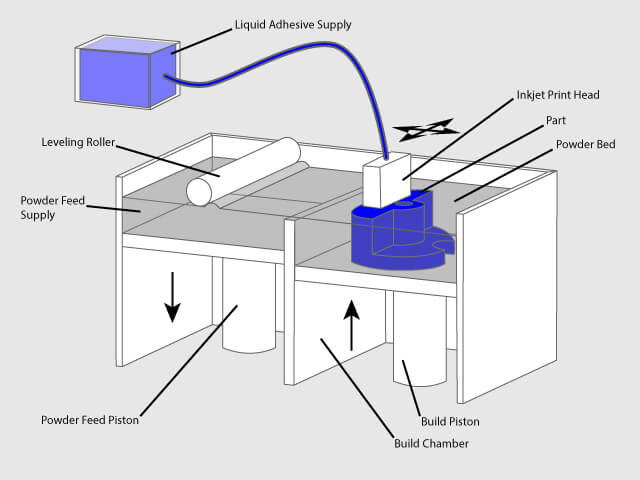
Extrusion de matériau
Modélisation par Dépôt fondu (FDM)
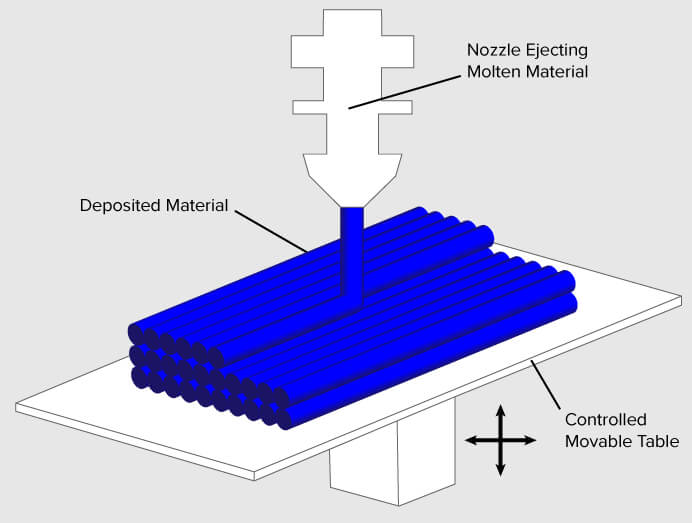
FDM fonctionne à l’aide d’un filament en plastique qui est déroulé à partir d’une bobine et est fourni à une buse d’extrusion qui peut activer et désactiver le flux. La buse est chauffée pour faire fondre le matériau et peut être déplacée dans les directions horizontale et verticale par un mécanisme à commande numérique. L’objet est produit en extrudant du matériau fondu pour former des couches à mesure que le matériau durcit immédiatement après l’extrusion de la buse.
Le FDM a été inventé par Scott Crump à la fin des années 80. Après avoir breveté cette technologie, il a créé la société Stratasys en 1988. Le terme Modélisation par dépôt fondu et son abréviation FDM sont des marques déposées de Stratasys Inc.
Fabrication de filaments fondus (FFF)
Le terme exactement équivalent, Fabrication de filaments fondus (FFF), a été inventé par les membres du projet RepRap pour donner une expression qui serait légalement libre dans son utilisation.
Fusion en lit de poudre
Frittage laser sélectif (SLS)
SLS utilise un laser de haute puissance pour fusionner de petites particules de poudre en une masse ayant la forme tridimensionnelle souhaitée. Le laser fusionne sélectivement la poudre en balayant d’abord les sections (ou couches) à la surface d’un lit de poudre. Après le balayage de chaque section transversale, le lit de poudre est abaissé d’une épaisseur de couche. Ensuite, une nouvelle couche de matériau est appliquée sur le dessus et le processus est répété jusqu’à ce que l’objet soit terminé.
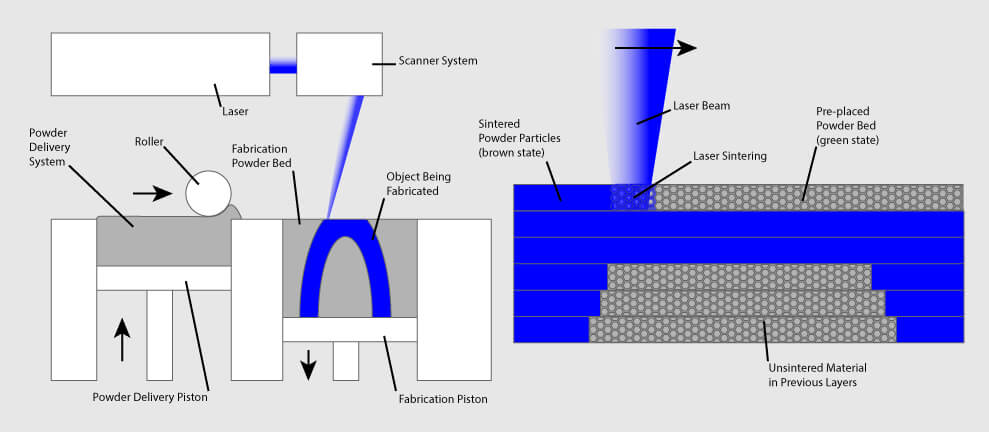
Multi Jet Fusion (MJF)
La technologie Multi Jet Fusion a été développée par Hewlett Packard et fonctionne avec un bras de balayage qui dépose une couche de poudre puis un autre bras équipé de jets d’encre qui applique sélectivement un agent liant sur le matériau. Les jets d’encre déposent également un agent de détail autour du liant pour assurer une dimensionnalité précise et des surfaces lisses. Enfin, la couche est exposée à une explosion d’énergie thermique qui fait réagir les agents.
