Die unten beschriebenen Tests wurden entwickelt, um die Fähigkeiten des Schweißers sowie die Qualität des Schweißmetalls und die Festigkeit der Schweißverbindung für jede Art von Metall zu überprüfen, das in Kampfmittelmaterial verwendet wird.
Viele Tests erkennen Defekte, die mit bloßem Auge nicht sichtbar sind.
Zerstörende Prüfungen
Einige dieser Prüfungen, wie Zug- und Biegeversuche, sind zerstörend, da die Prüflinge so lange belastet werden, bis sie versagen, so dass die gewünschten Informationen gewonnen werden können.
Zerstörende Prüfungen sind in zwei Kategorien unterteilt:
- Werkstattprüfungen
- Labortests (korrosiv, chemisch, mikroskopisch, makroskopisch/Lupe)
Zerstörungsfreie Prüfungen (NDT)
Andere Prüfverfahren, wie die Röntgen- und hydrostatischen Prüfungen, sind nicht zerstörend (NDT).
Diese Art der Prüfung wird auch als NDE oder zerstörungsfreie Prüfung und NDI oder zerstörungsfreie Prüfung bezeichnet.
Das Ziel dieser Methoden ist es, die Schweißnähte zu prüfen, ohne Schäden zu verursachen.
Jeder physikalische Prüfansatz für Schweißnähte wird im Folgenden beschrieben.
Zerstörende physikalische Schweißnahtprüfung
Säureätzprüfung
Diese Art oder physikalische Schweißnahtprüfung wird verwendet, um die Solidität einer Schweißnaht zu bestimmen. Die Säure greift an oder reagiert mit den Rändern von Rissen im Grund- oder Schweißgut und offenbart gegebenenfalls Schweißfehler. Es betont auch die Grenze zwischen der Basis und dem Schweißgut und zeigt auf diese Weise die Größe der Schweißnaht, die sonst undeutlich sein könnte. Dieser Test wird normalerweise an einem Querschnitt des Gelenks durchgeführt.
Lösungen von Salzsäure, Salpetersäure, Ammoniumpersulfat oder Jod und Kaliumiodid werden üblicherweise zum Ätzen von Kohlenstoff- und niedriglegierten Stählen verwendet.
Geführter Biegeversuch
Mittels geführter Biegeversuche wird die Qualität des Schweißgutes an der Stirn- und Fußfläche der Schweißverbindung sowie der Grad des Eindringens und Verschweißens mit dem Grundmetall bestimmt. Es zeigt auch die Effizienz der Schweißnaht.
Diese Art der physikalischen Schweißnahtprüfung wird in einer Vorrichtung durchgeführt (Abb. 13-1). Diese Prüfkörper werden aus geschweißten Platten bearbeitet, deren Dicke innerhalb der Kapazität der Biegevorrichtung liegen muss. Der Prüfling wird über die Stützen der Matrize gelegt, die der untere Teil der Vorrichtung ist. Der Kolben, der von oben durch einen hydraulischen Wagenheber oder andere Vorrichtungen betätigt wird, bewirkt, dass die Probe in die Matrize gedrückt wird und die Form der Matrize sicherstellt.
Um die Anforderungen dieses Tests zu erfüllen, müssen sich die Proben um 180 Grad biegen und, um als passierbar akzeptiert zu werden, keine Risse von mehr als 1/8 Zoll aufweisen. (3,2 mm) in jeder Dimension sollte auf der Oberfläche erscheinen. Die Stirnbiegetests werden in der Vorrichtung durchgeführt, wobei die Schweißnaht unter Spannung steht (d. h. an der Außenseite der Biegung) (A – Abb. 13-2). Die Wurzelbiegeprüfungen werden mit der Wurzel der Schweißnaht in Spannung (d. h., an der Außenseite der Biegung) (B – Abb. 13-2). Geführte Biegeprüfkörper sind auch in Abbildung 13-3 dargestellt.
