Les tests décrits ci-dessous ont été développés pour vérifier les compétences de l’opérateur de soudage ainsi que la qualité du métal de soudure et la résistance du joint soudé pour chaque type de métal utilisé dans les matériaux de munitions.
De nombreux tests détectent des défauts non visibles à l’œil nu.
Essais destructifs
Certains de ces essais, tels que les essais de traction et de flexion, sont destructifs, en ce sens que les éprouvettes sont chargées jusqu’à leur défaillance, ce qui permet d’obtenir les informations souhaitées.
Les essais destructifs se répartissent en deux catégories:
- Essais en atelier
- Essais en laboratoire (corrosifs, chimiques, microscopiques, macroscopiques/ loupe)
Essais non destructifs (CND)
Les autres méthodes d’essai, telles que les essais aux rayons X et hydrostatiques, ne sont pas destructives (CND).
Ce type de test est également appelé NDE ou examen non destructif et NDI ou inspection non destructive.
Le but de ces méthodes est d’examiner les soudures sans causer de dommages.
Chaque méthode d’essai physique de soudure est décrite ci-dessous.
Test de soudure Physique destructive
Test de gravure à l’acide
Ce type ou test de soudure physique est utilisé pour déterminer la solidité d’une soudure. L’acide attaque ou réagit avec les bords des fissures dans la base ou le métal de soudure et révèle des défauts de soudure, le cas échéant. Il accentue également la frontière entre la base et le métal de soudure et, de cette manière, montre la taille de la soudure qui peut autrement être indistincte. Ce test est généralement effectué sur une section transversale de l’articulation.
Des solutions d’acide chlorhydrique, d’acide nitrique, de persulfate d’ammonium ou d’iode et d’iodure de potassium sont couramment utilisées pour graver des aciers au carbone et faiblement alliés.
Test de pliage guidé
La qualité du métal de soudure à la face et à la racine du joint soudé, ainsi que le degré de pénétration et de fusion avec le métal de base, sont déterminés au moyen d’essais de pliage guidés. Il montre également l’efficacité de la soudure.
Ce type de test de soudure physique est réalisé en gabarit (fig 13-1). Ces éprouvettes sont usinées à partir de plaques soudées dont l’épaisseur doit être dans la capacité du gabarit de pliage. L’échantillon d’essai est placé à travers les supports de la matrice qui est la partie inférieure du gabarit. Le piston, actionné par le haut par un vérin hydraulique ou d’autres dispositifs, force l’échantillon à pénétrer et à assurer la forme de la matrice.
Pour satisfaire aux exigences de cet essai, les éprouvettes doivent se plier à 180 degrés et, pour être acceptées comme praticables, aucune fissure supérieure à 1/8 po. (3,2 mm) dans n’importe quelle dimension devrait apparaître sur la surface. Les essais de pliage de face sont réalisés dans le gabarit avec la face de la soudure en tension (c’est–à-dire à l’extérieur du coude) (A-fig 13-2). Les tests de courbure de la racine sont effectués avec la racine de la soudure en tension (c.-à-d., à l’extérieur du virage) (B- fig 13-2). Des éprouvettes de pliage guidées sont également représentées à la figure 13-3.
