Interessato a mettere insieme un programma di manutenzione preventiva efficace?
Decisione intelligente.
Affidarsi a un approccio proattivo alla manutenzione ti aiuterà a evitare gli alti costi della manutenzione reattiva. A lungo termine, può aiutare a risparmiare decine a centinaia di migliaia di dollari ogni anno.
Avviare un programma di manutenzione preventiva non è difficile se si hanno le risorse giuste a portata di mano. Cominciamo con alcune informazioni preziose-Vi mostrerò come impostare il programma di manutenzione preventiva iniziale in pochi semplici passi.
Ma per iniziare a passare attraverso i dettagli di implementazione di manutenzione preventiva, facciamo in modo che siamo sulla stessa pagina circa il concetto di programma di manutenzione preventiva e la sua importanza.
Che cos’è un programma di manutenzione preventiva?
Il programma di manutenzione preventiva (chiamato anche programma di manutenzione preventiva) è un insieme di attività di manutenzione pianificate che si svolgono regolarmente su risorse critiche per evitare guasti alle apparecchiature.
Diverso dalla manutenzione reattiva, che si verifica quando le apparecchiature sono già guasti, PM adotta un approccio proattivo alla manutenzione degli asset per mantenere gli asset in condizioni di lavoro ottimali.
Un efficace piano di manutenzione preventiva aiuta le aziende a evitare i tempi di fermo, a risparmiare e a mantenere il posto di lavoro sicuro.
— Un recente studio di Jones Lang LaSalle evidenzia come una società di telecomunicazioni abbia visto un ritorno sull’investimento del 545% (ROI) quando implementava un piano di manutenzione preventiva.-
Con questo, andiamo oltre una guida passo-passo su come creare un programma di manutenzione preventiva.
Come creare un programma di manutenzione preventiva
Impostare un programma di manutenzione preventiva personalizzato potrebbe essere uno dei migliori investimenti a lungo termine che puoi fare nel tuo reparto supply chain. Oltre a tutti i soldi risparmiati sulla manutenzione correttiva, il tuo team di manutenzione dovrà affrontare meno momenti di crisi.
I passaggi per creare un programma PM sono descritti di seguito.
Ridurre la Manutenzione Reattiva con il 73,2%
Vedere i Risultati Red Hawk Gode Con Limble
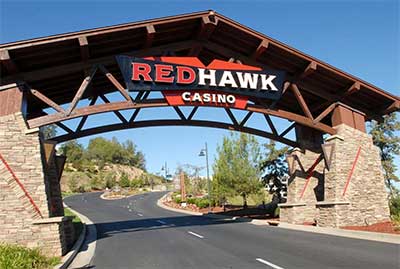
1: La priorità Attività da Esigenze di Manutenzione
mi consiglia di fare un elenco delle società più importanti attrezzature, e avviare il PM di pianificazione con loro – specialmente se questa è la prima volta che si stanno mettendo insieme una manutenzione proattiva di pianificazione.
Ciò consentirà a te e al tuo team di iniziare lentamente mentre passi a un flusso di lavoro e a una mentalità proattivi. Inoltre, se hai bisogno di lanciare l’idea ai più alti all’interno del tuo team, sarai in grado di dimostrare il valore più velocemente iniziando con poche risorse
In generale, le macchine che trarranno maggior beneficio da un programma di manutenzione preventiva sono quelle che:
1. Sono vitali per la funzione operativa e il successo dell’organizzazione
2. Avere modalità di guasto che possono essere prevenute con manutenzione ordinaria
3. Hanno alti costi di riparazione e sostituzione
4. Sono più probabilità di fallire col passare del tempo
Ciò significa che scegliendo pezzi di equipaggiamento che richiederebbero molte risorse – sia tempo che denaro-se falliscono inaspettatamente, fornirai alla tua azienda i maggiori ritorni a lungo termine. Tieni presente che investendo nella manutenzione preventiva, stai evitando i costi di manutenzione reattivi, che tendono ad essere molto più alti di una routine di manutenzione predittiva.
Un’altra cosa da tenere a mente quando si scelgono le risorse è che il rendimento sarà più alto se si scelgono macchine più recenti. La scelta di un pezzo di attrezzatura che raggiunge la fine del suo ciclo di vita non eviterà la necessità di sostituzione.
2: Raccogliere dati storici su ogni risorsa
Dopo aver avuto un’idea approssimativa di quali apparecchiature si desidera includere nel piano di manutenzione preventiva, è il momento di raccogliere dati su tutti gli ordini di lavoro e i tempi di inattività non pianificati che ogni risorsa ha attraversato negli ultimi anni.
