a 3D nyomtatás vagy az additív gyártás háromdimenziós szilárd tárgyak digitális fájlból történő előállításának folyamata.
a 3D nyomtatott objektum létrehozása additív eljárásokkal történik. Egy additív folyamat során egy objektumot úgy hoznak létre, hogy az objektum létrehozásáig egymást követő anyagrétegeket helyeznek el. Ezen rétegek mindegyike a tárgy vékonyra szeletelt keresztmetszetének tekinthető.
a 3D nyomtatás a kivonó gyártás ellentéte, amely egy fém vagy műanyag darab kivágása / ürítése például marógéppel.
a 3D nyomtatás lehetővé teszi, hogy összetett alakzatokat készítsen kevesebb anyag felhasználásával, mint a hagyományos gyártási módszerek.
hírlevelünk ingyenes & bármikor leiratkozhat.
hogyan működik a 3D nyomtatás?
minden egy 3D-s modellel kezdődik. Dönthet úgy, hogy létrehoz egyet az alapoktól kezdve, vagy letöltheti egy 3D-s könyvtárból.
3D szoftver
számos különböző szoftver eszköz áll rendelkezésre. Az ipari minőségtől a nyílt forráskódig. Létrehoztunk egy áttekintést a 3D szoftver oldalunkon.
gyakran javasoljuk a kezdőknek, hogy kezdjék a Tinkercad-et. Tinkercad ingyenes, és működik a böngészőben, akkor nem kell telepíteni a számítógépre. A Tinkercad kezdő órákat kínál, és beépített funkcióval rendelkezik a modell nyomtatható fájlként történő exportálásához, pl.STL vagy .OBJ.
most, hogy van nyomtatható fájlja, a következő lépés az, hogy előkészítse azt a 3D nyomtatóhoz. Ezt szeletelésnek hívják.
szeletelés: A nyomtatható fájltól a 3D Nyomtatóig
a szeletelés alapvetően azt jelenti, hogy egy 3d modellt több száz vagy ezer rétegre vágunk, és szeletelő szoftverrel végezzük.
amikor a fájl szeletelve van, készen áll a 3D nyomtatóra. A fájl nyomtatóra történő betáplálása USB, SD vagy Wi-Fi segítségével történhet. A szeletelt fájl készen áll a 3D nyomtatásra rétegenként.
3D nyomdaipar
a 3D nyomtatás elfogadása elérte a kritikus tömeget, mivel azok, akik még nem integrálták az additív gyártást valahol az ellátási láncukban, most egy egyre zsugorodó kisebbséghez tartoznak. Ahol a 3D nyomtatás csak prototípuskészítésre és egyszeri gyártásra volt alkalmas a korai szakaszban, most gyorsan átalakul gyártási technológiává.
a 3D nyomtatás iránti jelenlegi kereslet nagy része ipari jellegű. Az Acumen Research and Consulting előrejelzése szerint a globális 3D nyomtatási piac eléri a 41 milliárd dollárt 2026-ra.
fejlődésével a 3D nyomtatási technológia szinte minden nagyobb iparágat átalakít, és megváltoztatja az életünket, a munkánkat és a játékunkat a jövőben.
példák a 3D nyomtatásra
a 3D nyomtatás a technológiák és anyagok számos formáját magában foglalja, mivel a 3D nyomtatást szinte minden iparágban használják. Fontos, hogy úgy tekintsünk rá, mint a különböző iparágak klaszterére, számtalan különböző alkalmazással.
néhány példa:
- – fogyasztási cikkek (szemüveg, lábbeli, design, bútor)
- – ipari termékek (gyártási eszközök, prototípusok, funkcionális végfelhasználói alkatrészek)
- -fogászati termékek
- – protézisek
- – építészeti méretarányos modellek & makettek
- – a fosszíliák rekonstrukciója
- – ősi leletek
- – rekonstruálása bizonyíték törvényszéki patológia
- – film kellékek
gyors prototípus & gyors gyártás
a vállalatok 3D nyomtatókat használtak tervezési folyamatuk során prototípusok létrehozása a hetvenes évek vége óta. A 3D nyomtatók ilyen célú használatát gyors prototípuskészítésnek nevezzük.
miért érdemes 3D nyomtatókat használni a gyors prototípuskészítéshez?
röviden: gyors és viszonylag olcsó. Az ötlettől a 3D-s modellig a prototípus kézben tartásáig hetek helyett napok kérdése. Az iterációk egyszerűbbek és olcsóbbak, és nincs szükség drága formákra vagy szerszámokra.
a gyors prototípuskészítés mellett a 3D nyomtatást is használják a gyors gyártáshoz. A Rapid manufacturing egy új gyártási módszer, ahol a vállalkozások 3D nyomtatókat használnak rövid távú / kis tételű egyedi gyártáshoz.