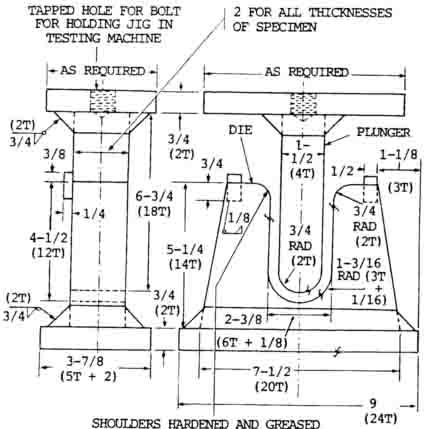
Notes:
- T = Épaisseur de la plaque d’essai
- Des rouleaux durcis peuvent être utilisés sur les épaules si désiré
- Dimensions spécifiques pour la plaque 3/7
- Toutes les dimensions indiquées sont en pouces
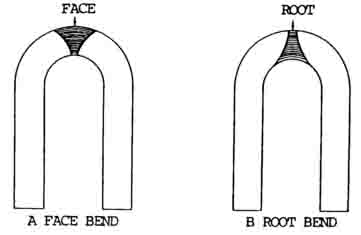
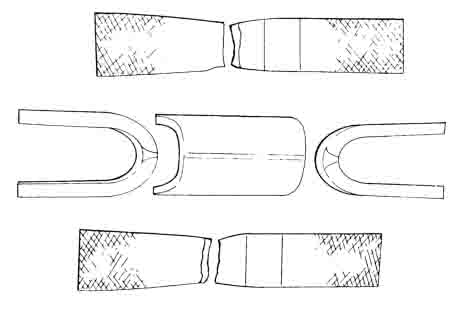
Test de pliage libre
L’approche de test de soudure physique à pliage libre a été conçue pour mesurer la ductilité du métal de soudure déposé dans un joint de soudure. Un échantillon d’essai de soudure physique est usiné à partir de la plaque soudée avec la soudure située comme indiqué à A, figure 13-4.
Chaque coin dans le sens de la longueur de l’échantillon doit être arrondi dans un rayon ne dépassant pas un dixième de l’épaisseur de l’échantillon. Les marques d’outil, le cas échéant, doivent être dans le sens de la longueur de l’échantillon. Deux lignes tracées sont placées sur la face 1/16 po. (1,6 mm) à partir du bord de la soudure. La distance entre ces lignes est mesurée en pouces et enregistrée comme la distance initiale X (B, figure 13-4). Les extrémités de l’éprouvette sont ensuite pliées selon des angles d’environ 30 degrés, ces courbures représentant environ un tiers de la longueur de chaque extrémité. La soudure est ainsi située au centre pour s’assurer que toute la flexion se produit dans la soudure.
L’échantillon plié initialement est ensuite placé dans une machine capable d’exercer une force de compression importante (C, figure 13-4) et plié jusqu’à une fissure supérieure à 1/16 po. (1,6 mm) dans n’importe quelle dimension apparaît sur la face de la soudure. Si aucune fissure n’apparaît, la flexion est poursuivie jusqu’à ce que les éprouvettes atteignent 1/4 po. (6,4 mm) d’épaisseur ou sous peut être testé dans un étau. La plaque la plus lourde est généralement testée dans une presse ou un gabarit de pliage.
Qu’un étau ou un autre type de dispositif de compression soit utilisé lors de l’essai de pliage libre, il est conseillé d’usiner les plaques de contact supérieure et inférieure de l’équipement de pliage pour présenter des surfaces parallèles aux extrémités de l’échantillon (E, figure 13-4). Cela empêchera le spécimen de glisser et de sortir de la machine d’essai lorsqu’il est plié.
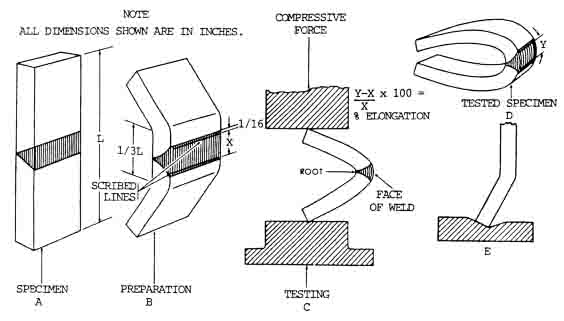
Après avoir plié l’éprouvette jusqu’au point où la courbure d’essai est terminée, la distance entre les lignes tracées sur l’éprouvette est à nouveau mesurée et enregistrée comme la distance Y. Pour trouver le pourcentage d’allongement, soustrayez l’initiale de la distance finale, divisez par la distance initiale et multipliez par 100 (figure 13-4). Les exigences habituelles pour réussir cet essai sont que l’allongement minimum soit de 15% et qu’aucune fissure ne dépasse 1/16 po. (1.6 mm) dans n’importe quelle dimension existent sur la face de la soudure.
L’essai de pliage libre est en grande partie remplacé par l’essai de pliage guidé où l’équipement d’essai requis est disponible.