Frittage laser direct des métaux (DMLS)
Le DMLS est fondamentalement le même que le SLS, mais utilise à la place de la poudre métallique. Toute la poudre inutilisée reste telle quelle et devient une structure de support pour l’objet. La poudre inutilisée peut être réutilisée pour la prochaine impression.
En raison de la puissance laser accrue, le DMLS a évolué vers un processus de fusion au laser. Pour en savoir plus à ce sujet et sur d’autres technologies métalliques, consultez notre page d’aperçu des technologies métalliques.
Stratification de feuilles
La stratification de feuilles implique un matériau en feuilles qui est lié ensemble par une force externe. Les feuilles peuvent être en métal, en papier ou sous forme de polymère. Les tôles sont soudées ensemble par soudage par ultrasons en couches, puis fraisées CNC dans une forme appropriée. Des feuilles de papier peuvent également être utilisées, mais elles sont collées par de la colle adhésive et découpées par des lames précises.
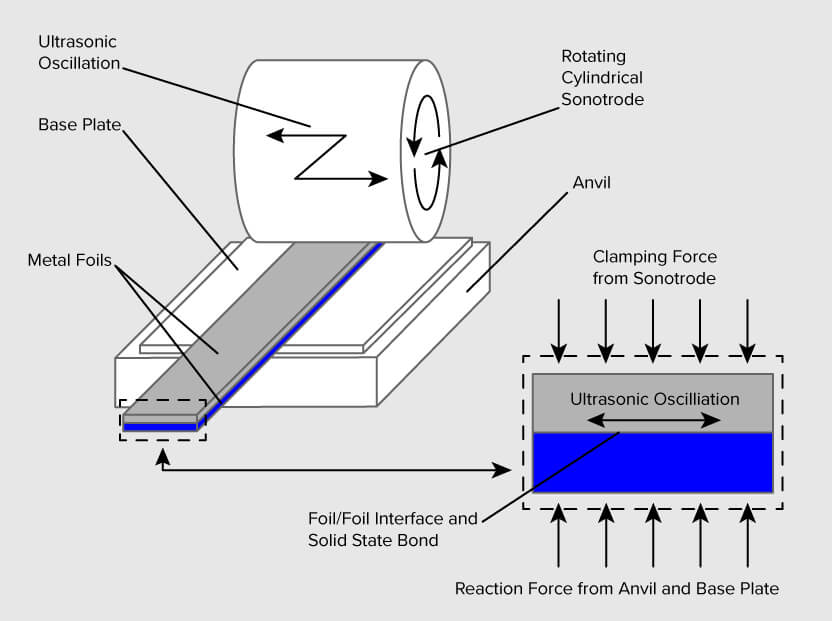
Dépôt d’énergie dirigée
Ce procédé est principalement utilisé dans l’industrie métallurgique et dans des applications de fabrication rapide. L’appareil d’impression 3D est généralement fixé à un bras robotique multi-axes et se compose d’une buse qui dépose de la poudre métallique ou du fil métallique sur une surface et d’une source d’énergie (laser, faisceau d’électrons ou arc de plasma) qui la fait fondre, formant un objet solide.
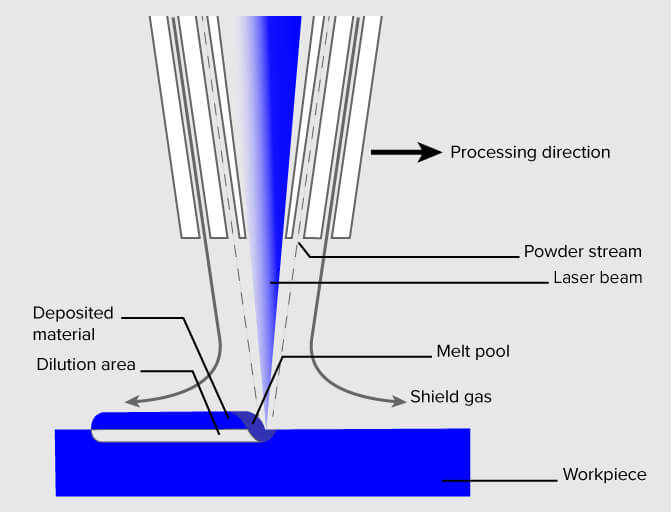
Matériaux
Plusieurs matériaux peuvent être utilisés en fabrication additive : plastiques, métaux, béton, céramique, papier et certains produits comestibles (par exemple le chocolat). Les matériaux sont souvent produits sous forme de fil d’alimentation, c’est-à-dire de filament, de poudre ou de résine liquide. En savoir plus sur nos matériaux en vedette sur notre page matériaux.
Services
Vous souhaitez implémenter l’impression 3D dans votre processus de production ? Obtenez un devis pour une pièce personnalisée ou commandez des échantillons sur notre page de service d’impression 3D.