Verificare quali tipi di problemi ogni risorsa presentato e con quale frequenza.
Questo ti darà qualche prospettiva su quanto dovresti spendere per lavori di manutenzione preventiva. È inoltre necessario prendere in considerazione l’età del bene e il tasso di ammortamento.
Se attualmente non si utilizza un CMMS, è probabile che questi dati storici siano registrati in un file CSV Excel o in un altro tipo di registro di manutenzione.
Nel caso in cui non si disponga di dati sostanziali sulla cronologia della manutenzione degli asset, il passo successivo può aiutare a raccogliere le informazioni necessarie per mettere insieme il piano di manutenzione preventiva.
3: Effettuare proiezioni sulle esigenze di manutenzione delle risorse
Ogni risorsa differisce notevolmente in termini di durata operativa e necessità di manutenzione – per questo motivo, è necessario raccogliere informazioni sulla particolarità di ciascuna apparecchiatura prima di mettere insieme la loro lista di controllo di manutenzione.
La principale fonte di informazioni sono le raccomandazioni del produttore di apparecchiature originali (OEM) del bene. Si tratta di un manuale fornito dal produttore che contiene i programmi per la manutenzione necessaria, l’utilizzo di pezzi di ricambio critici, e le istruzioni di lavoro di manutenzione di base.
I produttori di apparecchiature hanno un’enorme quantità di dati statistici provenienti da test interni e test sul campo eseguiti dai clienti, quindi è così che delineano l’OEM.
Un’altra fonte eccellente di informazioni preziose è il vostro team di manutenzione. Come responsabile della manutenzione, alcune informazioni possono essere ottenute solo parlando con tecnici di manutenzione, operatori di macchine e altri professionisti che gestiscono direttamente le macchine.
Mentre parli con loro, potresti scoprire che devi programmare una manutenzione regolare per uno dei tuoi beni perché uno dei tuoi tecnici non aveva il pezzo di ricambio necessario dopo un guasto recente e ha dovuto improvvisare una soluzione. La soluzione è evitare tempi di inattività non programmati, ma alcuni componenti sono attualmente sperimentando ulteriore usura.
4: Mettere insieme il piano di manutenzione preventiva iniziale
Dopo aver analizzato i dati storici, verificando le raccomandazioni dell’OEM e parlando con i tecnici sul campo, è il momento di organizzare le informazioni.
È necessario annotare tutte le attività di manutenzione preventiva per ciascuna risorsa insieme alla frequenza con cui è necessario eseguire ciascuna di tali attività su un particolare pezzo di equipaggiamento.
Dovresti finire con qualcosa di simile a questo per ciascuna delle tue risorse:
Come puoi vedere dall’immagine sopra, di solito non è una cattiva idea includere anche note aggiuntive per determinate attività in modo che un tecnico sappia esattamente cosa deve fare. Ecco un’altra risorsa per la frequenza delle ispezioni di manutenzione preventiva.
Una volta pronto questo piano iniziale di gestione patrimoniale, è possibile iniziare a mettere in pratica queste operazioni di manutenzione.
5: Verifica lo stato di avanzamento e adegualo secondo necessità
Man mano che il team di manutenzione si abitua a questo flusso di lavoro ottimizzato, monitorerai anche lo stato di avanzamento e le regolazioni.
Puoi aspettarti di fare aggiustamenti regolari in base ai risultati che ottieni. Questo ti aiuterà a mantenere un ritorno ottimale sull’investimento che stai facendo.
Una delle trappole comuni sta pianificando troppo lavoro preventivo e dando troppa attenzione alle risorse che non ne hanno bisogno. Se noti che è così, apporta le correzioni necessarie.
La buona notizia è che con un moderno software CMMS come Limble, si ha accesso a tutti i dati cruciali necessari per prendere queste decisioni. Hai solo bisogno di:
- Accedi al tuo CMMS
- Apri le carte asset per le risorse che sono sul tuo piano PM
- Apri report asset
Il report asset mostrerà grafici illuminanti e punti chiave per aiutarti a visualizzare i dati. Dovresti concentrarti su quanto lavoro preventivo è stato fatto sul bene. È inoltre necessario verificare se si è verificato un errore di asset da quando è stato avviato il piano PM.
Prendere decisioni da lì è abbastanza semplice.
