imprimarea 3D sau fabricarea aditivă este un proces de realizare a obiectelor solide tridimensionale dintr-un fișier digital.
crearea unui obiect imprimat 3D se realizează folosind procese aditive. Într-un proces aditiv, un obiect este creat prin stabilirea unor straturi succesive de material până când obiectul este creat. Fiecare dintre aceste straturi poate fi văzut ca o secțiune transversală subțire a obiectului.
imprimarea 3D este opusul fabricării substractive, care este tăierea / scobirea unei bucăți de metal sau plastic cu, de exemplu, o mașină de frezat.
imprimarea 3D vă permite să produceți forme complexe folosind mai puțin material decât metodele tradiționale de fabricație.
newsletter-ul nostru este gratuit & vă puteți dezabona în orice moment.
cum funcționează imprimarea 3D?
totul începe cu un model 3D. Puteți opta pentru a crea unul de la sol în sus sau descărcați-l dintr-o bibliotecă 3D.
Software 3D
există multe instrumente software diferite disponibile. De la grad industrial la open source. Am creat o prezentare generală pe pagina noastră de software 3D.
recomandăm adesea începătorilor să înceapă cu Tinkercad. Tinkercad este gratuit și funcționează în browserul dvs., nu trebuie să îl instalați pe computer. Tinkercad oferă lecții pentru începători și are o caracteristică încorporată pentru a exporta modelul dvs. ca fișier imprimabil, de ex.STL sau .OBJ.
acum că aveți un fișier imprimabil, următorul pas este să îl pregătiți pentru imprimanta 3D. Aceasta se numește feliere.
feliere: De la fișierul imprimabil la imprimanta 3D
felierea înseamnă practic felierea unui model 3D în sute sau mii de straturi și se face cu software-ul de feliere.
când fișierul este tăiat, este gata pentru imprimanta 3D. Alimentarea fișierului la imprimantă se poate face prin USB, SD sau Wi-Fi. Fișierul dvs. feliat este acum gata să fie imprimat 3D strat cu strat.
industria de imprimare 3D
adoptarea imprimării 3D a atins masa critică, deoarece cei care încă nu au integrat producția aditivă undeva în lanțul lor de aprovizionare fac acum parte dintr-o minoritate în continuă scădere. În cazul în care imprimarea 3D a fost potrivită doar pentru prototipuri și fabricație unică în primele etape, acum se transformă rapid într-o tehnologie de producție.
cea mai mare parte a cererii actuale de imprimare 3D este de natură industrială. Acumen Research and Consulting prognozează că piața globală de imprimare 3D va ajunge la 41 de miliarde de dolari până în 2026.
pe măsură ce evoluează, tehnologia de imprimare 3D este destinată să transforme aproape fiecare industrie majoră și să schimbe modul în care trăim, lucrăm și ne jucăm în viitor.
Exemple de imprimare 3D
imprimarea 3D cuprinde multe forme de tehnologii și materiale, deoarece imprimarea 3D este utilizată în aproape toate industriile la care vă puteți gândi. Este important să o vedem ca un grup de industrii diverse, cu o multitudine de aplicații diferite.
câteva exemple:
- – produse de larg consum (ochelari, încălțăminte, design, mobilier)
- – produse industriale (unelte de fabricație, prototipuri, piese funcționale de utilizare finală)
- -produse dentare
- – proteze
- – modele la scară arhitecturală & machete
- – reconstituirea fosilelor
- – replicarea fosilelor antice artefacte
- – reconstituirea dovezilor în patologia criminalistică
- – recuzită pentru filme
prototipuri rapide & producție rapidă
companiile au folosit imprimante 3D în procesul lor de proiectare pentru a crea prototipuri de la sfârșitul anilor șaptezeci. Utilizarea imprimantelor 3D în aceste scopuri se numește prototipare rapidă.
De ce să folosiți imprimante 3D pentru prototipuri rapide?
pe scurt: este rapid și relativ ieftin. De la idee, la modelul 3D până la deținerea unui prototip în mâinile tale este o chestiune de zile în loc de săptămâni. Iterații sunt mai ușor și mai ieftin de a face și nu aveți nevoie de matrite scumpe sau instrumente.
pe lângă prototiparea rapidă, imprimarea 3D este utilizată și pentru fabricarea rapidă. Fabricarea rapidă este o nouă metodă de fabricație în care întreprinderile folosesc imprimante 3D pentru fabricarea personalizată pe termen scurt / lot mic.
