drukowanie 3D lub wytwarzanie addytywne to proces tworzenia trójwymiarowych obiektów stałych z pliku cyfrowego.
tworzenie drukowanego obiektu 3D odbywa się za pomocą procesów addytywnych. W procesie addytywnym obiekt jest tworzony przez układanie kolejnych warstw materiału do momentu utworzenia obiektu. Każda z tych warstw może być postrzegana jako cienko przecięty przekrój obiektu.
druk 3D jest przeciwieństwem produkcji subtraktywnej, która polega na wycinaniu / wydrążaniu kawałka metalu lub plastiku na przykład za pomocą frezarki.
druk 3D umożliwia tworzenie złożonych kształtów przy użyciu mniejszej ilości materiału niż tradycyjne metody produkcji.
nasz biuletyn jest bezpłatny & w każdej chwili możesz zrezygnować z subskrypcji.
jak działa Druk 3D?
wszystko zaczyna się od modelu 3D. Możesz utworzyć go od podstaw lub pobrać z biblioteki 3D.
Oprogramowanie 3D
dostępnych jest wiele różnych narzędzi programowych. Od klasy przemysłowej do open source. Stworzyliśmy przegląd na naszej stronie oprogramowania 3D.
często zalecamy początkującym rozpoczęcie od Tinkercad. Tinkercad jest darmowy i działa w Twojej przeglądarce, nie musisz go instalować na swoim komputerze. Tinkercad oferuje lekcje dla początkujących i ma wbudowaną funkcję eksportowania modelu jako pliku do wydruku np.STL lub .OBJ.
teraz, gdy masz plik do wydruku, następnym krokiem jest przygotowanie go do drukarki 3D. To się nazywa krojenie.
krojenie: Od Pliku do druku Do Drukarki 3D
krojenie zasadniczo oznacza krojenie modelu 3D na setki lub tysiące warstw i odbywa się za pomocą oprogramowania do krojenia.
gdy plik jest pocięty, jest gotowy do drukarki 3D. Podawanie pliku do drukarki może odbywać się przez USB, SD lub Wi-Fi. Pokrojony plik jest teraz gotowy do druku 3D warstwa po warstwie.
Przemysł druku 3D
przyjęcie druku 3D osiągnęło masę krytyczną, ponieważ ci, którzy jeszcze nie zintegrowali produkcji przyrostowej gdzieś w swoim łańcuchu dostaw, są obecnie częścią stale kurczącej się mniejszości. Tam, gdzie druk 3D był odpowiedni tylko do prototypowania i jednorazowej produkcji na wczesnym etapie, obecnie szybko przekształca się w technologię produkcji.
większość obecnego zapotrzebowania na druk 3D ma charakter przemysłowy. Acumen Research and Consulting prognozuje, że globalny rynek druku 3D osiągnie 41 miliardów dolarów do 2026 roku.
w miarę rozwoju technologia druku 3D ma przekształcić prawie każdą poważną branżę i zmienić sposób, w jaki żyjemy, pracujemy i bawimy się w przyszłości.
przykłady druku 3D
druk 3D obejmuje wiele form technologii i materiałów, ponieważ druk 3D jest używany w prawie wszystkich branżach, o których można pomyśleć. Ważne jest, aby postrzegać go jako klaster różnych branż z niezliczoną ilością różnych zastosowań.
kilka przykładów:
- – produkty konsumenckie (okulary, obuwie, wzornictwo, meble)
- – produkty przemysłowe (narzędzia produkcyjne, prototypy, funkcjonalne części końcowe)
- -produkty dentystyczne
- – protetyka
- – modele architektoniczne w skali & makiety
- – rekonstrukcja skamieniałości
- – replikacja starożytne artefakty
- – rekonstrukcja dowodów w patologii sądowej
- – rekwizyty filmowe
szybkie prototypowanie & szybka produkcja
firmy wykorzystały Drukarki 3D w procesie projektowania do tworzenia prototypów od końca lat siedemdziesiątych. Używanie drukarek 3D do tych celów nazywa się szybkim prototypowaniem.
po co używać drukarek 3D do szybkiego prototypowania?
krótko mówiąc: szybko i stosunkowo tanio. Od pomysłu, przez model 3D, po trzymanie prototypu w rękach to kwestia dni, a nie tygodni. Iteracje są łatwiejsze i tańsze do wykonania i nie potrzebujesz drogich form ani narzędzi.
oprócz szybkiego prototypowania, druk 3D jest również używany do szybkiej produkcji. Rapid manufacturing to nowa metoda produkcji, w której firmy używają drukarek 3D do produkcji niestandardowej w krótkich seriach / małych partiach.