Test de courbure arrière
L’essai de courbure arrière est un type d’essai de soudure physique utilisé pour déterminer la qualité du métal de soudure et le degré de pénétration dans la racine du Y du joint bout à bout soudé. Les échantillons utilisés sont similaires à ceux requis pour l’essai de pliage libre, sauf qu’ils sont pliés avec la racine de la soudure du côté de la tension, ou à l’extérieur. Les éprouvettes testées doivent se plier à 90 degrés sans se briser. Cet essai est en grande partie remplacé par l’essai de pliage guidé.
Test de rupture de nick
Le test de rupture de nick a été conçu pour déterminer si le métal de soudure d’un joint bout à bout soudé présente des défauts internes, tels que des inclusions de scories, des poches de gaz, une mauvaise fusion et / ou du métal oxydé ou brûlé. L’échantillon est obtenu à partir d’un joint bout à bout soudé soit par usinage, soit par découpe au chalumeau oxyacétylénique. Chaque bord de la soudure au niveau du joint est fendu au moyen d’une scie coupée au centre (figure 13-5). La pièce ainsi préparée est pendue sur deux blocs d’acier (figure 13-5) et collée avec un marteau lourd jusqu’à ce que la section de la soudure entre les fentes se brise.
Le métal ainsi exposé doit être complètement fondu et exempt d’inclusions de scories. La taille d’une poche à gaz ne doit pas dépasser 1/16 po. (1,6 mm) sur la plus grande dimension et le nombre de poches ou de pores de gaz par pouce carré (64,5 mm carrés) ne doit pas dépasser 6.
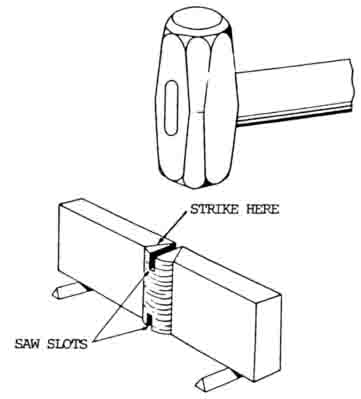
Une autre méthode d’essai de rupture est utilisée pour déterminer la solidité des soudures d’angle. Ceci est le test de rupture de soudure d’angle. Une force, au moyen d’une presse, d’une machine d’essai ou de coups de marteau, est appliquée au sommet de l’échantillon en forme de V jusqu’à ce que la soudure d’angle se rompe. Les surfaces de la fracture seront ensuite examinées pour en vérifier la solidité.
Essai de résistance à la traction
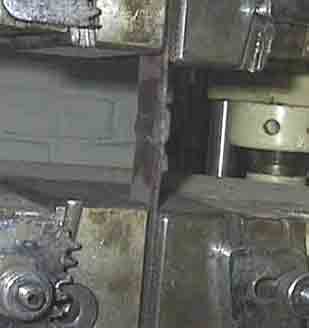
Ce type d’essai de soudure physique est utilisé pour mesurer la résistance d’un joint soudé. Une partie de a pour localiser la plaque soudée consiste à localiser la soudure à mi-chemin entre les mâchoires de la machine d’essai (figure 1306). L’épaisseur de la largeur de l’échantillon d’essai est mesurée avant l’essai, et la surface en pouces carrés est calculée en multipliant celles-ci avant l’essai, et la surface en pouces carrés est calculée en multipliant ces deux chiffres (voir formule, figure 13-6).
L’éprouvette d’essai de soudure physique en traction est ensuite montée dans une machine qui exercera une traction suffisante sur la pièce pour casser l’éprouvette. L’usinage d’essai peut être de type fixe ou portable. Une machine de type portable, fonctionnant sur le principe hydraulique et capable de tirer ainsi que des éprouvettes d’essai de flexion, est représentée à la figure 13-7.
Lorsque l’échantillon est testé dans cette machine, la charge en livres est enregistrée sur la jauge. Dans les types fixes, la charge appliquée peut être enregistrée sur une poutre d’équilibrage. Dans les deux cas, la charge au point de rupture est enregistrée. Les éprouvettes brisées par l’essai de résistance à la traction sont représentées à la figure 13-3.