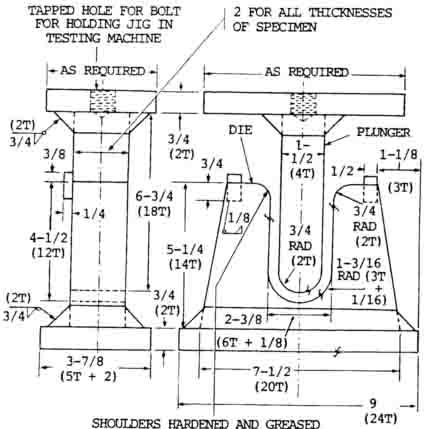
Anmerkungen:
- T =Prüfplattendicke
- Gehärtete Rollen können auf Wunsch auf Schultern verwendet werden
- Spezifische Abmessungen für 3/7 Platte
- Alle angegebenen Abmessungen sind in Zoll
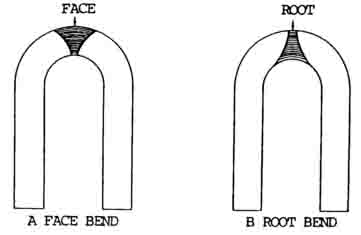
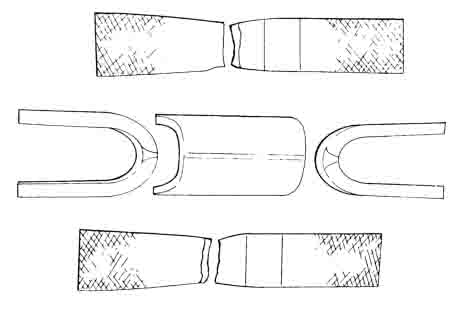
Free Bend Test
Der Ansatz der physikalischen Schweißnahtprüfung Free Bend wurde entwickelt, um die Duktilität des Schweißmetalls zu messen hinterlegt in einer Schweißverbindung. Eine körperliche Schweißungs-Prüfprobe wird von der geschweißten Platte mit der Schweißung maschinell bearbeitet, die lokalisiert wird, wie an A, Abbildung 13-4 gezeigt.
Jede Ecke der Probe muss in einem Radius gerundet sein, der ein Zehntel der Dicke der Probe nicht überschreitet. Werkzeugmarkierungen, falls vorhanden, müssen in Längsrichtung der Probe sein. Zwei Ritzlinien werden 1/16 Zoll auf das Gesicht gelegt. (1,6 mm) vom Rand der Schweißnaht. Der Abstand zwischen diesen Linien wird in Zoll gemessen und als Anfangsabstand X aufgezeichnet (B, Abbildung 13-4). Die Enden des Probekörpers werden dann um Winkel von ungefähr 30 Grad gebogen, wobei diese Biegungen ungefähr ein Drittel der Länge von jedem Ende her betragen. Die Schweißnaht befindet sich somit zentral, um sicherzustellen, dass die gesamte Biegung in der Schweißnaht erfolgt.
Die zunächst gebogene Probe wird dann in eine Maschine gegeben, die eine große Druckkraft ausüben kann (C, Abbildung 13-4), und bis zu einem Riss von mehr als 1/16 Zoll gebogen. (1,6 mm) in jeder Dimension erscheint auf der Fläche der Schweißnaht. Wenn keine Risse auftreten, wird das Biegen fortgesetzt, bis die Proben 1/4 in. (6,4 mm) dick oder unter kann in einem Schraubstock getestet werden. Die schwerere Platte wird in der Regel in einer Presse oder Biegevorrichtung getestet.
Unabhängig davon, ob ein Schraubstock oder eine andere Art von Kompressionsvorrichtung verwendet wird, wenn der freie Biegeversuch durchgeführt wird, ist es ratsam, die oberen und unteren Kontaktplatten der Biegevorrichtung so zu bearbeiten, dass die Oberflächen parallel zu den Enden der Probe liegen (E, Abbildung 13-4). Dies verhindert, dass die Probe beim Biegen verrutscht und aus der Prüfmaschine herausschnappt.