Automotive
az autógyártók már régóta használják a 3D nyomtatást. Az autóipari vállalatok pótalkatrészeket, szerszámokat, jigeket és szerelvényeket nyomtatnak, de végfelhasználói alkatrészeket is. A 3D nyomtatás lehetővé tette az igény szerinti gyártást, ami alacsonyabb készletszintet eredményezett, és lerövidítette a tervezési és gyártási ciklusokat.
az autóipari rajongók a világ minden tájáról 3D nyomtatott alkatrészeket használnak a régi autók helyreállításához. Az egyik ilyen példa az, amikor az Ausztrál mérnökök alkatrészeket nyomtattak, hogy életre keltsék a C típusú Delage-t. Ennek során olyan alkatrészeket kellett nyomtatniuk, amelyek évtizedek óta nem voltak gyártva.
repülés
a légiközlekedési ipar sokféle módon használja a 3D nyomtatást. A következő példa a 3D nyomtatás gyártásának jelentős mérföldkövét jelzi: a GE Aviation 3D nyomtatással 30 000 kobalt-króm üzemanyag-fúvókát nyomtatott LEAP Repülőgép-motorjaihoz. Ezt a mérföldkövet 2018 októberében érték el, és figyelembe véve, hogy hetente 600-at gyártanak negyven 3D nyomtatón, ez valószínűleg sokkal magasabb, mint most.
körülbelül húsz különálló alkatrészt, amelyeket korábban össze kellett hegeszteni, egyetlen 3D nyomtatott alkatrészbe konszolidáltak, amely 25% – kal kisebb súlyú és ötször erősebb. A LEAP engine a repülőgépipar legkelendőbb motorja magas hatékonysága miatt, és a GE repülőgépenként 3 millió dollárt takarít meg az üzemanyag-fúvókák 3D nyomtatásával, így ez az egyetlen 3D nyomtatott alkatrész több száz millió dolláros pénzügyi hasznot hoz.
a GE üzemanyagfúvókái szintén bejutottak a Boeing 787 Dreamlinerbe, de nem ez az egyetlen 3D nyomtatott alkatrész a 787-ben. A 33 centiméter hosszú szerkezeti szerelvényeket, amelyek a hátsó konyhai gályát a repülőgép vázához tartják, a Norsk Titanium nevű cég 3D-ben nyomtatja. A Norsk úgy döntött, hogy a Titánra szakosodik, mert nagyon nagy szilárdság-tömeg arány és meglehetősen drága, ami azt jelenti, hogy a 3D nyomtatás által lehetővé tett hulladékcsökkentés jelentősebb pénzügyi hatással bír, mint az olcsóbb fémekhez képest, ahol az anyaghulladék költségei könnyebben felszívódnak. Ahelyett, hogy a fémport lézerrel szinterezné, mint a legtöbb fém 3D nyomtató, A Norsk Merke 4 plazma ívet használ egy fémhuzal megolvasztására a gyors Plazma lerakódásnak (az irányított energia lerakódásának egyik formája) nevezett folyamatban, amely óránként akár 10 kg titánt is képes lerakni. Egy 2 kg-os titánrészhez általában 30 kg-os titánblokkra lenne szükség a megmunkáláshoz, 28 kg hulladékot generálva, de ugyanazon rész 3D nyomtatásához csak 6 kg titánhuzal szükséges.
Építés
lehet-e nyomtatni egy épületet? – igen, az. A 3D nyomtatott házak már kereskedelmi forgalomban kaphatók. Egyes vállalatok előregyártott alkatrészeket nyomtatnak, mások pedig a helyszínen.
a legtöbb konkrét nyomtatási történet, amelyet ezen a weboldalon nézünk, nagyméretű betonnyomtató rendszerekre összpontosít, meglehetősen nagy fúvókákkal, nagy áramlási sebesség mellett. Kiválóan alkalmas a betonrétegek meglehetősen gyors és megismételhető lefektetésére. De az igazán bonyolult konkrét munka, amely teljes mértékben kihasználja a képességeit 3D nyomtatás igényel valami egy kicsit fürge, finomabb tapintású.