Motoryzacja
producenci samochodów od dawna wykorzystują druk 3D. Firmy motoryzacyjne drukują części zamienne, narzędzia, przyrządy i osprzęt, ale także części końcowe. Drukowanie 3D umożliwiło produkcję na żądanie, co doprowadziło do obniżenia poziomu zapasów i skróciło cykle projektowania i produkcji.
entuzjaści motoryzacji na całym świecie używają drukowanych części 3D do przywracania starych samochodów. Jednym z takich przykładów jest, gdy Australijscy inżynierowie drukowali części, aby przywrócić do życia Delage Type-C. W ten sposób musieli drukować części, które nie były produkowane przez dziesięciolecia.
lotnictwo
przemysł lotniczy wykorzystuje druk 3D na wiele różnych sposobów. Poniższy przykład stanowi ważny kamień milowy w produkcji druku 3D: firma GE Aviation wydrukowała 3D 30 000 kobaltowo-chromowanych dysz paliwowych dla swoich silników lotniczych LEAP. Osiągnęli ten kamień milowy w październiku 2018 r., a biorąc pod uwagę, że produkują 600 tygodniowo na czterdziestu drukarkach 3D, jest to prawdopodobnie znacznie wyższe niż obecnie.
około dwudziestu pojedynczych części, które wcześniej musiały być ze sobą zespawane, połączono w jeden element drukowany 3D, który waży o 25% mniej i jest pięciokrotnie mocniejszy. Silnik LEAP jest najlepiej sprzedającym się silnikiem w przemyśle lotniczym ze względu na wysoki poziom wydajności, a GE oszczędza 3 miliony dolarów na samolot, drukując dysze paliwa 3D, więc ta pojedyncza drukowana część 3D generuje setki milionów dolarów korzyści finansowych.
dysze paliwa GE również trafiły do Boeinga 787 Dreamliner, ale nie jest to jedyna drukowana część 3D w modelu 787. 33-centymetrowe elementy konstrukcyjne, które przytrzymują kuchnię rufową do płatowca, są drukowane 3D przez firmę Norsk Titanium. Norsk zdecydował się na specjalizację w tytanie, ponieważ ma bardzo wysoki stosunek wytrzymałości do masy i jest dość drogi, co oznacza, że redukcja odpadów możliwa dzięki drukowaniu 3D ma bardziej znaczący wpływ finansowy niż w porównaniu z tańszymi metalami, gdzie koszty odpadów materiałowych są łatwiejsze do wchłonięcia. Zamiast spiekania proszku metalu za pomocą lasera, jak większość metalowych drukarek 3D, Norsk Merke 4 używa łuku plazmowego do stopienia drutu metalowego w procesie zwanym szybkim osadzaniem plazmowym (forma ukierunkowanego osadzania energii), który może osadzać do 10 kg tytanu na godzinę. Część tytanowa o wadze 2 kg wymagałaby Zwykle bloku tytanu o wadze 30 kg, aby go obrabiać, generując 28 kg odpadów, ale drukowanie 3D tej samej części wymaga tylko 6 kg drutu tytanowego.
Budownictwo
czy można wydrukować budynek? – tak. Domy z nadrukiem 3D są już dostępne na rynku. Niektóre firmy drukują prefabrykowane części, a inne robią to na miejscu.
większość historii drukowania betonu, które przeglądamy na tej stronie, koncentruje się na wielkoskalowych systemach drukowania betonu z dość dużymi dyszami dla dużego natężenia przepływu. Świetnie nadaje się do układania warstw betonu w dość szybki i powtarzalny sposób. Ale dla naprawdę skomplikowanych konkretnych prac, które w pełni wykorzystują możliwości druku 3D, wymaga czegoś nieco bardziej zwinnego i delikatniejszego.
produkty konsumenckie
kiedy w 2011 roku rozpoczęliśmy blogowanie na temat druku 3D, Druk 3D nie był gotowy do użycia jako metoda produkcji dużych ilości. Obecnie istnieje wiele przykładów produktów konsumenckich z nadrukiem 3D.