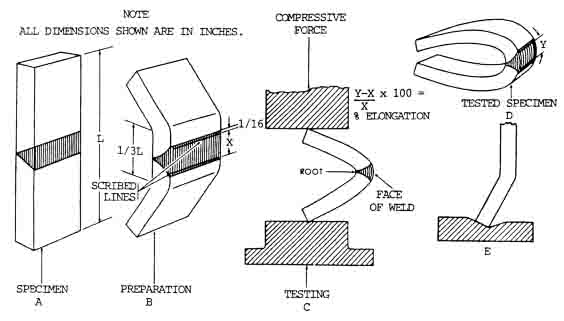
Nach dem Verbiegen des Exemplars zu dem Punkt, in dem die Testbiegung abgeschlossen wird, wird der Abstand zwischen den geritzten Linien auf dem Exemplar wieder gemessen und notiert als der Abstand Y. Um den Prozentsatz der Verlängerung zu finden, subtrahieren Sie den Anfang vom Endabstand, teilen Sie durch den Anfangsabstand und multiplizieren Sie mit 100 (Abbildung 13-4). Die üblichen Anforderungen für das Bestehen dieses Tests sind, dass die Mindestdehnung 15 Prozent beträgt und dass keine Risse größer als 1/16 Zoll sind. (1.6 mm) in beliebiger Dimension auf der Schweißfläche vorhanden.
Der freie Biegeversuch wird weitgehend durch den geführten Biegeversuch ersetzt, bei dem die erforderlichen Prüfmittel zur Verfügung stehen.
Rückbiegetest
Der Rückbiegetest ist eine Art physikalische Schweißnahtprüfung, mit der die Qualität des Schweißmetalls und der Grad des Eindringens in die Wurzel des Y der geschweißten Stoßverbindung bestimmt werden. Die verwendeten Proben ähneln denen, die für den freien Biegetest erforderlich sind, außer dass sie mit der Wurzel der Schweißnaht auf der Zugseite oder außen gebogen werden. Die getesteten Proben müssen sich um 90 Grad biegen, ohne auseinander zu brechen. Dieser Test wird weitgehend durch den geführten Biegeversuch ersetzt.
Nick Break Test
Der Nick Break Test wurde entwickelt, um festzustellen, ob das Schweißgut einer geschweißten Stoßverbindung interne Defekte aufweist, wie z. B. Schlackeneinschlüsse, Gastaschen, schlechtes Schmelzen und / oder oxidiertes oder verbranntes Metall. Die Probe wird aus einer Schweißstoßverbindung entweder durch spanende Bearbeitung oder durch Schneiden mit einem Autogenbrenner erhalten. Jede Kante der Schweißnaht an der Verbindung wird mit einer Säge durch die Mitte geschnitten (Abbildung 13-5). Das so vorbereitete Stück wird über zwei Stahlblöcke (Abbildung 13-5) überbrückt und mit einem schweren Hammer festgeklebt, bis der Abschnitt der Schweißnaht zwischen den Schlitzen bricht.
Das so freigelegte Metall sollte vollständig geschmolzen und frei von Schlackeneinschlüssen sein. Die Größe einer Gastasche darf nicht größer als 1/16 Zoll sein. (1,6 mm) über die größere Abmessung und die Anzahl der Gastaschen oder Poren pro Quadratzoll (64,5 Quadrat-mm) sollte 6 nicht überschreiten.
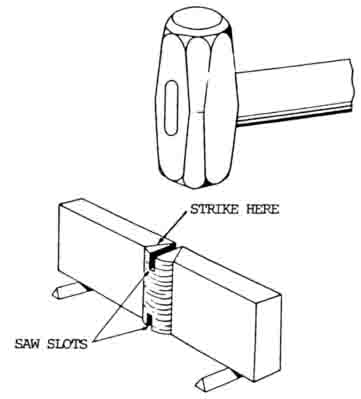
Eine andere Bruchprüfmethode wird verwendet, um die Solidität von Kehlnähten zu bestimmen. Dies ist der Kehlnahtbruch-Test. Eine Kraft, mittels einer Presse, einer Prüfmaschine oder Schläge eines Hammers, wird an die Spitze des V-förmigen Exemplars angewendet, bis die Kehlnaht reißt. Die Oberflächen der Fraktur werden dann auf Solidität untersucht.