fogyasztói termékek
amikor 2011-ben elkezdtünk blogolni a 3D nyomtatásról, a 3D nyomtatás nem volt kész arra, hogy nagy mennyiségű gyártási módszerként használják. Manapság számos példa van a végfelhasználás 3D nyomtatott fogyasztási cikkek.
lábbeli
az Adidas 4D termékcsaládja teljesen 3D nyomtatott középtalppal rendelkezik, és nagy mennyiségben nyomtatják. Akkor készítettünk egy cikket, amelyben elmagyaráztuk, hogy az Adidas kezdetben csak 5000 pár cipőt bocsátott ki a nyilvánosság számára, és 100 000 pár AM-infúziós mintát akart eladni 2018-ig.
a cipő legújabb iterációival úgy tűnik, hogy meghaladták ezt a célt, vagy úton vannak annak meghaladására. A cipők a világ minden tájáról elérhetők a helyi Adidas üzletekben, valamint a különböző 3rd party online üzletekben.
szemüveg
a 3D nyomtatott szemüvegek piaca várhatóan eléri a 3,4 milliárd dollárt 2028-ra. Gyorsan növekvő szakasz a végfelhasználói keretek. A 3D nyomtatás különösen alkalmas gyártási módszer a szemüvegkeretekhez, mivel az egyén méréseit könnyű feldolgozni a végtermékben.
de tudta, hogy 3D-s lencsék is nyomtathatók? A hagyományos üveglencsék nem vékonyak és könnyűek; egy sokkal nagyobb anyagtömbből vannak kivágva, amelyet vaknak neveznek, amelynek körülbelül 80% – a hulladékba kerül. Ha figyelembe vesszük, hogy hány ember visel szemüveget, és milyen gyakran van szüksége új párra, ezeknek a számoknak a 80% – a sok hulladék. Az egésznek a tetejébe, labs kell tartani hatalmas készletek üres, hogy megfeleljen az egyéni látás igényeinek ügyfeleik. Végül azonban a 3D nyomtatási technológia elég fejlett ahhoz, hogy kiváló minőségű, egyedi szemészeti lencséket biztosítson, megszüntetve a múlt hulladék-és készletköltségeit. A Luxexcel VisionEngine 3D nyomtató UV-gyógyítható akrilát monomert használ óránként két pár lencse nyomtatásához, amelyek semmilyen polírozást vagy utófeldolgozást nem igényelnek. A fókuszterületek teljesen testreszabhatók úgy is, hogy a lencse egy bizonyos területe távolról jobb tisztaságot biztosítson, míg a lencse másik területe jobb látást biztosít közelről.
ékszerek
kétféle módon lehet ékszereket gyártani 3D nyomtatóval. Használhat közvetlen vagy közvetett gyártási folyamatot. A közvetlen objektum létrehozására utal közvetlenül a 3D-s tervezésből, míg a közvetett gyártás azt jelenti, hogy a 3D-s nyomtatott objektumot (mintát) végül egy öntőforma létrehozására használják a befektetési öntéshez.
Healthcare
manapság nem ritka, hogy a 3D nyomtatott implantátumokkal kapcsolatos címsorokat látják. Gyakran ezek az esetek kísérleti jellegűek, ami azt a látszatot keltheti, hogy a 3D nyomtatás még mindig fringe technológia az orvosi és egészségügyi ágazatban, de ez már nem így van. Az elmúlt évtizedben több mint 100 000 csípőprotézist nyomtattak 3D-ben a GE Additive.
a Delta-TT Kupát Dr. A Guido Grappiolo és a LimaCorporate trabekuláris titánból készül, amelyet egy szabályos, háromdimenziós, hatszögletű sejtszerkezet jellemez, amely utánozza a trabekuláris csont morfológiáját. A trabekuláris szerkezet növeli a titán biokompatibilitását azáltal, hogy ösztönzi a csontok növekedését az implantátumba. Az első Delta-TT implantátumok egy része még mindig erős, több mint egy évtizeddel később.
egy másik 3D nyomtatott egészségügyi összetevő, amely jó munkát végez, hogy nem észlelhető, a hallókészülék. Az elmúlt 17 évben szinte minden hallókészülék 3D nyomtatásban készült a Materialise és a Phonak együttműködésének köszönhetően. A Phonak 2001-ben fejlesztette ki a gyors Héjmodellezést (RSM). Az RSM előtt egy hallókészülék elkészítése kilenc fáradságos lépést igényelt, beleértve a kézi szobrászatot és a penészkészítést, és az eredmények gyakran rosszul illeszkedtek. Az RSM segítségével a technikus szilikonnal készít benyomást a hallójáratról, ezt a benyomást 3D-ben szkennelik, majd néhány kisebb csípés után a modellt 3D-ben nyomtatják egy gyanta 3D nyomtatóval. Az elektronikát hozzáadják, majd eljuttatják a felhasználóhoz. Ezzel a folyamattal évente több százezer hallókészüléket nyomtatnak 3D-ben.