Obuwie
seria 4D firmy Adidas ma w pełni wydrukowaną podeszwę środkową 3D i jest drukowana w dużych ilościach. Przygotowaliśmy wtedy artykuł wyjaśniający, w jaki sposób Adidas początkowo wypuszczał na rynek tylko 5000 par butów, a jego celem było sprzedanie 100 000 par modeli z serii am do 2018 roku.
z ich najnowszymi iteracjami butów wydaje się, że przekroczyli ten cel, lub są na drodze do jego przekroczenia. Buty są dostępne na całym świecie w lokalnych sklepach Adidas, a także w różnych sklepach internetowych innych firm.
okulary
przewiduje się, że rynek okularów drukowanych 3D osiągnie 3,4 miliarda dolarów do 2028 roku. Szybko rosnąca sekcja dotyczy ramek końcowych. Druk 3D jest szczególnie odpowiednią metodą produkcji opraw okularów, ponieważ pomiary jednostki są łatwe do przetworzenia w produkcie końcowym.
ale czy wiesz, że możliwe jest również drukowanie soczewek 3D? Tradycyjne szklane soczewki nie zaczynają się od cienkich i lekkich; są wycięte ze znacznie większego bloku materiału zwanego pustym, z którego około 80% idzie na marne. Kiedy weźmiemy pod uwagę, ile osób nosi okulary i jak często muszą uzyskać nową parę, 80% tych liczb to dużo odpadów. Ponadto laboratoria muszą przechowywać ogromne zapasy półfabrykatów, aby spełnić niestandardowe potrzeby klientów. Wreszcie jednak technologia druku 3D jest wystarczająco zaawansowana, aby zapewnić wysokiej jakości niestandardowe soczewki okulistyczne, eliminując koszty odpadów i zapasów z przeszłości. Drukarka 3D Luxexcel VisionEngine wykorzystuje utwardzany UV monomer akrylowy do drukowania dwóch par soczewek na godzinę, które nie wymagają żadnego polerowania ani obróbki końcowej. Obszary ogniskowej można również całkowicie dostosować, aby określony obszar obiektywu zapewniał lepszą klarowność na odległość, podczas gdy inny obszar obiektywu zapewnia lepsze widzenie z bliska.
Biżuteria
istnieją dwa sposoby produkcji biżuterii za pomocą drukarki 3D. Możesz użyć bezpośredniego lub pośredniego procesu produkcyjnego. Bezpośrednie odnosi się do tworzenia obiektu prosto z projektu 3D, podczas gdy produkcja pośrednia oznacza, że obiekt (wzór), który jest drukowany 3D ostatecznie jest używany do tworzenia formy do odlewania inwestycyjnego.
Opieka zdrowotna
nierzadko w dzisiejszych czasach pojawiają się nagłówki na temat implantów drukowanych w 3D. Często te przypadki są eksperymentalne, co może wydawać się, że druk 3D nadal jest technologią marginesową w sektorze medycznym i opieki zdrowotnej, ale już tak nie jest. W ciągu ostatniej dekady firma GE Additive wydrukowała 3D ponad 100 000 uzupełnień stawu biodrowego.
Puchar Delta-TT zaprojektowany przez Dr. Guido Grappiolo i LimaCorporate jest wykonany z tytanu Beleczkowatego, który charakteryzuje się regularną, trójwymiarową, sześciokątną strukturą komórkową, która imituje morfologię kości beleczkowatej. Struktura beleczkowata zwiększa biokompatybilność tytanu poprzez stymulowanie wzrostu kości do implantu. Niektóre z pierwszych implantów Delta – TT są nadal silne ponad dekadę później.
kolejnym elementem drukowanym w technologii 3D, który dobrze sprawdza się jako niewykrywalny, jest aparat słuchowy. Prawie każdy aparat słuchowy w ciągu ostatnich 17 lat został wydrukowany w 3D dzięki współpracy między Materialise i Phonak. Firma Phonak opracowała Rapid Shell Modeling (RSM) w 2001 roku. Przed RSM wykonanie jednego aparatu słuchowego wymagało dziewięciu pracochłonnych kroków związanych z rzeźbieniem ręcznym i formowaniem, a wyniki były często źle dopasowane. W przypadku RSM technik używa silikonu do wykonania wrażenia kanału słuchowego, to wrażenie jest skanowane 3D, a po drobnych poprawkach model jest drukowany 3D za pomocą żywicznej Drukarki 3D. Elektronika jest dodawana, a następnie wysyłana do użytkownika. Dzięki temu procesowi każdego roku setki tysięcy aparatów słuchowych są drukowane 3D.