Automotive
producătorii de mașini utilizează imprimarea 3D de mult timp. Companiile auto tipăresc piese de schimb, scule, dispozitive de fixare și accesorii, dar și piese de uz final. Imprimarea 3D a permis producția la cerere, ceea ce a dus la niveluri mai scăzute ale stocurilor și a scurtat ciclurile de proiectare și producție.
pasionații de automobile din întreaga lume folosesc piese tipărite 3D pentru a restabili mașinile vechi. Un astfel de exemplu este atunci când inginerii australieni au tipărit piese pentru a readuce la viață un Delage Type-C. Procedând astfel, au trebuit să tipărească Piese care au fost scoase din producție de zeci de ani.
Aviație
industria aviatică utilizează imprimarea 3D în multe moduri diferite. Următorul exemplu marchează o importantă etapă de fabricație a imprimării 3D: GE Aviation a tipărit 3D 30.000 de duze de combustibil Cobalt-crom pentru motoarele sale de avioane LEAP. Au atins această etapă în octombrie 2018 și, având în vedere că produc 600 pe săptămână pe patruzeci de imprimante 3D, este probabil mult mai mare decât acum.
aproximativ douăzeci de părți individuale care anterior trebuiau sudate împreună au fost consolidate într-o componentă imprimată 3D care cântărește cu 25% mai puțin și este de cinci ori mai puternică. Motorul LEAP este cel mai bine vândut motor din industria aerospațială datorită nivelului ridicat de eficiență și GE economisește 3 milioane de dolari pe aeronavă prin imprimarea 3D a duzelor de combustibil, astfel încât această singură piesă tipărită 3D generează sute de milioane de dolari de beneficii financiare.
duzele de combustibil ale GE și-au făcut drum și în Boeing 787 Dreamliner, dar nu este singura piesă tipărită 3D din 787. Fitingurile structurale lungi de 33 de centimetri care țin bucătăria din spate la corpul aeronavei sunt tipărite 3D de o companie numită Norsk Titanium. Norsk a ales să se specializeze în titan, deoarece are un raport rezistență-greutate foarte mare și este destul de scump, ceea ce înseamnă că reducerea deșeurilor permisă de imprimarea 3D are un impact financiar mai semnificativ decât în comparație cu metalele mai ieftine, unde costurile deșeurilor materiale sunt mai ușor de absorbit. Mai degrabă decât sinterizarea pulberii metalice cu un laser ca majoritatea imprimantelor 3D metalice, Norsk Merke 4 folosește un arc de plasmă pentru a topi un fir metalic într-un proces numit Depunere Rapidă în plasmă (o formă de depunere de energie direcționată) care poate depune până la 10 kg de titan pe oră. O parte din titan de 2 kg ar necesita, în general, un bloc de titan de 30 kg pentru a-l prelucra, generând 28 kg de deșeuri, dar imprimarea 3D a aceleiași părți necesită doar 6 kg de sârmă de titan.
Constructii
este posibil pentru a imprima o clădire? – da, este. Casele tipărite 3D sunt deja disponibile în comerț. Unele companii imprimă piese prefabricate, iar altele o fac la fața locului.
majoritatea poveștilor de imprimare din beton pe care le analizăm pe acest site web sunt axate pe sisteme de imprimare din beton la scară largă, cu duze destul de mari pentru un debit mare. Este minunat pentru așezarea straturilor de beton într-o manieră destul de rapidă și repetabilă. Dar pentru lucrări concrete cu adevărat complicate, care utilizează pe deplin capacitățile de imprimare 3D necesită ceva puțin mai agil și cu o atingere mai fină.
produse de consum
când am început să scriem pe blog despre imprimarea 3D în 2011, imprimarea 3D nu era pregătită pentru a fi utilizată ca metodă de producție pentru volume mari. În zilele noastre există numeroase exemple de produse de consum tipărite 3D pentru uz final.