Fogászati
a fogászati iparban a tiszta alignerek öntőformáit látjuk, amelyek valószínűleg a legtöbb 3D nyomtatott tárgy a világon. Jelenleg a formákat 3D-ben nyomtatják mind gyanta, mind por alapú 3D nyomtatási eljárásokkal, de anyagsugarakkal is. A koronák és a fogsorok már közvetlenül 3D nyomtatásban vannak, sebészeti útmutatókkal együtt.
Bio-nyomtatás
a korai kétezer 3D nyomtatási technológiát tanulmányozták a biotechnológiai cégek és az egyetemek a szövetmérnöki alkalmazásokban való lehetséges felhasználásra, ahol a szerveket és testrészeket tintasugaras technikákkal építették. Az élő sejtek rétegei lerakódnak egy gél közegre, és lassan felépülnek, hogy háromdimenziós struktúrákat képezzenek. Erre a kutatási területre a következő kifejezéssel utalunk: bio-nyomtatás.
Élelmiszer
az adalékanyaggyártás régen megszállta az élelmiszeripart. Az olyan éttermek, mint a Food Ink és a Melisse ezt egyedülálló értékesítési pontként használják, hogy vonzzák az ügyfeleket a világ minden tájáról.
Oktatás
az oktatók és a diákok már régóta használnak 3D nyomtatókat az osztályteremben. A 3D nyomtatás lehetővé teszi a diákok számára, hogy ötleteiket gyors és megfizethető módon valósítsák meg.
míg az additív gyártás-specifikus fokozatok meglehetősen újak, az egyetemek már régóta használják a 3D nyomtatókat más tudományágakban. Vannak sok oktatási tanfolyamok lehet venni, hogy vegyenek részt a 3D-s nyomtatás. Az egyetemek tanfolyamokat kínálnak a 3D nyomtatással szomszédos dolgokról, mint például a CAD és a 3D tervezés, amelyek egy bizonyos szakaszban alkalmazhatók a 3D nyomtatásra.
ami a prototípus, sok egyetemi programok fordulnak nyomtatók. Vannak specializációk additív gyártás lehet elérni az építészet vagy ipari formatervezés fok. A nyomtatott prototípusok nagyon gyakoriak a művészetekben, az animációban és a divattanulmányokban is.
a 3D nyomtatási technológiák és folyamatok típusai
az American Society for Testing and Materials (ASTM) olyan szabványokat dolgozott ki, amelyek az additív gyártási folyamatokat 7 kategóriába sorolják. Ezek a következők:
- Vat fotopolimerizáció
- sztereolitográfia (SLA)
- digitális Fényfeldolgozás (DLP)
- folyamatos folyékony interfész gyártás (CLIP)
- anyag Jetting
- kötőanyag Jetting
- anyag extrudálás
- olvasztott lerakódás modellezés (FDM)
- olvasztott izzószál gyártás (FFF)
- por ágy Fusion
- Multi Jet Fusion (MJF)
- szelektív lézeres szinterezés (SLS)
- közvetlen fém lézeres szinterelés (DMLS)
- lemez laminálás
- irányított energia leválasztás
Vat fotopolimerizáció
a Vat Fotopolimerizációs módszeren alapuló 3D nyomtató fotopolimer gyantával töltött tartályt tartalmaz. A gyantát UV fényforrással keményítik.