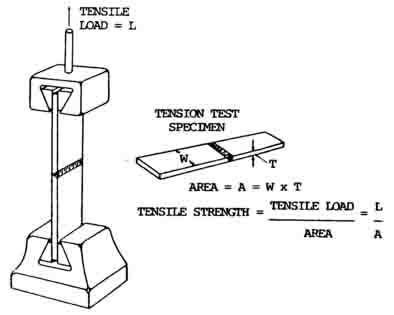
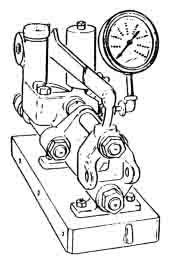
La résistance à la traction, qui est définie comme une contrainte en livres par pouce carré, est calculée en divisant la charge de rupture de l’éprouvette par la section transversale d’origine de l’échantillon. Les exigences habituelles pour la résistance à la traction des soudures sont que l’échantillon ne tire pas moins de 90% de la résistance à la traction du métal de base.
La résistance au cisaillement des soudures d’angle transversales et longitudinales est déterminée par la contrainte de traction sur les éprouvettes. La largeur de l’échantillon est mesurée en pouces. L’échantillon est rompu sous une charge de traction et la charge maximale en livres est déterminée. La résistance au cisaillement de la soudure en livres par pouce linéaire est déterminée en divisant la charge maximale par la longueur de la soudure d’angle qui s’est rompue. La résistance au cisaillement en livres par pouce carré est obtenue en divisant la résistance au cisaillement en livres par pouce linéaire par la dimension moyenne de la gorge de la soudure en pouces. Les éprouvettes sont plus larges que nécessaire et usinées jusqu’à la taille.
Lecture connexe: Types courants de défauts de soudage
Essais non destructifs
Essai hydrostatique
Il s’agit d’un type d’essai physique de soudure non destructif utilisé pour vérifier la qualité des soudures sur des récipients fermés tels que des récipients sous pression et des réservoirs. L’essai consiste généralement à remplir le récipient d’eau et à appliquer une pression supérieure à la pression de service du récipient. Parfois, les grands réservoirs sont remplis d’eau qui n’est pas sous pression pour détecter d’éventuelles fuites à travers des soudures défectueuses. Une autre méthode consiste à tester avec de l’huile, puis à vaporiser le récipient. L’infiltration arrière d’huile par l’arrière de la doublure apparaît visiblement.
Test de particules magnétiques
Il s’agit d’une méthode d’essai ou d’inspection physique des soudures utilisée sur les soudures et les pièces en aciers alliés magnétiques. Elle ne s’applique qu’aux matériaux ferromagnétiques dans lesquels la soudure déposée est également ferromagnétique. Un fort champ magnétique est mis en place dans la pièce à inspecter au moyen de courants électriques à fort ampérage.
Un champ de fuite sera mis en place par toute discontinuité qui intercepte ce champ dans la pièce. Les pôles locaux sont produits par le champ de fuite. Ces pôles attirent et retiennent les particules magnétiques qui sont placées à la surface à cet effet. Le motif de particules produit à la surface indique la présence d’une discontinuité ou d’un défaut sur ou à proximité de la surface de la pièce.
Test aux rayons X
Il s’agit d’une méthode d’essai physique radiographique de soudure utilisée pour révéler la présence et la nature de défauts internes dans une soudure, tels que des fissures, des scories, des trous de soufflage et des zones où une fusion adéquate fait défaut. En pratique, un tube à rayons X est placé d’un côté de la plaque soudée et un film à rayons X, avec une émulsion sensible spéciale, de l’autre côté. Une fois développés, les défauts du métal apparaissent sous forme de taches et de bandes sombres, qui peuvent être interprétées par un opérateur expérimenté dans cette méthode d’inspection.
La porosité et la pénétration radiculaire défectueuse telles que décrites par l’inspection aux rayons X sont illustrées à la figure 13-8.