încălțăminte
gama Adidas 4D are o talpă intermediară imprimată complet 3D și este tipărită în volume mari. Am făcut un articol atunci, explicând cum Adidas a lansat inițial doar 5.000 de perechi de pantofi pentru public și și-a propus să vândă 100.000 de perechi de modele infuzate AM până în 2018.
cu cele mai recente iterații ale pantofului, se pare că au depășit acest obiectiv sau sunt pe cale să-l depășească. Pantofii sunt disponibili în întreaga lume de la magazinele locale Adidas și, de asemenea, de la diverse puncte de vânzare online 3rd party.
Ochelari
se estimează că piața ochelarilor tipăriți 3D va ajunge la 3,4 miliarde de dolari până în 2028. O secțiune în creștere rapidă este cea a cadrelor de utilizare finală. Imprimarea 3D este o metodă de producție deosebit de potrivită pentru ramele de ochelari, deoarece măsurătorile unui individ sunt ușor de procesat în produsul final.
dar știați că este posibilă și imprimarea lentilelor 3D? Lentilele tradiționale de sticlă nu încep subțiri și ușoare; sunt tăiate dintr-un bloc mult mai mare de material numit martor, din care aproximativ 80% se risipesc. Când luăm în considerare câți oameni poartă ochelari și cât de des au nevoie pentru a obține o pereche nouă, 80% din aceste numere reprezintă o mulțime de deșeuri. În plus, laboratoarele trebuie să păstreze stocuri uriașe de spații libere pentru a satisface nevoile de viziune personalizate ale clienților lor. În cele din urmă, însă, tehnologia de imprimare 3D a avansat suficient pentru a oferi lentile oftalmice personalizate de înaltă calitate, eliminând costurile deșeurilor și inventarului din trecut. Imprimanta 3d Luxexcel VisionEngine utilizează un monomer acrilat curabil UV pentru a imprima două perechi de lentile pe oră care nu necesită lustruire sau post-procesare de orice fel. Zonele focale pot fi, de asemenea, complet personalizate, astfel încât o anumită zonă a obiectivului să poată oferi o claritate mai bună la distanță, în timp ce o zonă diferită a obiectivului oferă o viziune mai bună de aproape.
Bijuterii
există două moduri de a produce bijuterii cu o imprimantă 3d. Puteți utiliza fie un proces de producție direct sau indirect. Direct se referă la crearea unui obiect direct din designul 3D, în timp ce fabricarea indirectă înseamnă că obiectul (modelul) care este tipărit 3D este utilizat în cele din urmă pentru a crea o matriță pentru turnarea investițiilor.
asistență medicală
nu este neobișnuit în aceste zile să vezi titluri despre implanturile tipărite 3D. Adesea, aceste cazuri sunt experimentale, ceea ce poate face să pară că imprimarea 3D este încă o tehnologie marginală în sectoarele medicale și de asistență medicală, dar nu mai este cazul. În ultimul deceniu, peste 100.000 de înlocuitori de șold au fost tipăriți 3D de GE Additive.
Cupa Delta-TT proiectată de Dr. Guido Grappiolo și LimaCorporate este fabricat din Titan Trabecular, care se caracterizează printr-o structură celulară regulată, tridimensională, hexagonală, care imită morfologia osului trabecular. Structura trabeculară crește biocompatibilitatea titanului prin încurajarea creșterii osoase în implant. Unele dintre primele implanturi Delta-TT sunt încă puternice peste un deceniu mai târziu.
o altă componentă de asistență medicală tipărită 3D care face o treabă bună de a fi nedetectabilă este aparatul auditiv. Aproape fiecare aparat auditiv din ultimii 17 ani a fost tipărit 3D datorită unei colaborări între Materialise și Phonak. Phonak a dezvoltat rapid Shell Modeling (RSM) în 2001. Înainte de RSM, realizarea unui aparat auditiv a necesitat nouă pași laborioși care implică sculptarea mâinilor și fabricarea mucegaiului, iar rezultatele au fost adesea nepotrivite. Cu RSM, un tehnician folosește silicon pentru a face o impresie a canalului urechii, acea impresie este scanată 3D, iar după unele modificări minore, modelul este imprimat 3D cu o imprimantă 3D din rășină. Electronica este adăugată și apoi este expediată utilizatorului. Folosind acest proces, sute de mii de aparate auditive sunt tipărite 3D în fiecare an.