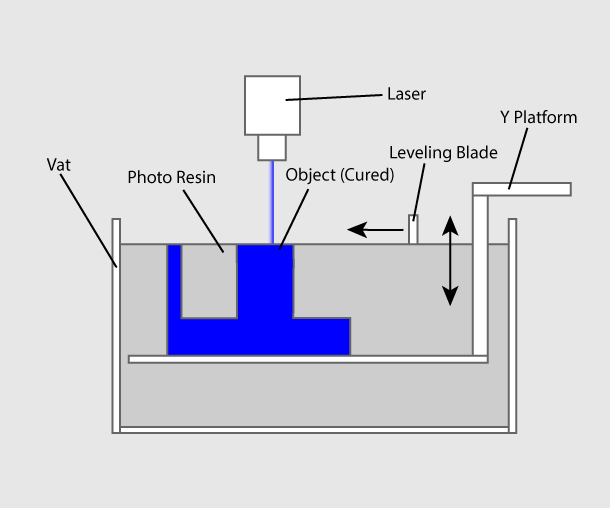
sztereolitográfia (SLA)
az SLA-t 1986-ban találta fel Charles Hull, aki akkoriban megalapította a 3D Systems céget. A sztereolitográfia folyékony, gyógyítható fotopolimer gyantát és ultraibolya lézert használ az objektum rétegeinek egyesével történő felépítéséhez. Minden réteg esetében a lézersugár az alkatrészmintázat keresztmetszetét követi a folyékony gyanta felületén. Az ultraibolya lézerfénynek való kitettség meggyógyítja és megszilárdítja a gyantán nyomon követett mintát, és összeolvasztja azt az alábbi réteggel.
a minta nyomon követése után az SLA felvonóplatformja egy réteg vastagságával megegyező távolsággal ereszkedik le, jellemzően 0,05-0,15 mm (0,002″ – 0,006″). Ezután egy gyantával töltött penge végigsöpör az alkatrész keresztmetszetén, új anyaggal bevonva. Ezen az új folyadékfelületen a következő rétegmintázat nyomon követhető, összekapcsolva az előző réteget. A & nyomtatási tájolástól függően az SLA gyakran támogató struktúrák használatát igényli.
Digital Light Processing (DLP)
a DLP vagy Digital Light Processing olyan nyomtatási módszer, amely fény-és fényérzékeny polimereket használ. Bár nagyon hasonlít az SLA-hoz, a legfontosabb különbség a fényforrás. A DLP más fényforrásokat, például ívlámpákat használ. A DLP viszonylag gyors a többi 3D nyomtatási technológiához képest.
folyamatos folyékony interfész termelés (CLIP)
az egyik leggyorsabb folyamat, amely a Vat Fotopolimerizációt használja, a CLIP, a folyamatos folyékony interfész gyártásának rövidítése, amelyet a Carbon fejlesztett ki.
digitális Fényszintézis
a klip folyamat szíve a digitális Fényszintézis technológia. Ebben a technológiában az egyedi, nagy teljesítményű LED-es fénymotorból származó fény UV-képek sorozatát vetíti ki, amelyek a 3D nyomtatott rész keresztmetszetét teszik ki, ami az UV-gyógyítható gyantát pontosan ellenőrzött módon részben kikeményíti. Az oxigén áthalad az oxigénáteresztő ablakon, létrehozva a nem keményített gyanta vékony folyékony interfészét az ablak és a holt zóna néven ismert nyomtatott rész között. A holt zóna olyan vékony, mint tíz mikron. A holt zónában az oxigén megakadályozza, hogy a fény az ablakhoz legközelebb eső gyantát kikeményítse, így lehetővé teszi a folyadék folyamatos áramlását a nyomtatott rész alatt. Közvetlenül a holt zóna felett az UV vetített fény felfelé kaszkádot okoz, mint az alkatrész kikeményedése.
egyszerűen a Carbon hardverével történő nyomtatás önmagában nem teszi lehetővé a végfelhasználási tulajdonságokat valós alkalmazásokkal. Miután a fény megformálta az alkatrészt, egy második programozható kikeményedési folyamat a kívánt mechanikai tulajdonságokat úgy éri el, hogy a 3D nyomtatott alkatrészt termálfürdőben vagy kemencében sütjük. A programozott hőkezelés beállítja a mechanikai tulajdonságokat egy másodlagos kémiai reakció kiváltásával, amely az anyagot erősíti a kívánt végső tulajdonságok elérése érdekében.
a Carbon technológiával nyomtatott alkatrészek egyenértékűek a fröccsöntött alkatrészekkel. A digitális Fényszintézis következetes és kiszámítható mechanikai tulajdonságokat hoz létre, amelyek valóban izotróp alkatrészeket hoznak létre.
anyagsugár
ebben a folyamatban az anyagot cseppekben viszik fel egy kis átmérőjű fúvókán keresztül, hasonlóan a közönséges tintasugaras papírnyomtató működéséhez, de rétegenként felviszik egy építési platformra, majd UV-fénnyel megkeményítik.