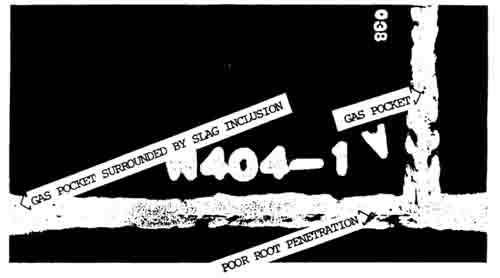
Les instructions de manipulation des appareils à rayons X pour éviter la GRH au personnel d’exploitation se trouvent dans le: American Standard Code for the Industrial Use of X-rays
Gamma Ray Test
Ce test est une méthode d’essai et d’inspection physique des soudures radiographiques similaire à la méthode aux rayons X décrite dans le paragraphe sur les tests de gravure à l’acide, sauf que les rayons gamma émanent d’une capsule de sulfate de radium au lieu d’un tube à rayons X.
En raison des courtes longueurs d’onde des rayons gamma, la pénétration de sections d’épaisseur considérable est possible, mais le temps d’exposition pour toute épaisseur de métal est beaucoup plus long que celui requis pour les rayons X en raison de la vitesse plus lente à laquelle les rayons gamma sont produits.
Les tests aux rayons X sont utilisés pour la plupart des inspections radiographiques, mais les équipements à rayons gamma présentent l’avantage d’être extrêmement portables.
Test de Ressuage fluorescent (Test de Colorant)
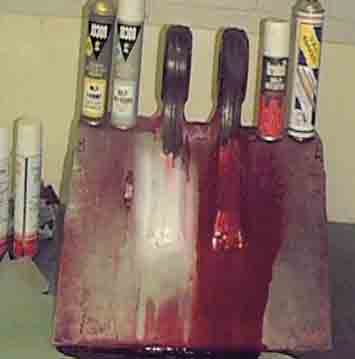
L’inspection par ressuage fluorescent est une méthode d’essai physique de soudure non destructive au moyen de laquelle des fissures, des pores, des fuites et d’autres discontinuités peuvent être localisées dans des matériaux solides. Il est particulièrement utile pour localiser les défauts de surface dans les matériaux non magnétiques tels que l’aluminium, le magnésium et les soudures en acier austénitique et pour localiser les fuites dans tous les types de soudures. Cette méthode utilise un matériau lavable à l’eau, hautement fluorescent, aux qualités de pénétration exceptionnelles.
Ce matériau est appliqué sur la surface propre et sèche du métal à inspecter par brossage, pulvérisation ou trempage. L’excès de matière est éliminé par rinçage, essuyage avec des chiffons propres imbibés d’eau ou sablage. Un révélateur de type humide ou sec est ensuite appliqué. Les discontinuités dans les surfaces correctement nettoyées, traitées avec le pénétrant, rincées et traitées avec le révélateur présentent des indications fluorescentes brillantes sous lumière noire.
Avantages de cette méthode d’essai de soudure physique:
- Bon pour les métaux ferreux et non ferreux
- Faible coût
- Facile à appliquer et à interpréter
- Formation minimale
Inconvénients:
- Peut manquer des problèmes sous la surface
- Ne peut pas fonctionner sur des matériaux poreux
Types de colorants:
- Type A: Fluorescent qui émet de la lumière visible lorsqu’il est vu à l’aide d’une lumière noire
- Type B: Colorant aux couleurs vives qui peut être inspecté à la lumière régulière. Simple à utiliser et bon pour les tests sur le terrain.
Essais de dureté
La dureté peut être définie comme la capacité d’une substance à résister à l’indentation d’un déplacement localisé. Simplement dit, résistance à l’indentation, à l’usure et à l’abrasion. L’essai de dureté habituellement appliqué est un essai non destructif, utilisé principalement en laboratoire et pas dans une large mesure sur le terrain. Les essais de dureté sont utilisés comme moyen de contrôler les propriétés des matériaux utilisés à des fins spécifiques après que la dureté souhaitée a été établie pour l’application particulière.
Un test de dureté est utilisé pour déterminer la dureté du métal de soudure. Par un test minutieux d’un joint soudé, les zones dures peuvent être isolées et l’étendue de l’effet de la chaleur de soudage sur les propriétés du métal de base déterminée.