Zugfestigkeit Test
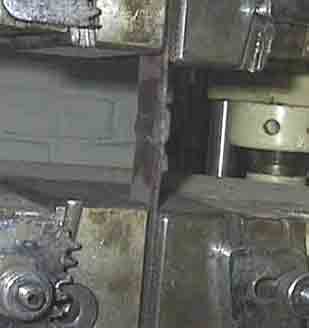
Diese art von physikalische schweiß prüfung ist verwendet zu messen die festigkeit einer schweißverbindung. Ein Teil von a, um die geschweißte Platte zu lokalisieren, ist die Schweißnaht in der Mitte zwischen den Backen der Prüfmaschine zu lokalisieren (Abbildung 1306). Die Breitenstärke des Probekörpers werden vor der Prüfung gemessen, und der Bereich in den Quadratzoll wird berechnet, indem man diese vor der Prüfung multipliziert, und der Bereich in den Quadratzoll wird berechnet, indem man diese zwei Zahlen multipliziert (sehen Sie Formel, Abbildung 13-6).
Der Prüfling für physikalische Zugschweißungen wird dann in einer Maschine montiert, die genügend Zug auf das Stück ausübt, um den Prüfling zu brechen. Die Prüfvorrichtung kann entweder stationär oder tragbar sein. Eine Maschine des tragbaren Typs, die nach dem hydraulischen Prinzip arbeitet und sowohl Prüfkörper ziehen als auch biegen kann, ist in Abbildung 13-7 dargestellt.
Während die Probe in dieser Maschine getestet wird, wird die Last in Pfund auf dem Messgerät registriert. Bei den stationären Typen kann die aufgebrachte Last auf einem Wuchtbalken registriert werden. In beiden Fällen wird die Last am Bruchpunkt aufgezeichnet. Prüfkörper, die durch den Zugfestigkeitstest gebrochen wurden, sind in Abbildung 13-3 dargestellt.
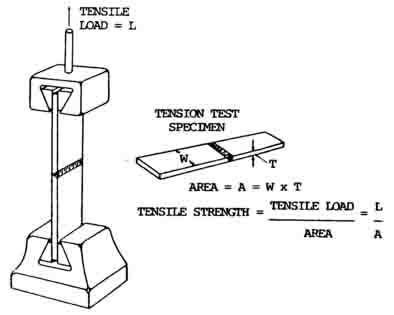
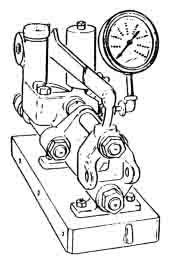
Die Zugfestigkeit, die als Spannung in Pfund pro Quadratzoll definiert ist, wird berechnet, indem die Bruchlast des Prüflings durch die ursprüngliche Querschnittsfläche der Probe dividiert wird. Die üblichen Anforderungen an die Zugfestigkeit von Schweißnähten sind, dass die Probe nicht weniger als 90 Prozent der Zugfestigkeit des unedlen Metalls ziehen muss.
Die Scherfestigkeit von Quer- und Längskehlnähten wird durch Zugbeanspruchung der Prüfkörper bestimmt. Die Breite der Probe wird in Zoll gemessen. Die Probe wird unter Zugbelastung gerissen und die maximale Belastung in Pfund bestimmt. Die Scherfestigkeit der Schweißnaht in Pfund pro linearem Zoll wird bestimmt, indem die maximale Belastung durch die Länge der Kehlnaht geteilt wird, die gerissen ist. Die Scherfestigkeit in Pfund pro Quadratzoll wird erhalten, indem die Scherfestigkeit in Pfund pro Quadratzoll durch das durchschnittliche Halsmaß der Schweißnaht in Zoll dividiert wird. Die Prüfkörper werden breiter als erforderlich gefertigt und auf Maß bearbeitet.