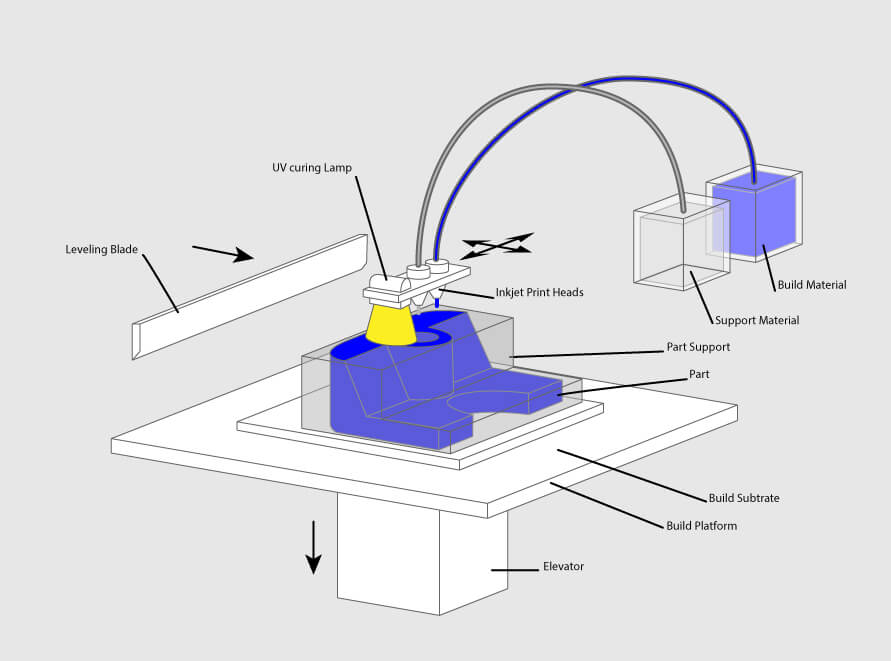
kötőanyag-befecskendezés
kötőanyag-befecskendezéssel két anyagot használnak: por alapanyagot és folyékony kötőanyagot. Az építőkamrában a port egyenlő rétegekben terítik el, a kötőanyagot pedig sugárfúvókákon keresztül viszik fel, amelyek a porrészecskéket a kívánt formába “ragasztják”. A nyomtatás befejezése után a maradék port megtisztítják, amely gyakran újra felhasználható a következő tárgy nyomtatására. Ezt a technológiát először a Massachusetts Institute of Technology-ban fejlesztették ki 1993-ban.
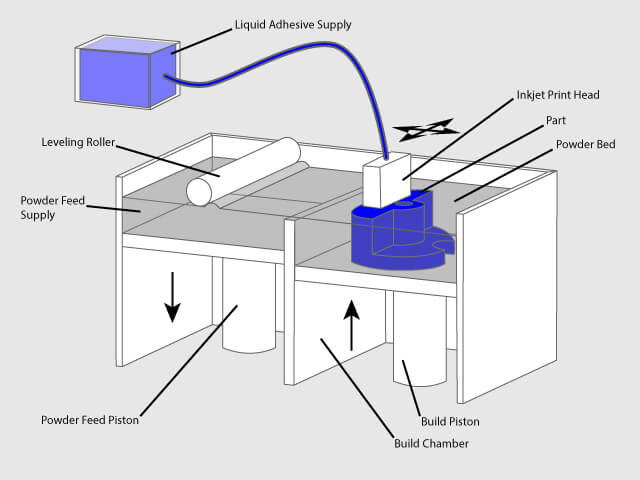
anyag extrudálás
olvasztott lerakódás modellezés (FDM)
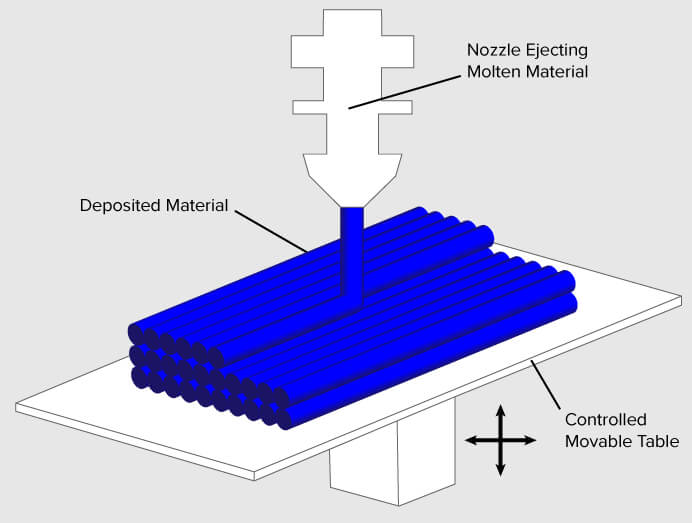
az FDM egy műanyag izzószállal működik, amelyet egy orsóról letekernek, és egy extrudáló fúvókához juttatnak, amely be-és kikapcsolhatja az áramlást. A fúvókát az anyag megolvasztására melegítik, és numerikusan vezérelt mechanizmussal mind vízszintes, mind függőleges irányban mozgatható. A tárgyat olvasztott anyag extrudálásával állítják elő, hogy rétegeket képezzenek, mivel az anyag közvetlenül a fúvókából történő extrudálás után megkeményedik.