Équipement d’essai de dureté
Test de fichier:
La méthode la plus simple pour déterminer la dureté comparative est le test de fichier. Elle est réalisée en exécutant une lime sous pression manuelle sur la pièce à tester. Des informations peuvent être obtenues pour savoir si le métal testé est plus dur ou plus mou que la lime ou d’autres matériaux qui ont reçu le même traitement.Machines d’essai de dureté
:
Il existe plusieurs types de machines d’essai de dureté. Chacune d’elles est singulière en ce que sa conception fonctionnelle se prête le mieux au domaine ou à l’application particulière auquel la machine est destinée. Cependant, plus d’un type de machine peut être utilisé sur un métal donné, et les valeurs de dureté obtenues peuvent être corrélées de manière satisfaisante. Deux types de machines sont utilisés le plus souvent dans les tests de laboratoire pour la dureté des métaux: le testeur de dureté Brinell et le testeur de dureté Rockwell.
- Test de dureté Brinelldans les essais Brinell, l’échantillon est monté sur l’enclume de la machine et une charge de 6620 lb (3003 kg) est appliquée contre une bille d’acier trempé qui est en contact avec la surface de l’échantillon testé. La bille d’acier est de 0,4 po. (10,2 mm) de diamètre. On laisse la charge rester 1/2 minute puis on la relâche, et on mesure la profondeur de la dépression faite par la balle sur l’échantillon.Il est à noter que, pour faciliter la détermination de la dureté Brinell, on mesure effectivement le diamètre de la dépression plutôt que la profondeur. Des tableaux des nombres de dureté Brinell ont été préparés pour une gamme de diamètres d’empreinte. Ces graphiques sont couramment utilisés pour déterminer les nombres Brinell.Le nombre de dureté Brinell obtenu est obtenu par la formule suivante:
HB = Numéro de dureté Brinell
D = diamètre de la bille (mm),
d = diamètre de l’indentation circulaire récupérée résultante (mm)
P = charge appliquée (kg) - Test de dureté Rockwell Le principe du testeur Rockwell est essentiellement le même que celui du testeur Brinell. Il diffère du testeur Brinell en ce qu’une charge moindre est appliquée sur une boule plus petite ou un diamant en forme de cône. La profondeur de l’indentation est mesurée et indiquée sur un cadran fixé à la machine. La dureté est exprimée en chiffres arbitraires appelés « nombres de Rockwell. »Ceux-ci sont préfixés par une notation en lettres telle que « B » ou « C » pour indiquer la taille de la balle utilisée, la charge impressionnée et l’échelle utilisée dans le test.
Les autres tests sont la pyramide de diamant Vickers et le scléroscope.
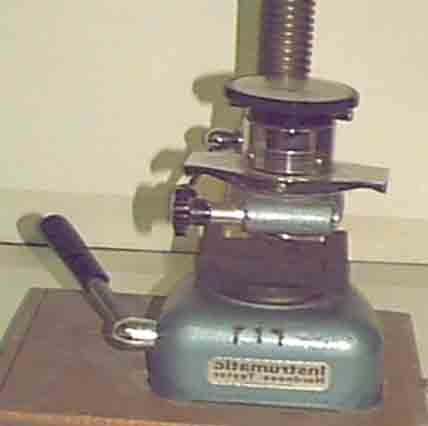
Test Magnaflux
Il s’agit d’une méthode d’essai de soudure physique rapide et non destructive permettant de localiser les défauts à la surface ou à proximité de l’acier et de ses alliages magnétiques au moyen d’une aimantation correcte et de l’application de particules ferromagnétiques.
Principes de base
Dans tous les cas pratiques, l’inspection magnaflux peut être comparée à l’utilisation d’une loupe comme méthode d’essai physique des soudures. Au lieu d’utiliser un verre, cependant, on utilise un champ magnétique et des poudres ferromagnétiques. La méthode d’inspection des particules magnétiques repose sur deux principes: un, qu’un champ magnétique est produit dans un morceau de métal lorsqu’un courant électrique le traverse ou l’entoure; deux, que des pôles minuscules sont installés à la surface du métal partout où ce champ magnétique est brisé ou déformé.