Dental
w branży dentystycznej widzimy, że formy do przezroczystych alignerów są prawdopodobnie najbardziej drukowanymi obiektami 3D na świecie. Obecnie formy są drukowane 3D zarówno za pomocą procesów drukowania 3D na bazie żywicy, jak i proszku, ale także za pomocą strumieniowania materiału. Korony i protezy są już bezpośrednio drukowane w 3D wraz z przewodnikami chirurgicznymi.
bio-printing
od początku dwóch tysięcy technologia druku 3D była badana przez firmy biotechnologiczne i środowiska akademickie pod kątem możliwego zastosowania w zastosowaniach inżynierii tkankowej, w których organy i części ciała są budowane przy użyciu technik atramentowych. Warstwy żywych komórek są osadzane na podłożu żelowym i powoli budowane, tworząc trójwymiarowe struktury. Tę dziedzinę badań określamy terminem: bio-druk.
żywność
produkcja addytywna już dawno opanowała przemysł spożywczy. Restauracje takie jak Food Ink i Melisse wykorzystują to jako unikalny punkt sprzedaży, aby przyciągnąć klientów z całego świata.
Edukacja
nauczyciele i uczniowie od dawna używają drukarek 3D w klasie. Drukowanie 3D umożliwia uczniom zmaterializowanie swoich pomysłów w szybki i niedrogi sposób.
chociaż stopnie specyficzne dla wytwarzania przyrostowego są dość nowe, uniwersytety od dawna używają drukarek 3D w innych dyscyplinach. Istnieje wiele kursów edukacyjnych, które można podjąć, aby zaangażować się w Drukowanie 3D. Uniwersytety oferują kursy na temat rzeczy sąsiadujących z drukiem 3D, takich jak projektowanie CAD i 3D, które mogą być stosowane do drukowania 3D na pewnym etapie.
jeśli chodzi o prototypowanie, wiele programów uniwersyteckich zwraca się do drukarek. Istnieją specjalizacje w produkcji addytywnej, które można osiągnąć poprzez stopnie architektury lub Wzornictwa Przemysłowego. Drukowane prototypy są również bardzo powszechne w sztuce, animacji i badaniach mody.
rodzaje technologii i procesów druku 3D
Amerykańskie Towarzystwo Badań i materiałów (ASTM) opracowało zestaw norm, które klasyfikują procesy wytwarzania przyrostowego w 7 kategoriach. Są to:
- Fotopolimeryzacja Vat
- Stereolitografia (SLA)
- cyfrowe przetwarzanie światła (DLP)
- ciągła produkcja płynnego interfejsu (CLIP)
- Materiał Jetting
- spoiwo JETTING
- wytłaczanie materiału
- topione Modelowanie osadzania (FDM)
- topione wytwarzanie włókien (FFF)
- fuzja złoża proszku
- Multi Jet Fusion (MJF)
- selektywne spiekanie laserowe (SLS)
- bezpośrednie spiekanie laserowe metalu (DMLS)
- laminowanie arkuszy
- ukierunkowane osadzanie energii
Fotopolimeryzacja w kadzi
Drukarka 3D oparta na metodzie fotopolimeryzacji w kadzi posiada pojemnik wypełniony żywicą fotopolimerową. Żywica utwardzana jest za pomocą Źródła światła UV.
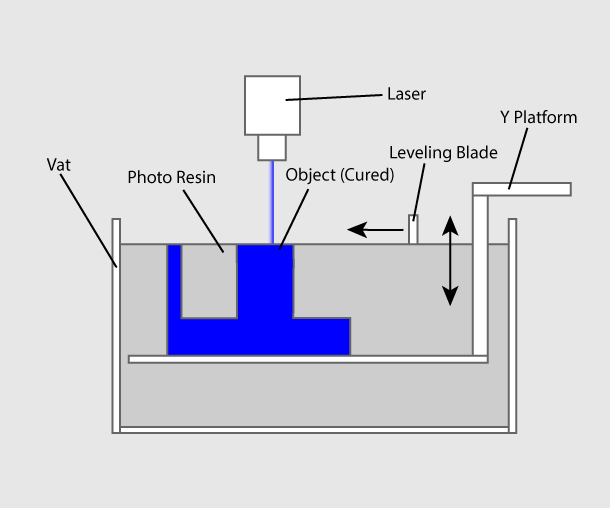
Stereolitografia (SLA)
SLA został wynaleziony w 1986 roku przez Charlesa Hulla, który również w tym czasie założył firmę 3D Systems. Stereolitografia używa kadzi z ciekłej utwardzalnej żywicy fotopolimerowej i lasera ultrafioletowego do budowy warstw obiektu pojedynczo. Dla każdej warstwy wiązka laserowa śledzi przekrój wzoru części na powierzchni ciekłej żywicy. Ekspozycja na światło lasera ultrafioletowego utwardza i zestala wzór na żywicy i łączy go z warstwą poniżej.