Verwandte Informationen: Häufige Arten von Schweißfehlern
Zerstörungsfreie Prüfungen
Hydrostatischer Test
Dies ist eine zerstörungsfreie Art der physikalischen Schweißnahtprüfung, mit der die Qualität von Schweißnähten an geschlossenen Behältern wie Druckbehältern und Tanks überprüft wird. Der Test besteht normalerweise aus dem Füllen des Behälters mit Wasser und dem Anlegen eines Drucks, der größer als der Arbeitsdruck des Behälters ist. Manchmal werden große Tanks mit Wasser gefüllt, das nicht unter Druck steht, um mögliche Leckagen durch defekte Schweißnähte zu erkennen. Eine andere Methode besteht darin, mit Öl zu testen und dann das Gefäß auszudampfen. Das Versickern von Öl hinter dem Liner zeigt sich sichtbar.
Magnetpulverprüfung
Dies ist eine physikalische Schweißungsprüf- oder Inspektionsmethode für Schweißnähte und Teile aus magnetischen legierten Stählen. Sie gilt nur für ferromagnetische Werkstoffe, bei denen die abgeschiedene Schweißnaht ebenfalls ferromagnetisch ist. Durch elektrische Ströme mit hoher Stromstärke wird im Prüfling ein starkes Magnetfeld aufgebaut.
Ein Leckagefeld wird durch jede Diskontinuität eingerichtet, die dieses Feld im Teil abfängt. Lokale Pole werden durch das Leckfeld erzeugt. Diese Pole ziehen magnetische Partikel an und halten sie fest, die zu diesem Zweck auf der Oberfläche platziert werden. Das auf der Oberfläche erzeugte Partikelmuster zeigt das Vorhandensein einer Diskontinuität oder eines Defekts auf oder nahe der Oberfläche des Teils an.
Röntgenprüfung
Dies ist eine radiographische physikalische Schweißnahtprüfmethode, die verwendet wird, um das Vorhandensein und die Art von inneren Defekten in einer Schweißnaht, wie Risse, Schlacke, Blaslöcher und Zonen, in denen eine ordnungsgemäße Fusion fehlt, aufzudecken. In der Praxis wird eine Röntgenröhre auf einer Seite der geschweißten Platte und ein Röntgenfilm mit einer speziellen empfindlichen Emulsion auf der anderen Seite platziert. Bei der Entwicklung zeigen sich die Defekte im Metall als dunkle Flecken und Bänder, die von einem mit dieser Inspektionsmethode erfahrenen Bediener interpretiert werden können.
Porosität und fehlerhafte Wurzelpenetration, wie durch Röntgeninspektion offenbart, sind in Abbildung 13-8 dargestellt.
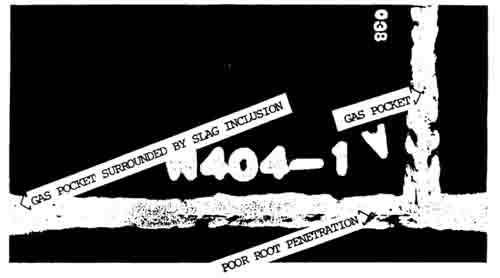
Anweisungen zum Umgang mit Röntgengeräten zur Vermeidung von ahrm für das Bedienpersonal finden Sie in der: American Standard Code for the Industrial Use of X-rays
Gamma Ray Test
Bei diesem Test handelt es sich um ein radiographisches physikalisches Schweißprüf- und Inspektionsverfahren, das dem im Absatz über Säureätztests beschriebenen Röntgenverfahren ähnelt, mit der Ausnahme, dass die Gammastrahlen von einer Kapsel aus Radiumsulfat anstelle einer Röntgenröhre ausgehen.
Aufgrund der kurzen Wellenlängen von Gammastrahlen ist das Eindringen von Abschnitten beträchtlicher Dicke möglich, aber die für die Belichtung erforderliche Zeit für jede Metalldicke ist aufgrund der langsameren Geschwindigkeit, mit der die Gammastrahlen erzeugt werden, viel länger als die für Röntgenstrahlen erforderliche Zeit.