Lorsque des particules ferromagnétiques sont amenées au voisinage d’une pièce aimantée, elles sont fortement attirées par ces pôles et y sont maintenues plus fermement que sur le reste de la surface de la pièce, formant ainsi une indication visible.
Courant de Foucault (Essai électromagnétique)
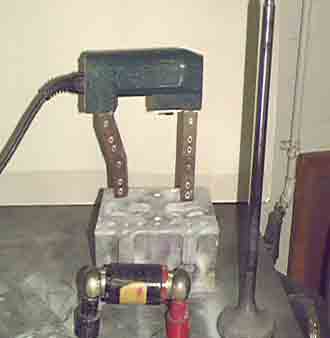
L’essai par courants de Foucault (électromagnétiques) est une méthode d’essai non destructive basée sur le principe qu’un courant électrique circule dans tout conducteur soumis à un champ magnétique changeant. Il est utilisé pour vérifier les soudures dans les matériaux magnétiques et non magnétiques et est particulièrement utile pour tester les barres, les filets, les tuyaux soudés et les tubes. La fréquence peut varier de 50 Hz à 1 MHz, en fonction du type et de l’épaisseur des méthodes actuelles de matériau. Le premier concerne les essais où la perméabilité magnétique d’un matériau est le facteur affectant les résultats des essais et le second les essais où la conductivité électrique est le facteur impliqué.
Les essais de soudure physique non destructifs par des méthodes à courants de Foucault impliquent l’induction de courants électriques (courants de Foucault ou de Foucault) dans une éprouvette et la mesure des changements produits dans ces courants par des discontinuités ou d’autres différences physiques dans l’éprouvette. De tels essais peuvent être utilisés non seulement pour détecter des discontinuités, mais aussi pour mesurer les variations des dimensions et de la résistivité de l’éprouvette. Puisque la résistivité dépend de propriétés telles que la composition chimique (pureté et alliage), l’orientation cristalline, le traitement thermique et la dureté, ces propriétés peuvent également être déterminées indirectement. Les méthodes électromagnétiques sont classées comme méthodes magnéto-inductives et à courants de Foucault. Le premier concerne les essais où la perméabilité magnétique d’un matériau est le facteur affectant les résultats des essais et le second les essais où la conductivité électrique est le facteur impliqué.
Une méthode de production de courants de Foucault dans un échantillon d’essai consiste à faire de l’échantillon le noyau d’une bobine d’induction à courant alternatif (ca). Il existe deux façons de mesurer les changements qui se produisent dans l’ampleur et la distribution de ces courants. La première consiste à mesurer la composante résistive d’impédance de la bobine d’excitation (ou d’une bobine de test secondaire), et la seconde consiste à mesurer la composante inductive d’impédance de la bobine d’excitation (ou d’une bobine secondaire). Des équipements électroniques ont été développés pour mesurer les composants d’impédance résistive ou inductive individuellement ou les deux simultanément.
Les courants de Foucault sont induits dans l’éprouvette conductrice par induction électromagnétique alternative ou action du transformateur. Les courants de Foucault sont de nature électrique et possèdent toutes les propriétés associées aux courants électriques. En générant des courants de Foucault, l’éprouvette, qui doit être un conducteur, est amenée dans le champ d’une bobine porteuse de courant alternatif. La bobine peut entourer la pièce, peut-être sous la forme d’une sonde, ou dans le cas de formes tubulaires, peut-être enroulée pour s’insérer à l’intérieur d’un tube ou d’un tuyau. Un courant de Foucault dans l’échantillon métallique crée également son propre champ magnétique qui s’oppose au champ magnétique d’origine. L’impédance de la bobine d’excitation, ou d’une deuxième bobine couplée à la première, à proximité immédiate de l’échantillon, est affectée par la présence des courants de Foucault induits. Cette deuxième bobine est souvent utilisée pour des raisons de commodité et est appelée bobine de détection ou de ramassage. Le trajet du courant de Foucault est déformé par la présence d’une discontinuité. Une fissure détourne et foule les courants de Foucault. De cette manière, l’impédance apparente de la bobine est modifiée par la présence du défaut. Ce changement peut être mesuré et est utilisé pour donner une indication des défauts ou des différences de structure physique, chimique et métallurgique. Des discontinuités souterraines peuvent également être détectées, mais le courant diminue avec la profondeur.