Dental
în industria dentară, vedem că matrițele pentru aliniatori clari sunt probabil cele mai tipărite obiecte 3D din lume. În prezent, matrițele sunt imprimate 3D atât cu procese de imprimare 3D pe bază de rășină, cât și pe bază de pulbere, dar și prin jet de materiale. Coroanele și protezele sunt deja imprimate direct 3D, împreună cu ghidurile chirurgicale.
bio-imprimare
începând cu primele două mii tehnologia de imprimare 3D a fost studiată de firmele de biotehnologie și mediul academic pentru o posibilă utilizare în aplicații de inginerie tisulară în care organele și părțile corpului sunt construite folosind tehnici cu jet de cerneală. Straturile de celule vii sunt depuse pe un mediu de gel și construite încet pentru a forma structuri tridimensionale. Ne referim la acest domeniu de cercetare cu termenul: bio-imprimare.
alimente
fabricarea aditivilor a invadat industria alimentară cu mult timp în urmă. Restaurante precum Food Ink și Melisse folosesc acest lucru ca un punct de vânzare unic pentru a atrage clienți din întreaga lume.
Educație
educatorii și studenții folosesc de mult timp imprimante 3D în clasă. Imprimarea 3D permite studenților să-și materializeze ideile într-un mod rapid și accesibil.
în timp ce gradele specifice producției aditive sunt destul de noi, universitățile folosesc de mult timp imprimante 3D în alte discipline. Există multe cursuri educaționale pe care le puteți lua pentru a vă angaja cu imprimarea 3D. Universitățile oferă cursuri despre lucruri adiacente imprimării 3D, cum ar fi CAD și design 3D, care pot fi aplicate imprimării 3D într-o anumită etapă.
în ceea ce privește prototiparea, multe programe universitare se îndreaptă către imprimante. Există specializări în fabricarea aditivilor pe care le puteți obține prin grade de arhitectură sau design industrial. Prototipurile tipărite sunt, de asemenea, foarte frecvente în artele, animația și studiile de modă.
tipuri de tehnologii și procese de imprimare 3D
Societatea Americană pentru testare și materiale (ASTM), a dezvoltat un set de standarde care clasifică procesele de fabricație aditivă în 7 categorii. Acestea sunt:
- fotopolimerizare TVA
- stereolitografie (SLA)
- procesare digitală a luminii (DLP)
- producție continuă de interfață lichidă (CLIP)
- Jet de materiale
- Jet de liant
- extrudare de materiale
- modelare prin depunere fuzionată (FDM)
- Fabricare cu Filament fuzionat (FFF)
- pat de pulbere Fusion
- Multi Jet Fusion (MJF)
- sinterizare selectivă cu Laser (SLS)
- sinterizare directă cu laser metalic (DMLS)
- laminare foaie
- depunere de energie direcționată
fotopolimerizare TVA
o imprimantă 3D bazată pe metoda fotopolimerizării TVA are un recipient umplut cu rășină fotopolimerică. Rășina este întărită cu o sursă de lumină UV.
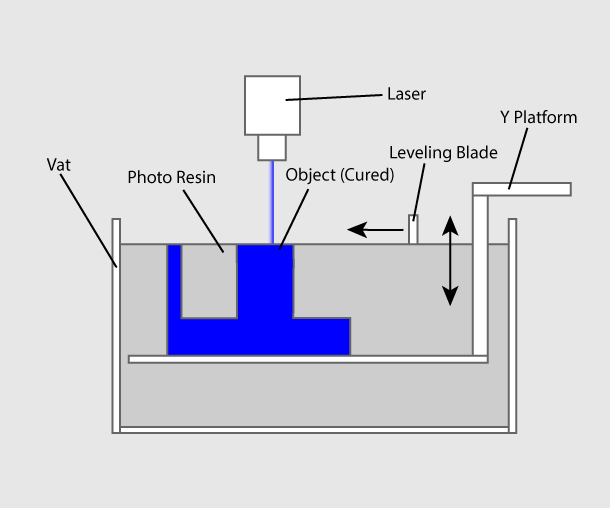
stereolitografie (SLA)
SLA a fost inventat în 1986 de Charles Hull, care, de asemenea, la momentul fondat compania, 3D Systems. Stereolitografia folosește o cuvă de rășină fotopolimerică curabilă lichidă și un laser ultraviolet pentru a construi straturile obiectului pe rând. Pentru fiecare strat, fasciculul laser Urmărește o secțiune transversală a modelului piesei pe suprafața rășinii lichide. Expunerea la lumina laser ultravioletă vindecă și solidifică modelul trasat pe rășină și îl fuzionează cu stratul de mai jos.