Röntgenprüfungen werden für die meisten Röntgeninspektionen verwendet, aber Gammastrahlengeräte haben den Vorteil, dass sie extrem tragbar sind.
Fluoreszenzeindringprüfung (Farbtest)
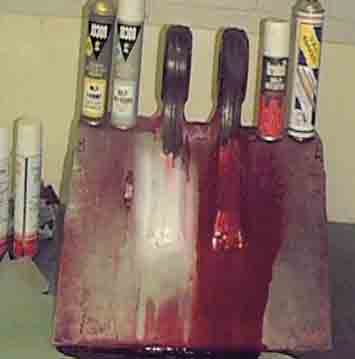
HB = Brinell härte anzahl
D = ball durchmesser (mm),
d = durchmesser der resultierenden, erholt kreisförmigen einzug (mm)
P = angewendet last (kg)
Andere Tests sind Vickers Diamond Pyramid und Scleroscope.
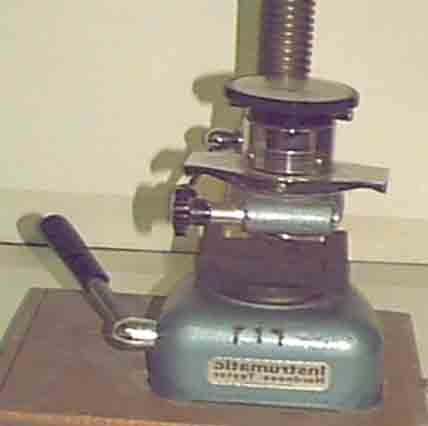
Magnaflux-Test
Dieses ist eine schnelle, zerstörungsfreie körperliche Schweißungs-Prüfmethode für das Lokalisieren von Defekten an oder nahe der Oberfläche des Stahls und seiner magnetischen Legierungen mittels der korrekten Magnetisierung und der Anwendung von ferromagnetischen Partikeln.
Grundprinzipien
Für alle praktischen Zwecke kann die Magnaflux-Inspektion mit der Verwendung einer Lupe als physikalische Schweißnahtprüfmethode verglichen werden. Anstelle eines Glases werden jedoch ein Magnetfeld und ferromagnetische Pulver verwendet. Die Methode der Magnetpulverprüfung basiert auf zwei Prinzipien: Erstens, dass ein Magnetfeld in einem Metallstück erzeugt wird, wenn ein elektrischer Strom durch oder um es herum fließt; zwei, dass winzige Pole auf der Oberfläche des Metalls aufgestellt werden, wo immer dieses Magnetfeld gebrochen oder verzerrt ist.
Wenn ferromagnetische Partikel in die Nähe eines magnetisierten Teils gebracht werden, werden sie von diesen Polen stark angezogen und fester an ihnen gehalten als an der übrigen Oberfläche des Teils, wodurch ein sichtbares Zeichen gebildet wird.
Wirbelstrom (Elektromagnetische Prüfung)
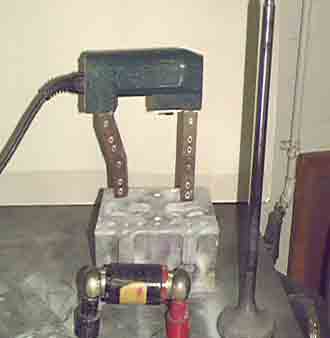
Die Wirbelstrom- (elektromagnetische) Prüfung ist eine zerstörungsfreie Prüfmethode, die auf dem Prinzip basiert, dass in jedem Leiter, der einem sich ändernden Magnetfeld ausgesetzt ist, ein elektrischer Strom fließt. Es wird verwendet, um Schweißnähte in magnetischen und nichtmagnetischen Materialien zu überprüfen und ist besonders nützlich bei der Prüfung von Stäben, Filets, geschweißten Rohren und Rohren. Die Frequenz kann von 50 Hz bis 1 MHz variieren, abhängig von der Art und Dicke des Materials aktuellen Methoden. Ersteres bezieht sich auf Prüfungen, bei denen die magnetische Permeabilität eines Materials die Prüfergebnisse beeinflusst, und letzteres auf Prüfungen, bei denen die elektrische Leitfähigkeit der Faktor ist.