po prześledzeniu wzoru platforma windy SLA schodzi o odległość równą grubości pojedynczej warstwy, zwykle od 0,05 mm do 0,15 mm (0,002″ do 0,006″). Następnie wypełnione żywicą ostrze przemieszcza się po przekroju części, ponownie pokrywając ją świeżym materiałem. Na tej nowej powierzchni cieczy śledzony jest kolejny wzór warstwy, łącząc poprzednią warstwę. W zależności od orientacji wydruku obiektu &, SLA często wymaga użycia struktur podporowych.
cyfrowe przetwarzanie światła (DLP)
DLP lub cyfrowe przetwarzanie światła odnosi się do metody drukowania, która wykorzystuje lekkie i światłoczułe polimery. Chociaż jest bardzo podobny do SLA, kluczową różnicą jest źródło światła. DLP wykorzystuje inne źródła światła, takie jak lampy łukowe. DLP jest stosunkowo szybki w porównaniu do innych technologii druku 3D.
Continuous Liquid Interface Production (CLIP)
jednym z najszybszych procesów wykorzystujących Fotopolimeryzację Vat jest CLIP, skrót od Continuous Liquid Interface Production, opracowany przez Carbon.
Cyfrowa synteza światła
sercem procesu klipu jest technologia cyfrowej syntezy światła. W tej technologii światło z niestandardowego wysokowydajnego silnika świetlnego LED wyświetla sekwencję obrazów UV, odsłaniając przekrój drukowanej części 3D, powodując częściowe utwardzanie żywicy utwardzalnej UV w precyzyjnie kontrolowany sposób. Tlen przechodzi przez okno przepuszczalne dla tlenu, tworząc cienki płynny interfejs nieutwardzonej żywicy między oknem a drukowaną częścią znaną jako martwa strefa. Martwa strefa jest tak cienka jak dziesięć mikronów. Wewnątrz strefy martwej tlen uniemożliwia utwardzanie przez światło żywicy znajdującej się najbliżej okna, umożliwiając tym samym ciągły przepływ cieczy pod drukowaną częścią. Tuż nad Martwą strefą promieniowanie UV rzutowane w górę powoduje kaskadę, taką jak utwardzanie części.
proste drukowanie przy użyciu samego sprzętu Carbon nie pozwala na uzyskanie właściwości końcowego zastosowania w rzeczywistych zastosowaniach. Gdy światło ukształtuje część, drugi programowalny proces utwardzania osiąga pożądane właściwości mechaniczne poprzez pieczenie wydrukowanej części 3d w kąpieli termicznej lub piekarniku. Zaprogramowane utwardzanie termiczne ustawia właściwości mechaniczne poprzez wywołanie wtórnej reakcji chemicznej, powodując, że materiał wzmacnia osiągnięcie pożądanych właściwości końcowych.
elementy drukowane w technologii Carbon są na równi z częściami formowanymi wtryskowo. Cyfrowa synteza światła wytwarza spójne i przewidywalne właściwości mechaniczne, tworząc części, które są prawdziwie izotropowe.
Materiał Jetting
w tym procesie materiał jest nakładany kropelkami przez dyszę o małej średnicy, podobną do sposobu, w jaki działa zwykła drukarka atramentowa, ale jest nakładany warstwa po warstwie na platformę konstrukcyjną, a następnie utwardzany światłem UV.