după ce modelul a fost urmărit, platforma ascensorului SLA coboară cu o distanță egală cu grosimea unui singur strat, de obicei 0,05 mm până la 0,15 mm (0,002″ până la 0,006″). Apoi, o lamă umplută cu rășină mătură secțiunea transversală a piesei, re-acoperind-o cu material proaspăt. Pe această nouă suprafață lichidă, modelul de strat ulterior este urmărit, aderând la stratul anterior. În funcție de obiectul & orientarea de imprimare, SLA necesită adesea utilizarea structurilor de sprijin.
Digital Light Processing (DLP)
DLP sau Digital Light Processing se referă la o metodă de imprimare care utilizează polimeri ușori și fotosensibili. Deși este foarte similar cu SLA, diferența cheie este sursa de lumină. DLP utilizează alte surse de lumină, cum ar fi lămpile cu arc. DLP este relativ rapid în comparație cu alte tehnologii de imprimare 3D.
producție continuă de interfață lichidă (CLIP)
unul dintre cele mai rapide procese care utilizează fotopolimerizarea TVA se numește CLIP, prescurtare pentru producția continuă de interfață lichidă, dezvoltată de Carbon.
sinteza digitală a luminii
inima procesului CLIP este tehnologia digitală de sinteză a luminii. În această tehnologie, lumina de la un motor de lumină LED personalizat de înaltă performanță proiectează o secvență de imagini UV expunând o secțiune transversală a părții imprimate 3D, determinând rășina curabilă UV să se vindece parțial într-un mod precis controlat. Oxigenul trece prin fereastra permeabilă la oxigen creând o interfață lichidă subțire de rășină necurățată între fereastră și partea tipărită cunoscută sub numele de zona moartă. Zona moartă este la fel de subțire ca zece microni. În interiorul zonei moarte, oxigenul interzice luminii să vindece rășina situată cel mai aproape de fereastră, permițând astfel fluxul continuu de lichid sub partea imprimată. Chiar deasupra zonei moarte UV proiectat lumina în sus provoacă o cascadă ca întărire a părții.
simpla imprimare numai cu hardware-ul carbonului nu permite Proprietăți de utilizare finală cu aplicații din lumea reală. Odată ce lumina a modelat piesa, Un al doilea proces de întărire programabil atinge proprietățile mecanice dorite prin coacerea piesei imprimate 3D într-o baie termică sau cuptor. Intarirea termica programata Seteaza proprietatile mecanice prin declansarea unei reactii chimice secundare care determina intarirea materialului obtinand proprietatile finale dorite.
componentele imprimate cu tehnologia carbonului sunt la egalitate cu piesele turnate prin injecție. Sinteza digitală a luminii produce proprietăți mecanice consistente și previzibile, creând părți care sunt cu adevărat izotrope.
Jet de Material
în acest proces, materialul este aplicat în picături printr-o duză cu diametru mic, similar cu modul în care funcționează o imprimantă obișnuită de hârtie cu jet de cerneală, dar este aplicat strat cu strat pe o platformă de construcție și apoi întărit de lumina UV.