az FDM-et Scott Crump találta fel a 80-as évek végén. A technológia szabadalmaztatása után 1988-ban megalapította a Stratasys céget. A Fused Deposition Modeling kifejezést és annak FDM rövidítését a Stratasys Inc.
olvasztott izzószál gyártása (FFF)
a pontosan egyenértékű kifejezést, olvasztott izzószál gyártása (FFF), a RepRap projekt tagjai alkották meg, hogy olyan kifejezést adjanak, amely használata jogilag nem korlátozott.
Porágyfúzió
szelektív lézeres szinterezés (SLS)
az SLS nagy teljesítményű lézert használ a por kis részecskéinek a kívánt háromdimenziós alakú tömegbe történő összeolvasztására. A lézer szelektíven biztosítja a port azáltal, hogy először letapogatja a keresztmetszeteket (vagy rétegeket) a porágy felületén. Minden keresztmetszet beolvasása után a porágyat egy rétegvastagsággal leengedjük. Ezután egy új anyagréteget viszünk fel a tetejére, és a folyamatot addig ismételjük, amíg az objektum befejeződik.
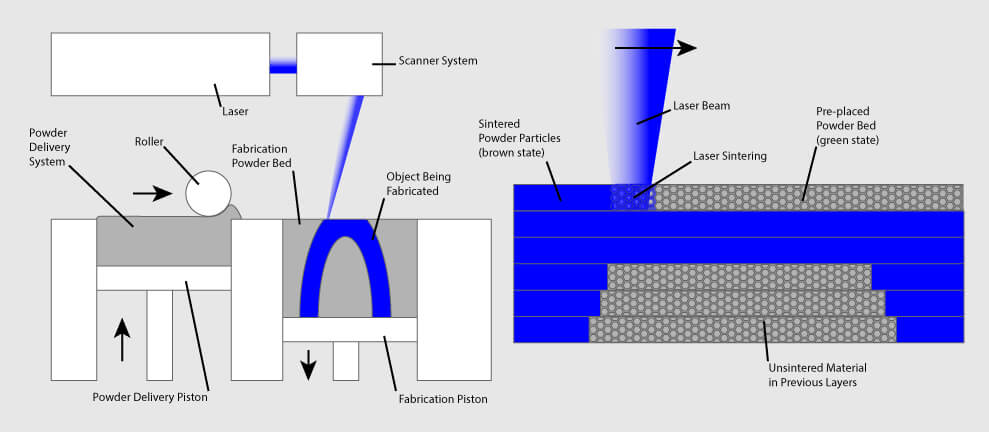
Multi Jet Fusion (MJF)
a Multi Jet Fusion technológiát a Hewlett Packard fejlesztette ki, és egy seprőkarral működik, amely lerakja a porréteget, majd egy másik karral, amely tintasugarakkal van felszerelve, amely szelektíven alkalmaz kötőanyagot az anyag felett. A tintasugaras nyomtatók egy részletező anyagot is elhelyeznek a kötőanyag körül, hogy biztosítsák a pontos méretezést és a sima felületeket. Végül a réteget hőenergia-robbanásnak tesszük ki, amely az ágensek reakcióját okozza.
közvetlen fém lézeres szinterezés (DMLS)
a DMLS alapvetően ugyanaz, mint az SLS, de fémport használ. Minden fel nem használt por úgy marad, ahogy van, és az objektum tartószerkezetévé válik. A fel nem használt por újra felhasználható a következő nyomtatáshoz.
a megnövekedett lézerteljesítmény miatt a DMLS lézeres olvasztási folyamattá fejlődött. Tudjon meg többet erről és más fémtechnológiákról a fémtechnológiák áttekintő oldalán.
lemez laminálás
lemez laminálás magában foglalja a lemezekben lévő anyagot, amely külső erővel van összekötve. A lapok lehetnek fém, papír vagy polimer formák. A fémlemezeket ultrahangos hegesztéssel hegesztik össze rétegekben, majd a CNC-t megfelelő formába őrlik. Papírlapok is használhatók, de ragasztóval ragasztják őket, és pontos pengékkel vágják.