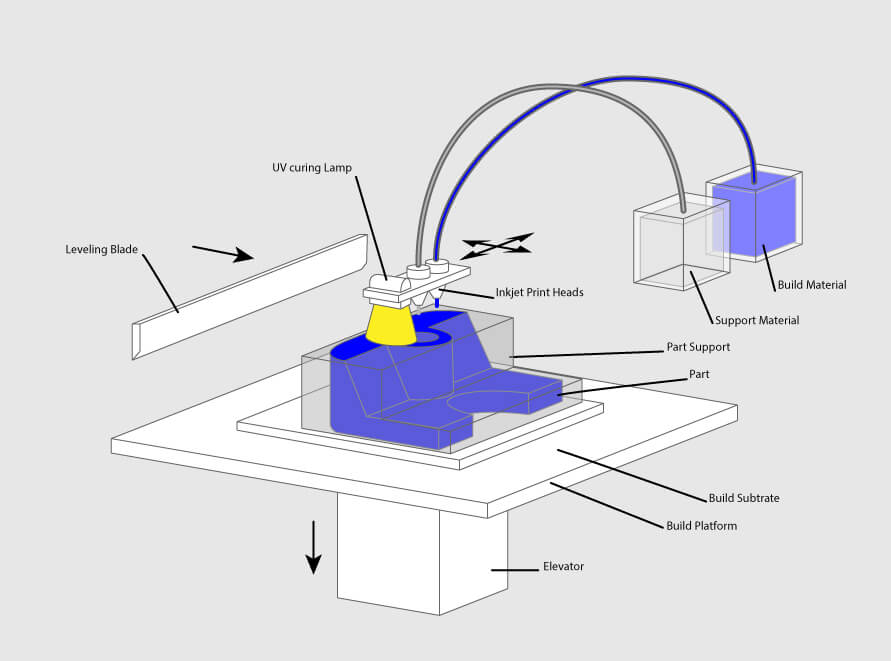
Binder Jetting
przy Binder jetting stosuje się dwa materiały: proszek i płynne spoiwo. W komorze budowlanej proszek rozprowadzany jest w równych warstwach, a spoiwo nanosi się za pomocą dysz strumieniowych, które „kleją” cząstki proszku w wymaganym kształcie. Po zakończeniu nadruku oczyszczany jest pozostały proszek, który często można ponownie wykorzystać drukując następny obiekt. Technologia ta została po raz pierwszy opracowana w Massachusetts Institute of Technology w 1993 roku.
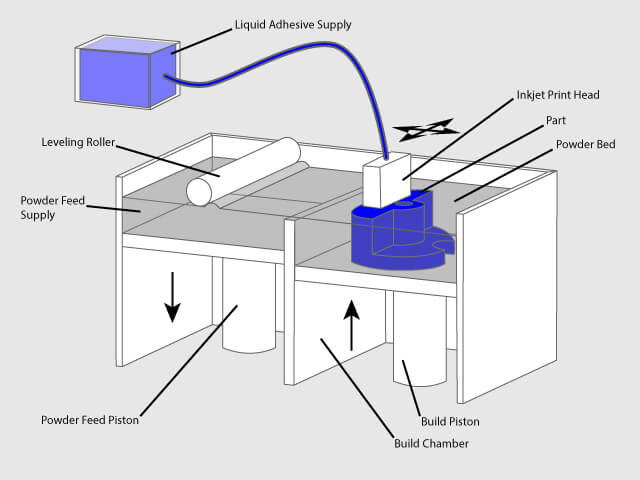
wytłaczanie materiału
Modelowanie topionego osadzania (FDM)
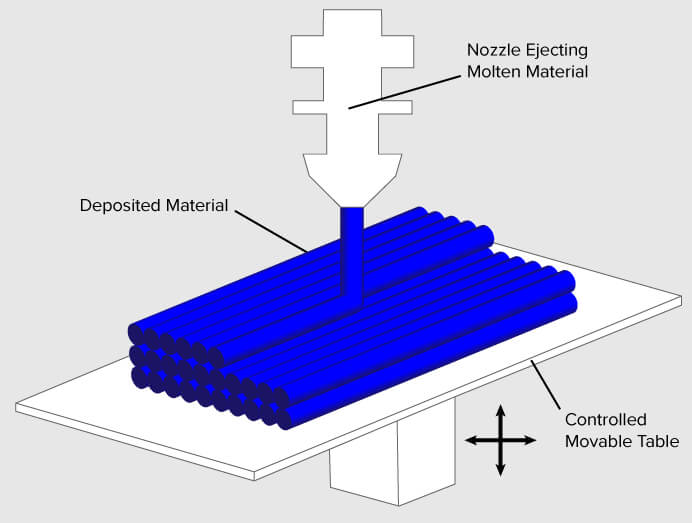
FDM działa przy użyciu filamentu z tworzywa sztucznego, który jest rozwijany ze szpuli i jest dostarczany do dyszy wytłaczania, która może włączać i wyłączać przepływ. Dysza jest podgrzewana w celu stopienia materiału i może być przesuwana zarówno w kierunku poziomym, jak i pionowym za pomocą sterowanego numerycznie mechanizmu. Przedmiot jest wytwarzany przez wytłaczanie stopionego materiału w celu utworzenia warstw, ponieważ materiał twardnieje natychmiast po wytłoczeniu z dyszy.