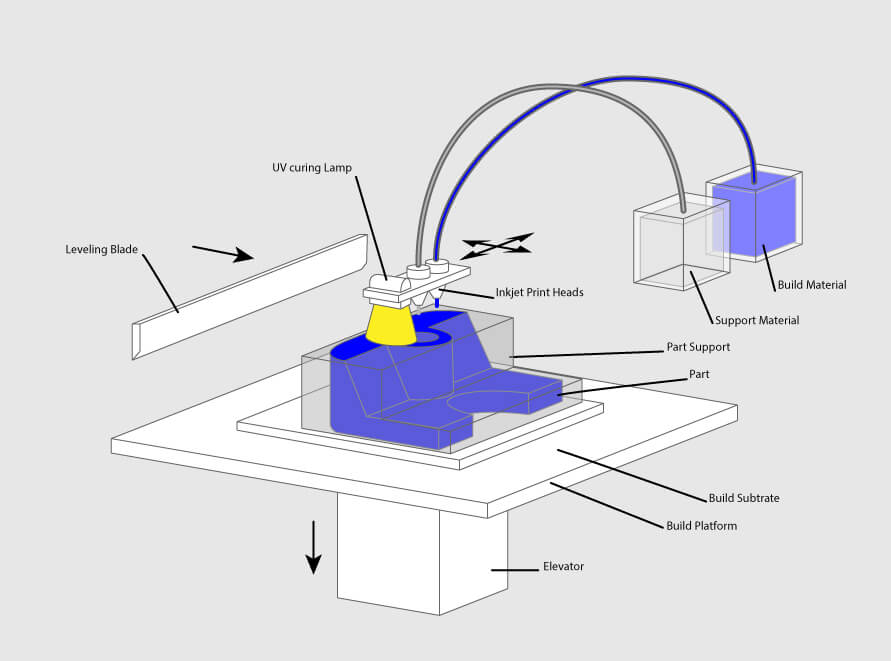
Jet de liant
cu jet de liant se folosesc două materiale: material de bază pentru pulbere și un liant lichid. În camera de construcție, pulberea este răspândită în straturi egale și liantul este aplicat prin duze cu jet care „lipesc” particulele de pulbere în forma necesară. După ce imprimarea este terminată, pulberea rămasă este curățată, care adesea poate fi reutilizată imprimând următorul obiect. Această tehnologie a fost dezvoltată pentru prima dată la Institutul de Tehnologie din Massachusetts în 1993.
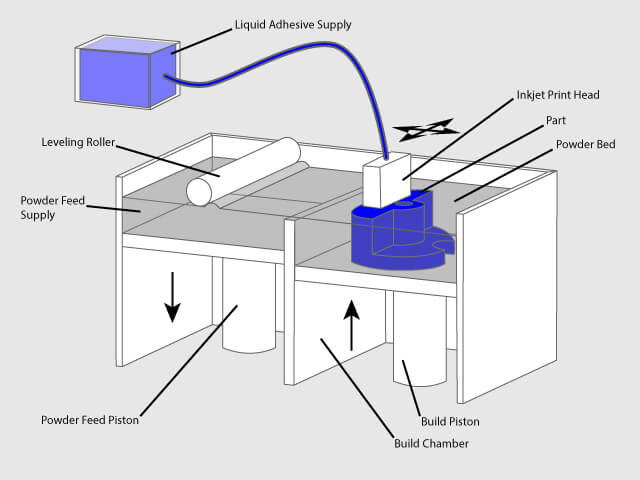
Material extrudare
modelare de depunere topită (FDM)
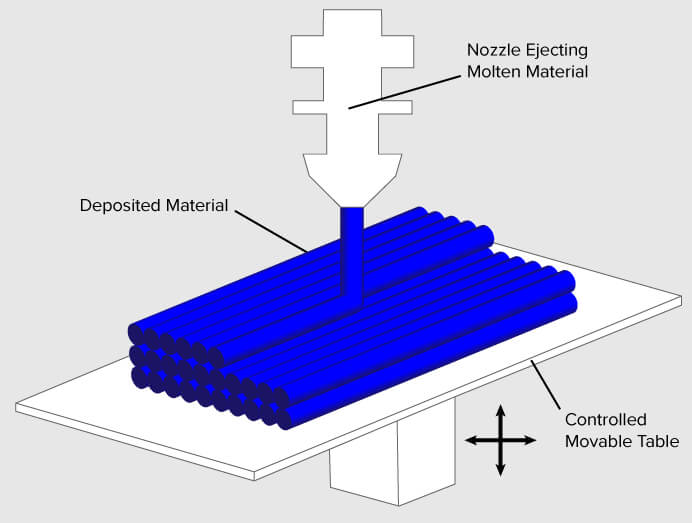
FDM funcționează folosind un filament de plastic care este desfăcut dintr-o bobină și este furnizat la o duză de extrudare care poate porni și opri fluxul. Duza este încălzită pentru a topi materialul și poate fi deplasată atât în direcții orizontale, cât și verticale printr-un mecanism controlat numeric. Obiectul este produs prin extrudarea materialului topit pentru a forma straturi pe măsură ce materialul se întărește imediat după extrudarea din duză.