Test d’émission acoustique
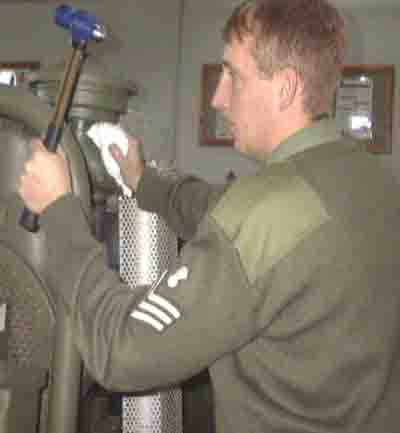
Essais d’émission acoustique (AET) Les méthodes d’essais physiques de soudure sont actuellement considérées comme complémentaires aux autres méthodes d’essais non destructifs. Ils ont cependant été appliqués lors des tests de preuve, des inspections récurrentes, de l’entretien et de la fabrication.
L’essai d’émission acoustique consiste à détecter les signaux acoustiques produits par la déformation plastique ou la formation de fissures pendant le chargement. Ces signaux sont présents dans un large spectre de fréquences avec le bruit ambiant provenant de nombreuses autres sources. Les transducteurs, placés stratégiquement sur une structure, sont activés par des signaux arrivant. Par des procédés de filtrage appropriés, le bruit ambiant dans le signal composite est notamment réduit. Toute source de signaux significatifs est tracée par triangulation en fonction des temps d’arrivée de ces signaux aux différents transducteurs.
Essais de ferrite
Effets de la teneur en ferrite
Les dépôts de soudure en acier inoxydable entièrement austénitique ont tendance à développer de petites fissures même dans des conditions de contrainte minimale. Ces petites fissures ont tendance à être situées transversalement à la ligne de fusion de la soudure dans les passes de soudure et le métal de base qui ont été réchauffés à proximité du point de fusion du matériau par des passes de soudure ultérieures. Les fissures sont clairement des défauts préjudiciables et ne peuvent pas être tolérées. D’autre part, l’effet des fissures sur les performances des soudures est moins clair, car ces micro-fissures sont rapidement brouillées par la matrice austénitique très dure. Les dépôts de soudure fissurés ont fonctionné de manière satisfaisante dans des conditions très sévères. Cependant, une tendance à former des fissures va généralement de pair avec une tendance à une fissuration plus importante, il est donc souvent souhaitable d’éviter les métaux de soudure sensibles aux fissures.
La présence d’une petite fraction de la phase de ferrite delta magnétique dans un dépôt de soudure austénitique (non magnétique) a une influence sur la prévention de la fissuration et de la fissuration de la ligne centrale. La quantité de ferrite delta dans le matériau soudé est largement contrôlée par un équilibre dans la composition du métal de soudure entre les éléments favorisant la ferrite (le chrome, le silicium, le molybdène et le columbium sont les plus courants) et les éléments favorisant l’austénite (le nickel, le manganèse, le carbone et l’azote sont les plus courants). Un excès de ferrite delta peut cependant avoir des effets néfastes sur les propriétés du métal de soudure. Plus la quantité de ferrite delta est importante, plus la ductilité et la ténacité du métal de soudure seront faibles. La ferrite delta est également attaquée préférentiellement dans quelques environnements corrosifs, tels que l’urée. Lors d’une exposition prolongée à des températures comprises entre 482 et 927 ° C (900 et 1700 ° F), la ferrite a tendance à se transformer en partie en un composé intermétallique fragile qui fragilise gravement la soudure.
Les indicateurs de ferrite portables sont conçus pour une utilisation sur site. La teneur en ferrite du dépôt de soudure peut être indiquée en pourcentage de ferrite et peut être placée entre deux valeurs. Cela permet un contrôle suffisant dans la plupart des applications où une teneur minimale en ferrite ou une plage de ferrite est spécifiée.