FDM został wynaleziony przez Scotta Crumpa pod koniec lat 80-tych. Po opatentowaniu tej technologii w 1988 roku założył firmę Stratasys. Termin Fused Deposition Modeling i jego skrót do FDM są znakami towarowymi Stratasys Inc.
Fused Filament Fabrication (FFF)
dokładnie równoważny termin, Fused Filament Fabrication (FFF), został ukuty przez członków projektu RepRap, aby dać wyrażenie, które byłoby prawnie nieskrępowane w jego użyciu.
fuzja złoża proszku
selektywne spiekanie laserowe (SLS)
SLS wykorzystuje laser dużej mocy do wtapiania małych cząstek proszku w masę o pożądanym trójwymiarowym kształcie. Laser selektywnie łączy proszek, najpierw skanując przekroje (lub warstwy) na powierzchni złoża proszku. Po zeskanowaniu każdego przekroju, złoże proszku jest obniżane o jedną grubość warstwy. Następnie nakłada się nową warstwę materiału na wierzch i proces powtarza się, aż obiekt zostanie ukończony.
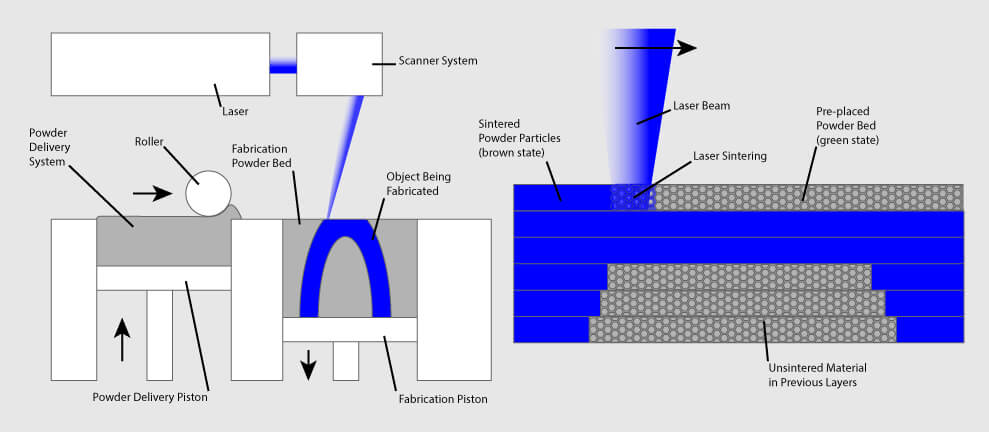
Multi Jet Fusion (MJF)
technologia Multi Jet Fusion została opracowana przez firmę Hewlett Packard i działa z ramieniem zamiatającym, które nanosi warstwę proszku, a następnie innym ramieniem wyposażonym w dysze atramentowe, które selektywnie nanosi środek wiążący na materiał. Wtryskiwacze nakładają również środek do detali wokół spoiwa, aby zapewnić precyzyjną wymiarowość i gładkość powierzchni. Na koniec warstwa jest narażona na wybuch energii cieplnej, który powoduje reakcję czynników.
bezpośrednie spiekanie laserowe metali (DMLS)
DMLS jest zasadniczo taki sam jak SLS, ale zamiast tego używa proszku metalu. Cały niewykorzystany proszek pozostaje taki, jaki jest i staje się strukturą nośną dla obiektu. Niewykorzystany proszek można ponownie wykorzystać do następnego wydruku.
ze względu na zwiększoną moc lasera, DMLS przekształcił się w proces topienia laserowego. Przeczytaj więcej o tej i innych technologiach metalowych na naszej stronie Przegląd technologii metalowych.
laminowanie arkuszy
laminowanie arkuszy obejmuje materiał w arkuszach, który jest związany razem z siłą zewnętrzną. Arkusze mogą być metalowe, papierowe lub w formie polimeru. Blachy są spawane ze sobą za pomocą spawania ultradźwiękowego w warstwach, a następnie frezowane CNC w odpowiedni kształt. Można również użyć arkuszy papieru, ale są one klejone klejem i cięte w kształcie za pomocą precyzyjnych ostrzy.