FDM a fost inventat de Scott Crump la sfârșitul anilor ‘ 80. După brevetarea acestei tehnologii, a început compania Stratasys în 1988. Termenul de modelare a depunerii fuzionate și abrevierea sa la FDM sunt mărci înregistrate de Stratasys Inc.
Fused Filament Fabrication (FFF)
termenul exact echivalent, Fused Filament Fabrication (FFF), a fost inventat de membrii proiectului RepRap pentru a da o frază care ar fi legal fără restricții în utilizarea sa.
pat de pulbere Fusion
sinterizare selectivă cu Laser (SLS)
SLS utilizează un laser de mare putere pentru a fuziona particule mici de pulbere într-o masă care are forma tridimensională dorită. Laserul fuzionează selectiv pulberea scanând mai întâi secțiunile transversale (sau straturile) de pe suprafața unui pat de pulbere. După ce fiecare secțiune transversală este scanată, patul de pulbere este coborât cu o grosime a stratului. Apoi se aplică un nou strat de material deasupra și procesul se repetă până când obiectul este finalizat.
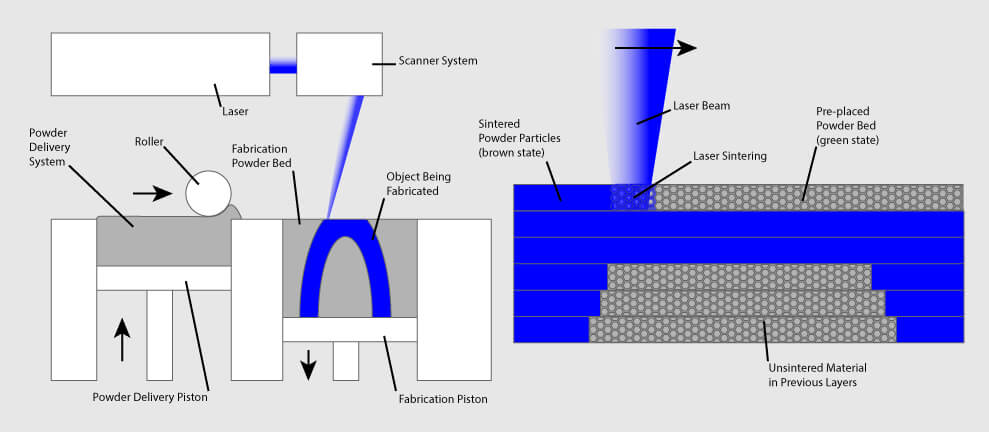
Multi Jet Fusion (MJF)
tehnologia Multi Jet Fusion a fost dezvoltată de Hewlett Packard și funcționează cu un braț de măturat care depune un strat de pulbere și apoi un alt braț echipat cu jeturi de cerneală care aplică selectiv un agent de liant peste material. Jeturile de cerneală depun, de asemenea, un agent de detaliere în jurul liantului pentru a asigura o dimensionalitate precisă și suprafețe netede. În cele din urmă, stratul este expus la o explozie de energie termică care determină reacția agenților.
direct metal laser sinterizare (DMLS)
DMLS este practic la fel ca SLS, dar foloseste pulbere de metal în loc. Toată pulberea neutilizată rămâne așa cum este și devine o structură de sprijin pentru obiect. Pulberea neutilizată poate fi reutilizată pentru următoarea imprimare.
datorită creșterii puterii laserului, DMLS a evoluat într-un proces de topire cu laser. Citiți mai multe despre aceasta și alte tehnologii metalice pe pagina noastră de prezentare a tehnologiilor metalice.
laminarea foilor
laminarea foilor implică materialul din foi care este legat împreună cu forța externă. Foile pot fi metalice, hârtie sau o formă de polimer. Foi de Metal sunt sudate împreună prin sudare cu ultrasunete în straturi și apoi CNC măcinat într-o formă adecvată. Foi de hârtie pot fi utilizate, de asemenea, dar ele sunt lipite cu adeziv adeziv și tăiate în formă de lame precise.