Zerstörungsfreie physikalische Schweißnahtprüfungen mit Wirbelstromverfahren umfassen das Induzieren elektrischer Ströme (Wirbel- oder Foucault-Ströme) in einem Prüfling und das Messen der Änderungen, die in diesen Strömen durch Diskontinuitäten oder andere physikalische Unterschiede im Prüfling erzeugt werden. Solche Tests können nicht nur zur Erkennung von Diskontinuitäten verwendet werden, sondern auch zur Messung von Variationen der Probekörperabmessungen und des spezifischen Widerstands. Da der spezifische Widerstand von Eigenschaften wie chemischer Zusammensetzung (Reinheit und Legierung), Kristallorientierung, Wärmebehandlung und Härte abhängt, können diese Eigenschaften auch indirekt bestimmt werden. Elektromagnetische Verfahren werden als magnetisch-induktive und Wirbelstromverfahren klassifiziert. Ersteres bezieht sich auf Prüfungen, bei denen die magnetische Permeabilität eines Materials die Prüfergebnisse beeinflusst, und letzteres auf Prüfungen, bei denen die elektrische Leitfähigkeit der Faktor ist.
Eine Methode zur Erzeugung von Wirbelströmen in einem Prüfling besteht darin, den Prüfling zum Kern einer Wechselstrom-Induktionsspule zu machen. Es gibt zwei Möglichkeiten, Änderungen zu messen, die in der Größe und Verteilung dieser Ströme auftreten. Die erste besteht darin, die resistive Komponente der Impedanz der Erregerspule (oder einer sekundären Testspule) zu messen, und die zweite besteht darin, die induktive Komponente der Impedanz der Erregerspule (oder einer sekundären Spule) zu messen. Elektronische Geräte wurden entwickelt, um entweder die resistiven oder induktiven Impedanzkomponenten einzeln oder beide gleichzeitig zu messen.
Durch elektromagnetische Wechselinduktion oder Transformatorwirkung werden Wirbelströme in den leitenden Prüfling induziert. Wirbelströme sind elektrischer Natur und haben alle Eigenschaften, die mit elektrischen Strömen verbunden sind. Bei der Erzeugung von Wirbelströmen wird der Prüfling, der ein Leiter sein muss, in das Feld einer wechselstromführenden Spule gebracht. Die Spule kann das Teil umgeben, vielleicht in Form einer Sonde, oder im Falle von Rohrformen, vielleicht gewickelt, um in ein Rohr oder Rohr zu passen. Ein Wirbelstrom in der Metallprobe baut auch ein eigenes Magnetfeld auf, das dem ursprünglichen Magnetfeld entgegengesetzt ist. Die Impedanz der Erregerspule oder einer mit der ersten gekoppelten zweiten Spule in unmittelbarer Nähe der Probe wird durch das Vorhandensein der induzierten Wirbelströme beeinflusst. Diese zweite Spule wird oft als Bequemlichkeit verwendet und wird als Sensing oder Pick up Coil bezeichnet. Der Weg des Wirbelstroms wird durch das Vorhandensein einer Diskontinuität verzerrt. Ein Riss lenkt Wirbelströme ab und erzeugt sie. Auf diese Weise wird die Scheinimpedanz der Spule durch das Vorhandensein des Defekts verändert. Diese Änderung kann gemessen werden und wird verwendet, um einen Hinweis auf Defekte oder Unterschiede in der physikalischen, chemischen und metallurgischen Struktur zu geben. Unterirdische Diskontinuitäten können ebenfalls erkannt werden, aber der Strom fällt mit der Tiefe ab.