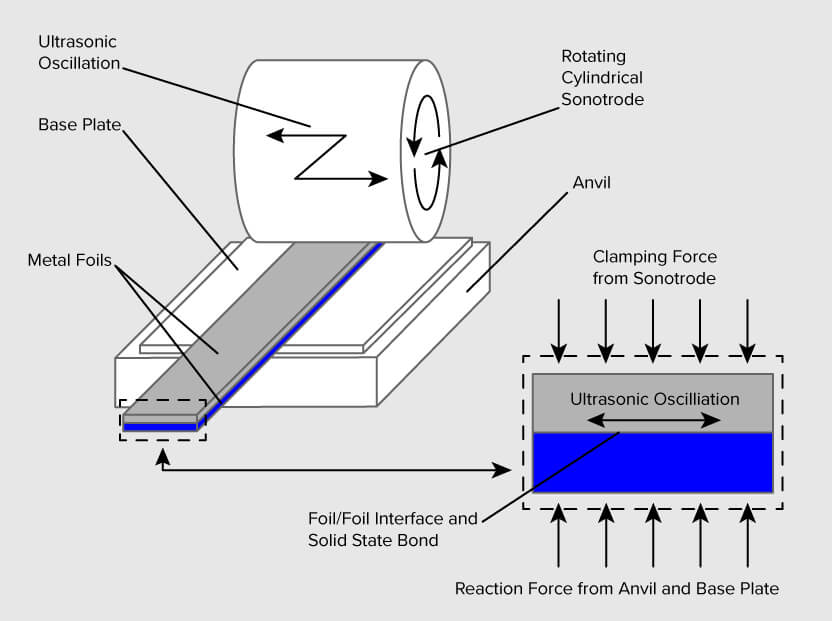
irányított energia leválasztás
ezt a folyamatot leginkább a fémiparban és a gyors gyártási alkalmazásokban használják. A 3D nyomtatóberendezést általában egy többtengelyes robotkarhoz rögzítik, és egy fúvókából áll, amely fémport vagy huzalt helyez el egy felületen, és egy energiaforrásból (lézer, elektronnyaláb vagy plazma ív), amely megolvasztja, szilárd tárgyat képezve.
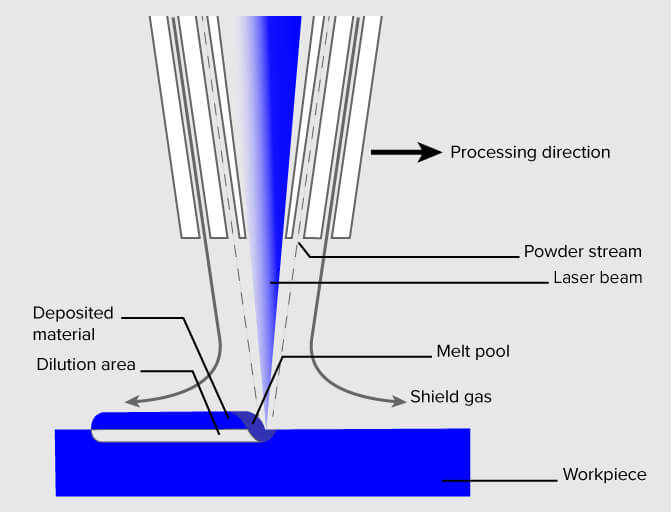
anyagok
az additív gyártásban többféle anyag használható: műanyagok, Fémek, beton, kerámia, papír és bizonyos ehető termékek (pl. csokoládé). Az anyagokat gyakran huzal alapanyagban, más néven izzószálban, por formában vagy folyékony gyantában állítják elő. Tudjon meg többet a kiemelt anyagokról az anyagok oldalon.
szolgáltatások
szeretné megvalósítani a 3D nyomtatást a gyártási folyamatban? Kérjen árajánlatot egy egyedi alkatrészhez vagy rendeljen mintákat a 3D nyomtatási szolgáltatás oldalunkon.