Se la risorsa ha attraversato diversi lavori preventivi e non ha fallito una volta, significa che la lista di controllo della manutenzione preventiva funziona come dovrebbe. È anche possibile che ci sia più lavoro programmato per quella risorsa rispetto a ciò che è necessario. In tal caso, è possibile ridurre la lista di controllo PM senza comprometterne le condizioni operative.
Se la risorsa ha subito guasti, significa che probabilmente dovresti pianificare un lavoro PM più regolare. Ma prima di pianificare il lavoro preventivo extra, è una buona idea indagare su cosa ha causato i guasti. A volte, il problema è causato da una sola parte specifica che può essere facilmente risolta e non è necessario pianificare la manutenzione dell’intera risorsa.
Tieni presente che il tuo programma PM iniziale non sarà mai perfetto, e questo va perfettamente bene. Finché sei pronto a modificare il tuo piano di manutenzione preventiva in base alle informazioni che ottieni dal software di manutenzione e al feedback che ottieni dai tuoi tecnici, non hai nulla di cui preoccuparti.
6: Espandi il tuo programma di manutenzione preventiva
Con il programma di manutenzione preventiva iniziale, darai al tuo team la possibilità di familiarizzare con il nuovo approccio alla manutenzione e di capire come utilizzare il software di manutenzione preventiva per ottimizzare il programma PM.
Iniziare con solo poche risorse ti ha anche dato la possibilità di dimostrare l’impatto significativo sul flusso di lavoro di bottom line e operations della tua azienda.
Se avete bisogno di ottenere l’approvazione da parte dei superiori della società, o se si voleva testare i risultati di pianificazione di manutenzione preventiva da soli — a questo punto sarete stati in grado di farlo.
Se questo fosse davvero il caso, allora è il momento di ripetere questi passaggi ed espandere il programma PM in modo da poter vedere i vantaggi ancora più grandi dei programmi di manutenzione preventiva.
Sappiamo che inserire molti dati in un CMMS tutto in una volta non sembra una proposta divertente. Ecco perché abbiamo impostato Limble in un modo in cui puoi semplicemente preparare un file CSV Excel delle tue risorse, fare clic su Carica e lasciare Limble al resto del lavoro.
Come ottimizzare l’implementazione della manutenzione preventiva
A questo punto, hai una buona idea di come creare un programma di manutenzione preventiva. Ma come garantire che i membri del tuo team saranno in grado di implementarlo?
Bene, Limble CMMS si prende cura anche di quella parte.
Ecco come funziona:
Una volta che hai l’elenco delle attività di manutenzione preventiva necessarie per ogni risorsa, è il momento di assegnarle al tuo team di manutenzione e lasciare che la magia accada.
Ecco un esempio illustrativo di come apparirebbe se si stesse utilizzando CMM Limble:
Al fine di garantire un programma di manutenzione preventiva di successo, abbiamo progettato la piattaforma per offrire un’esperienza utente superba. Ciò significa offrire una dashboard che contenga tutto ciò di cui il tuo team avrà mai bisogno pur essendo facile da usare.
Il calendario PM offre al tuo team una panoramica in tempo reale dei lavori aperti e futuri. Automatizza la pianificazione PM e consente ai manager di modificare le date di scadenza con un semplice drag and drop.
I tecnici possono facilmente registrare il lavoro completato mentre si è sul campo utilizzando la soluzione software mobile. Ciò non solo consente di risparmiare tempo, ma riduce anche le possibilità di perdere alcune informazioni.
Pronto a creare un programma di manutenzione preventiva?
Investire nella manutenzione preventiva ha vantaggi inestimabili. Alcuni di essi includono:
- , prolungando la vita delle attrezzature critiche
- il miglioramento della vostra azienda di manutenzione del flusso di lavoro
- ridurre il numero di non pianificati i tempi di fermo macchina
- aumentando la sicurezza sul posto di lavoro
- diminuire il numero di costosa manutenzione reattiva
Avere un piano di manutenzione preventiva è un grande passo nella giusta direzione, ma non si dovrebbe lasciare che i tuoi sforzi sono stati sprecati. La supervisione e il controllo che ottieni con un CMMS ti assicureranno di spremere fino all’ultima goccia di valore dal tuo programma di manutenzione preventiva accuratamente predisposto. Per non parlare di come CMMS rende anche la vita molto più facile facendo il lavoro pesante di invio di notifiche, copiando orari PM, il monitoraggio della storia del lavoro, e molto altro ancora.
Pertanto, se si desidera semplificare il processo massimizzando i rendimenti, investire in un CMMS moderno, come Limble, è un gioco da ragazzi.