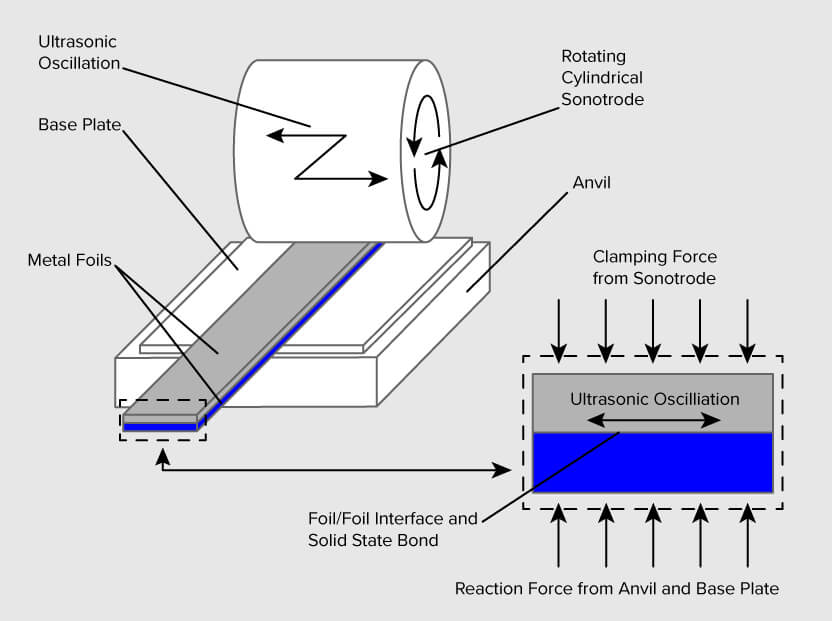
depunerea energiei direcționate
acest proces este utilizat mai ales în industria metalelor și în aplicații rapide de fabricație. Aparatul de imprimare 3D este de obicei atașat la un braț robotizat cu mai multe axe și constă dintr-o duză care depune pulbere metalică sau sârmă pe o suprafață și o sursă de energie (laser, fascicul de electroni sau arc de plasmă) care îl topește, formând un obiect solid.
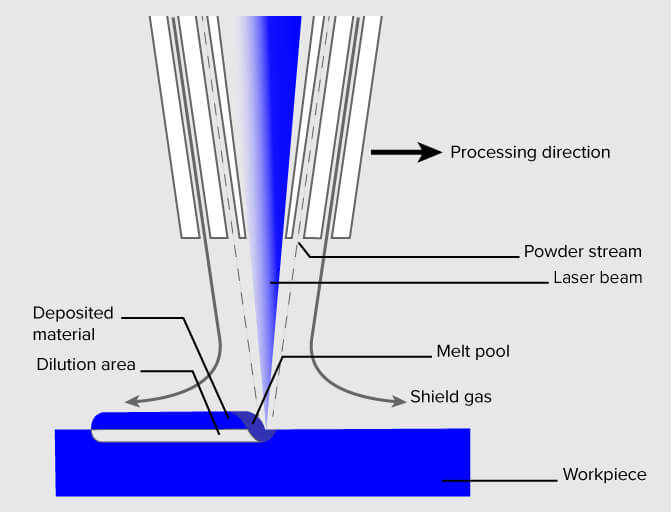
materiale
materiale Multiple pot fi utilizate în fabricarea aditivilor: materiale plastice, metale, beton, ceramică, hârtie și anumite alimente (de exemplu, ciocolată). Materialele sunt adesea produse în materie primă de sârmă alias filament, sub formă de pulbere sau rășină lichidă. Aflați mai multe despre materialele noastre prezentate pe pagina noastră de materiale.
servicii
doriți să implementați imprimarea 3D în procesul de producție? Obțineți o ofertă pentru o piesă personalizată sau mostre de comandă pe pagina noastră de servicii de imprimare 3D.