Akustische Emissionsprüfung
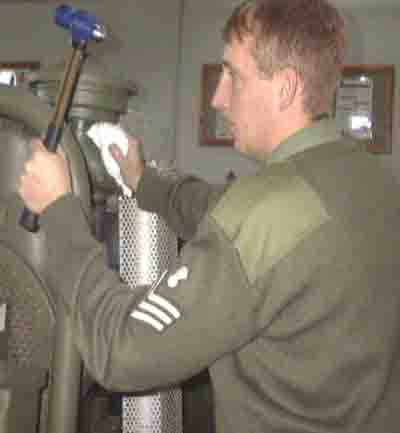
Akustische Emissionsprüfung (AET) Physikalische Schweißnahtprüfverfahren gelten derzeit als Ergänzung zu anderen zerstörungsfreien Prüfverfahren. Sie wurden jedoch während Proof-Tests, wiederkehrenden Inspektionen, Service und Fertigung angewendet.
Die Schallemissionsprüfung besteht in der Erfassung akustischer Signale, die durch plastische Verformung oder Rissbildung während der Belastung entstehen. Diese Signale sind in einem breiten Frequenzspektrum zusammen mit Umgebungsgeräuschen aus vielen anderen Quellen vorhanden. Wandler, die strategisch auf einer Struktur platziert sind, werden durch ankommende Signale aktiviert. Durch geeignete Filterverfahren wird das Umgebungsrauschen im Verbundsignal deutlich reduziert. Jede Quelle signifikanter Signale wird durch Triangulation basierend auf den Ankunftszeiten dieser Signale an den verschiedenen Wandlern aufgetragen.
Ferritprüfung
Auswirkungen des Ferritgehalts
Vollaustenitische Edelstahlschweißablagerungen neigen dazu, auch unter minimalen Bedingungen kleine Risse zu entwickeln. Diese kleinen Risse neigen dazu, sich quer zur Schweißnahtfusionslinie in Schweißdurchgängen und unedlen Metallen zu befinden, die durch nachfolgende Schweißdurchgänge auf nahe den Schmelzpunkt des Materials erwärmt wurden. Risse sind eindeutig schädigende Defekte und können nicht toleriert werden. Auf der anderen Seite ist der Effekt von Rissen auf die Schweißleistung weniger klar, da diese Mikrorisse durch die sehr zähe austenitische Matrix schnell platzen. Rissige Schweißablagerungen haben unter sehr schwierigen Bedingungen zufriedenstellend funktioniert. Eine Tendenz zur Bildung von Rissen geht jedoch im Allgemeinen mit einer Tendenz zu größeren Rissen einher, so dass es oft wünschenswert ist, rissempfindliche Schweißmetalle zu vermeiden.
Das Vorhandensein eines kleinen Bruchteils der magnetischen Delta-Ferritphase in einer ansonsten austenitischen (nichtmagnetischen) Schweißnahtablagerung hat einen Einfluss auf die Verhinderung von Mittellinienrissen und -rissen. Die Menge an Delta-Ferrit in as-geschweißtem Material wird weitgehend durch ein Gleichgewicht in der Schweißmetallzusammensetzung zwischen den ferritfördernden Elementen (Chrom, Silizium, Molybdän und Columbium sind am häufigsten) und den austenitfördernden Elementen (Nickel, Mangan) gesteuert, Kohlenstoff und Stickstoff sind am häufigsten). Übermäßiges Delta-Ferrit kann jedoch nachteilige Auswirkungen auf die Schweißmetalleigenschaften haben. Je größer die Menge an Delta-Ferrit ist, desto geringer ist die Duktilität und Zähigkeit des Schweißgutes. Delta-Ferrit wird auch bevorzugt in einigen korrosiven Umgebungen wie Harnstoff angegriffen. Bei längerer Einwirkung von Temperaturen im Bereich von 900 bis 1700 ° F (482 bis 927 ° C) neigt Ferrit dazu, sich teilweise in eine spröde intermetallische Verbindung umzuwandeln, die das Schweißteil stark versprödet.
Tragbare Ferritindikatoren sind für den Einsatz vor Ort konzipiert. Der Ferritgehalt der Schweißnahtablagerung kann in Prozent Ferrit angegeben und zwischen zwei Werten eingeklammert werden. Dies bietet eine ausreichende Kontrolle in den meisten Anwendungen, in denen ein minimaler Ferritgehalt oder ein Ferritbereich angegeben ist.