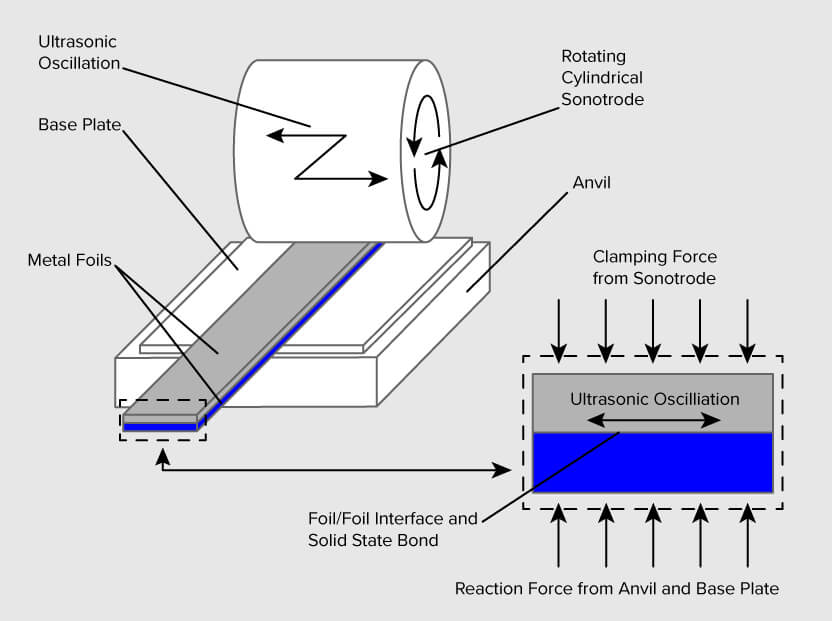
ukierunkowane osadzanie energii
proces ten jest stosowany głównie w przemyśle metalowym i w szybkich zastosowaniach produkcyjnych. Urządzenie do drukowania 3D jest zwykle przymocowane do wieloosiowego ramienia robota i składa się z dyszy, która osadza metalowy proszek lub drut na powierzchni oraz źródła energii (laser, wiązka elektronów lub łuk plazmowy), które topi go, tworząc stały obiekt.
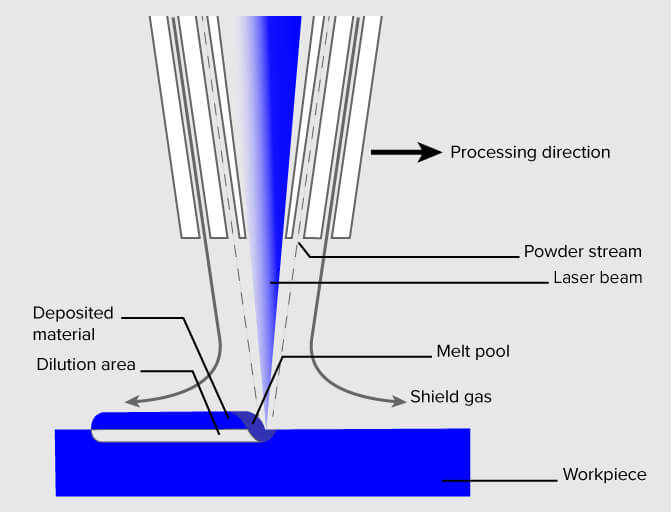
materiały
w produkcji addytywnej można stosować wiele materiałów: Tworzywa sztuczne, metale, Beton, ceramikę, Papier i niektóre Artykuły spożywcze (np. czekoladę). Materiały są często wytwarzane w surowcu drucianym, zwanym włóknem, w postaci proszku lub płynnej żywicy. Dowiedz się więcej o naszych polecanych materiałach na naszej stronie Materiały.
usługi
chcesz wdrożyć druk 3D w swoim procesie produkcyjnym? Uzyskaj wycenę niestandardowej części lub zamów próbki na naszej stronie usługi drukowania 3D.